West Control Solutions CALogix User Manual
Page 21
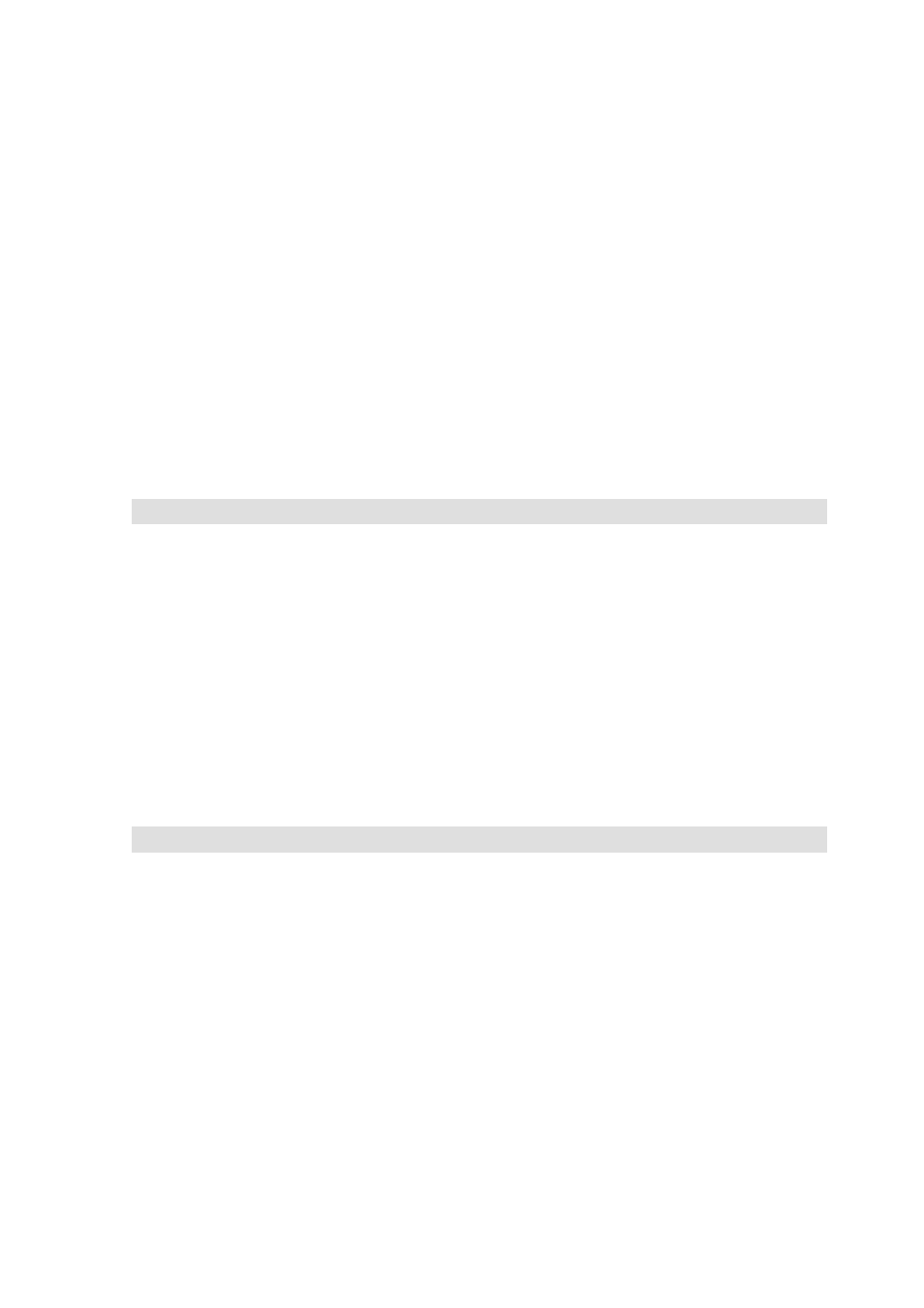
Resolution of PV and Setpoint on CALogix-sw can be set as 0.01, 0.1 or 1. This resolution is also the format used for the corresponding
data register with CALogix unit to be read by an operator panel or for data acquisition. It is recommended that display setting of 0.01 is NOT
used when a thermocouple or PT100 sensor is used as the displayed value will fluctuate.
Setpoint 1 upper limit
Sensor Max
-9999 to 9999 step 0.01
Sets a maximum permissible value for Setpoint 1
Setpoint 1 Lower limit
Sensor Min
-9999 to 9999 step 0.01
Seets a minimum permissible value for Setpoint 1
Span Offset
0.0
-9999 to 9999 step 0.01
Realigns readings to match another instrument e.g. calibration source or meter see note on recalibration.
Zero offset
0.0
-9999 to 9999 step 0.01
Zero sensor error. +ve zero offset increases measured PV, -ve zero offset reduces measured PV, see note on recalibration.
Linear High
50.0
0.0 to 50.0 step 0.1
Configures maximum linear input see Linear inputs
Linear Low
10.0
0.0 to 50.0 step 0.1
Configures minimum linear input, see Linear inputs
Linear high scale
1000
-9999 to 9999 step 0.01
Scale controller to display value at Linear high value
Linear low scale
0
-9999 to 9999 step 0.01
Scale controller to display value at Linear low value
Module * - Output settings
Default
Options
Setpoint 1 output
None
Output 1, Output 2, Output 3
Select physical output to be assigned as Setpoint 1.
Setpoint 2 output
None
Output 1, Output 2, Output 3
Select physical output to be assigned as Setpoint 2
Setpoint 3 output
None
Output 1, Output 2, Output 3
Select physical output to be assigned as Setpoint 3
Output 1, 2 & 3 burnout state
De-energised
De-energised,
Energised
Configure state of outputs on sensor burnout / break
Output 1, 2 & 3 inversion
False
False,
True
Reverse operation of outputs
Output 1 inhibit
None
None, Output 2, Output 3
Prevents other outputs energising at the same time as Output1
Output 1,2 & 3 cycle count
-
Count value (Read only)
Each module internally stores a read-only value of the number of cycles for each output, this can be used to check the estimated remaining
life of a mechanical relay, if fitted.
Module * – Setpoint 1 control
Default
Options
Setpoint
1 0
-9999 to 9999, step 0.01
Change setpoint 1 value
Mode
Park
P, PI, PID, PD, Park, On/Off
Primary control type for setpoint 1
P
Proportional
PI
Proportional
Integral
PID
Proportional
Integral
Derivative
PD
Proportional
Derivative
Park
Holds controller operation – disables output
On/Off
On/Off
Control
Band
10
0 to 9999, step 0.01
SP1 proportional band or Hysteresis -
* 100% sensor maximum, proportional control eliminates the cycling of on-off control. Output power
is varied, by proportioning action, across the proportional band
Integral Time
5 mins
0 to 9999, step 0.1
SP1 integral time/reset -
Auto-corrects proportional control offset error
Derivative time
25 secs
0 to 200, step 1
SP1 derivative time/rate -
Suppresses overshoot and speeds response to disturbances
DAC
2
0.5 to 8, step 0.5
SP1 derivative approach control dAC -
Tunes warm-up characteristics, independent of normal operating conditions, by adjusting
when derivative action starts during start-up (smaller dAC value = nearer setpoint).
Page 21 of 44