Dwyer 8600 User Manual
Page 25
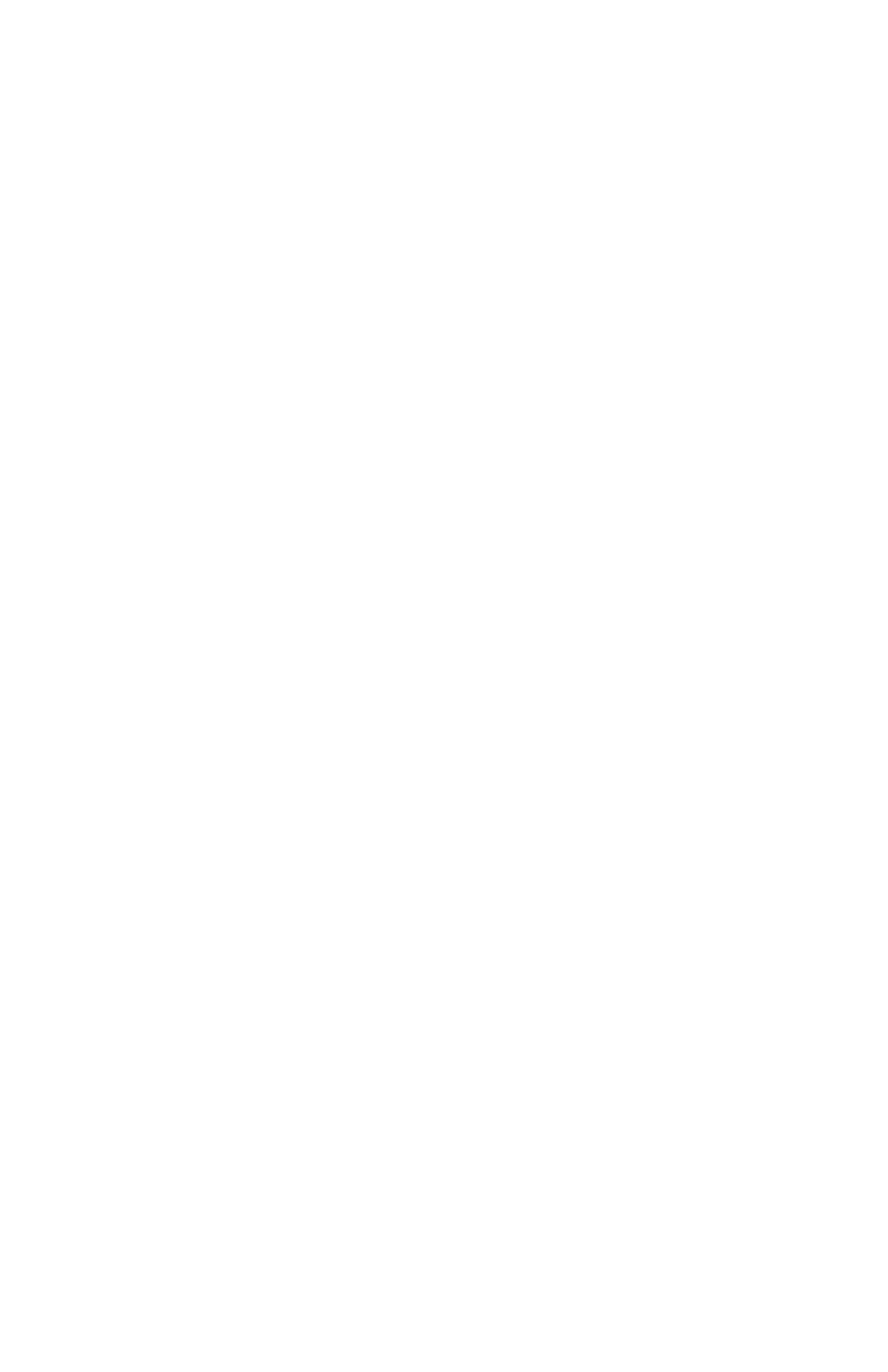
December, 1998
Page 25
949-1277-3
PEnd
Program End action: Select Hold or OoFF.
Hold
Stay at the Present Set Point (16SP).
OoFF
Turn Off SP1 and SP2 Outputs at the end of the program.
LooP
Repeat program starting at 1ti.
SP1
Revert to SP1 value.
InPC
Input Correction: Select ±500 °F, °C, or counts. This feature allows
the input value to be changed to agree with an external reference
or to compensate for sensor error. Note: InPC is reset to zero
when the input type is changed, or when decimal position is
changed.
FiLt
Digital Filter: Select OFF, 1 to 99. In some cases the time constant
of the sensor, or noise could cause the display to jump enough to
be unreadable. A setting of 2 is usually sufficient to provide enough
filtering for most cases, (2 represents approximately a 1 second
time constant). When the 0.1 degree resolution is selected this
should be increased to 4. If this value is set too high, controllability
will suffer.
LPbr
Loop Break Protection: Select OFF, 1 to 9999 seconds. If, during
operation, the output is minimum (0%) or maximum (100%), and the
input moves less than 5°F (3°C) or 5 counts over the time set for LPbr,
the LOOP bAd message will appear. This condition can also be
routed to an Alarm Condition if alarms are present and turned On (see
ALbr in the secure menu). The loop break error can be reset by
pressing the ENTER key when at the LPbr menu item. The INDEX
& ENTER keys may also be used.
POL
(Option 934, 936, Analog Retransmission Output) Process Output
Low: Select -450°F, -260°C, or -1999 counts to any value less than
POH.
POH
(Option 934, 936, Analog Retransmission Output) Process Output
High: Select from any value greater than POL to +9999°F, +5530°C,
or 9999 counts.
POSr
(Option 934, 936, Analog Retransmission Output) Process Output
Source: Select InP or SPt.
InP
Process output follows the Process Variable (input).
SPt
Process Output follows the Set Variable (SP1).