West Control Solutions CALogix User Manual
Page 19
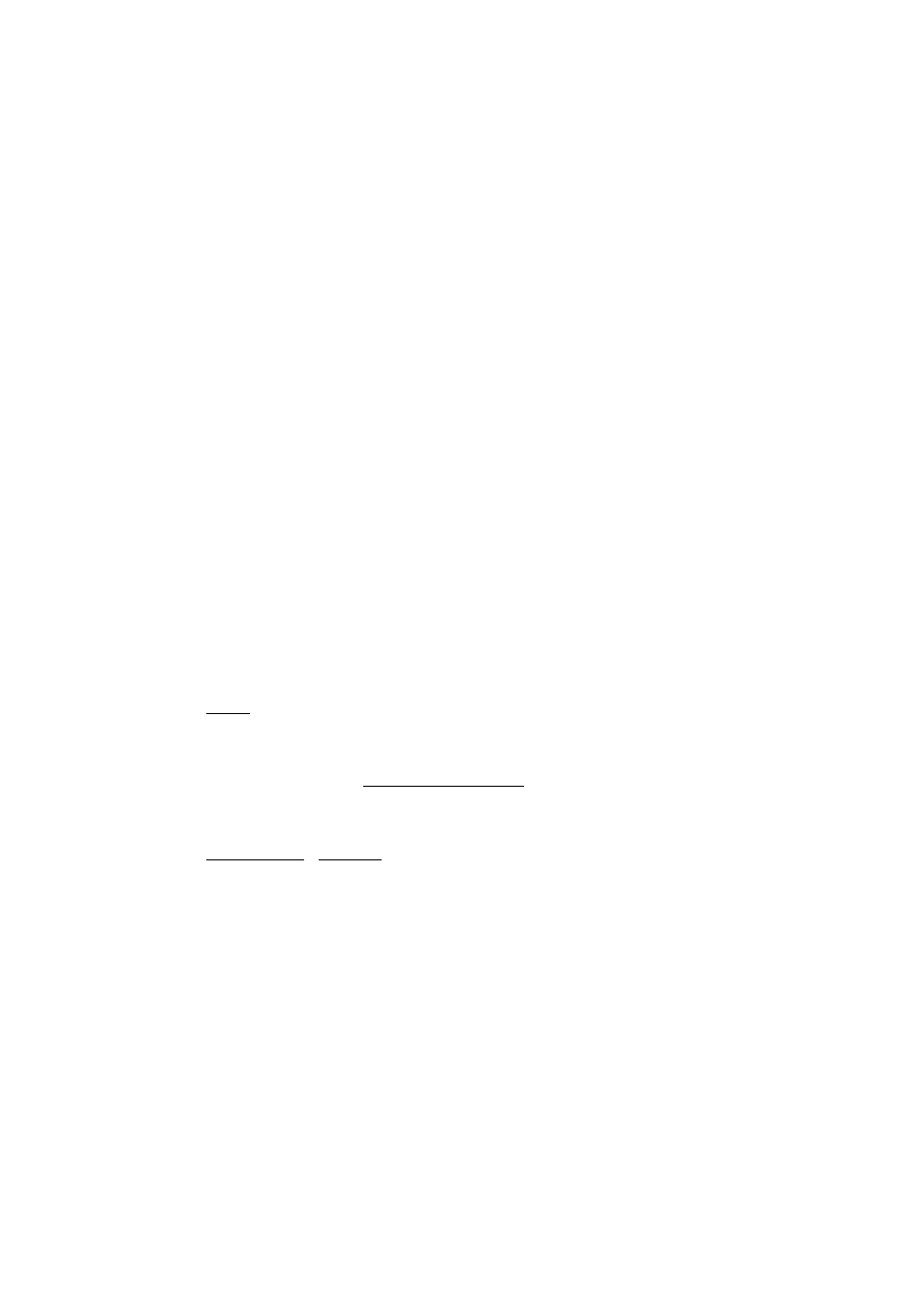
Autotune sets PID terms for Heat and Cool with the same setting values. Band, integral time, derivative time, DAC and
derivative sensitivity
settings can all be modified independently for both heat (setpoint 1 settings) and cool (setpoint 2
settings).
In some processes oscillations occur during cooling. If this occurs double the value of band (setpoint 2 settings).
If no improvement return band (SP2) to its original value and half the cycle time (setpoint 2 settings)
If the process hunts between heating and cooling a deadband setting may be needed. Enter a small value e.g.1 for
Setpoint 2
(setpoint 2 settings)
Water cooled applications
Water cooled applications at temperatures greater than 100°C may suffer from the non linear effect caused by water
turning to steam. This can be countered by setting subsidiary mode (setpoint 2 settings) to NLIN.
Multi zone applications
When tuning multi zone applications like extruders, distortions due to thermal interaction between adjacent zones can be
minimised by running autotune on all controllers at the same time.
RECALIBRATION
F
If the controller and instrument readings are different, the zero and span (input settings) will require adjustment.
Adjust zero to make an equal adjustment across the full scale of the controller and/or span to make a correction where
the error increases or decreases across the scale.
1. To adjust the zero function substitute the measured values in the expression
Instrument reading
− controller reading = zero
Example
: Instrument reading = 245
Controller reading = 250
245
− 250 = −5
Adjust
zero
to -5 to correct the error.
2. Adjusting
the
span
function i.e. to make a correction when errors are different across the scale.
a) Choose a temperature near the bottom and another near the top of the scale
b) Run the process at the lower temperature (T1). Note the error (E1) between the controller and the instrument
readings.
c) Check value of setpoint 1 upper limit (SP1UL) in input settings menu.
d) Repeat at the upper temperature (T2) and note error (E2)
e) Substitute the values for T1, T2, E1, E2 in the expression below;
E2
− E1 X SP1UL = span
T2
− T1
Example T1
T2
Instrument reading
58
385
Controller reading
60
400
.
Error
E1
=
−2
E2
=
−15
Substituting values in the formula
(
−15) − (−2) x 450 = (−13) x 450 = −17.9
385
− 58
327
Therefore adjust span to
−18 to correct error.
Notes:
1. After making the adjustment the reading will immediately change. Allow time for the temperature to stabalise at T2
before making any further adjustment. At this point zero adjustment may be needed, refer to step 1 above.
2. Check that the temperature correctly stabalises at T2 and then adjust setpoints to T1. If an error is present at T1
repeat from step 2.
LINEAR INPUT
Modules can be ordered with analog inputs for use with other field devices and instruments. Check the specification of the
device providing the input to ensure it is compatible.
Set-up Procedure
− 4-20mA
The 4–20mA input model converts current into voltage using an internal resistor which spreads the signal across
the input range 10 to 50 mV using a multiplier of 2.5. When using a transducer with an output less than 4–20mA,
the input maximum and minimum mV values can be calculated using the same multiplication factor.
Page 19 of 44