A' 'b – KROHNE BM 90 EN User Manual
Page 23
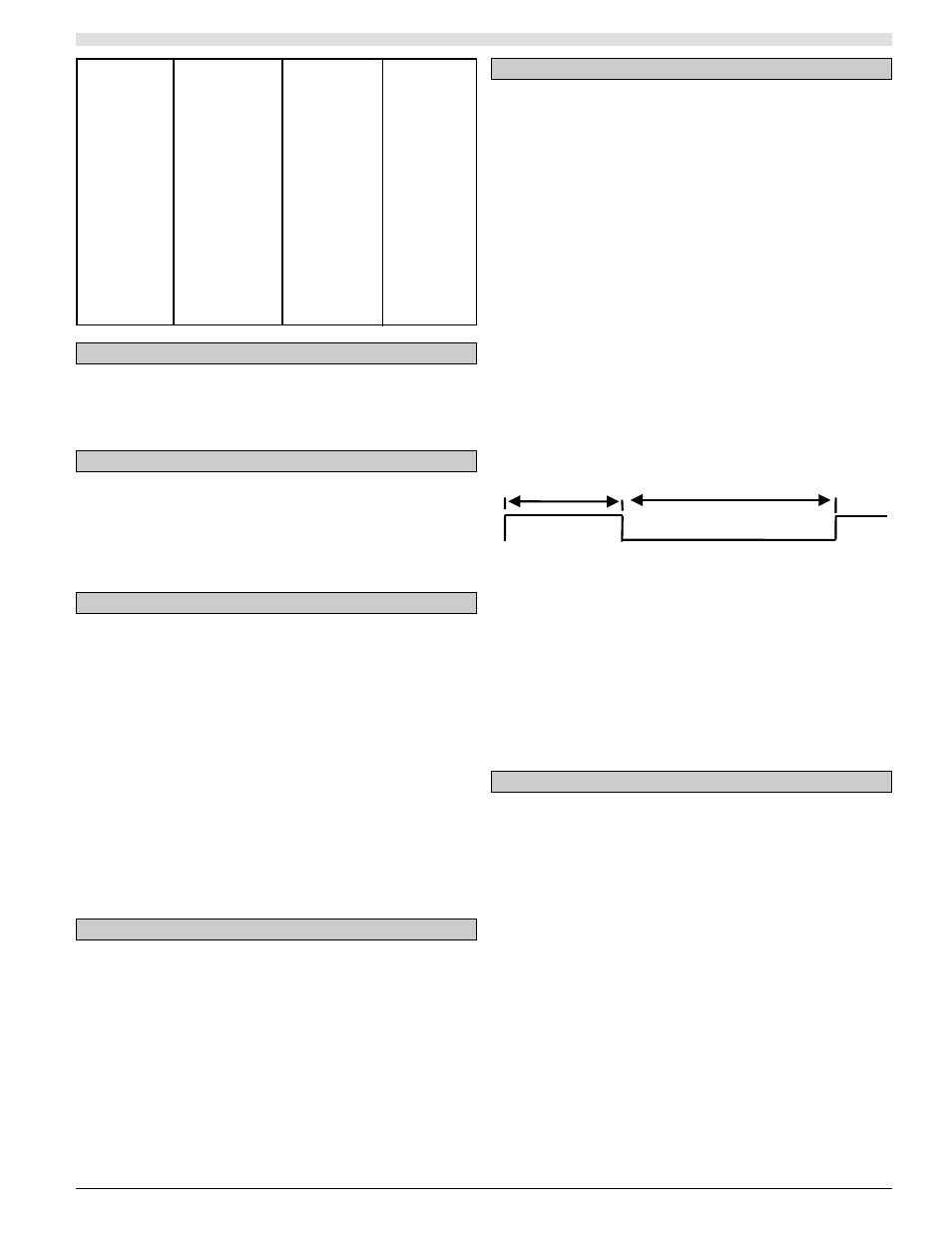
23
Pr. 46 Maximum Flow Rate (D=0)
Pr. 47 Time Base of Maximum Flow Rate (D=1)
Pr. 48 Totalizer Display Conversion (D=0)
Pr.49
Control External Counter (D=0.00)
Used to totalise on the display in flow units larger than
those entered at Pr.46 (max. flow rate)
Enter
0
Multiples by 1
1
Multiples by 0.1
2
Multiples by 0.01
3
Multiples by 0.001
4
Multiples by 0.0001
5
Multiples by 0.00001
6
Multiples by 0.000001
7
Multiples by 0.0000001
e.g. If Pr.46 is entered as litres, at Pr.48 enter ‘3‘ to total-
ize the flow in cubic meters.
Enter the maximum flow rate in units per second, per
minute, per hour or per day, corresponding to maximum
head, set at Pr.4 and then define the time base at Pr.47.
Enter the value corresponding to the flow rate time base.
Enter 1 =
units per second
2 =
units per minute
3 =
units per hour
4 =
units per day
If Pr.20 is set to 5, "Totaliser Drive", then enter the
amount which each relay trip is to represent in totalised
units. See example 5 on page 39.
e.g.
If "litres" entered at Pr.46 and Pr.48 is ’0’ then to
totalise in cubic metres enter 1000.
If an entry is made at Pr.48 for the internal totaliser then
to use the same unit for an external counter enter ’1’.
After making entries in Pr.49, go to Pr.98 to clear and ini-
tiate totaliser.
Flume K
Factor
Flume K
Factor
Size-Inches
for US GPM
Size-Feet
for US GPM
1
3.22
10
331.60
2
6.45
12
393.70
3
9.46
15
486.90
6
18.20
20
642.10
9
30.80
30
797.40
12
40.90
40
1263.00
18
58.90
50
1574.00
24
76.30
36
110.00
48
142.00
72
204.70
96
256.60
Pr. 50 Penstock Control (D=1)
Enter
1 - No drive
2 - Penstock control
The control system uses relays 1 and 2 to drive a pen-
stock up and down respectively to maintain the flow in a
channel within certain limits.
The designations for relays 1 and 2 are ignored, but the
following values have to be set.
Pr.9
: Top flow limit
) In units defined by
Pr.10
: Bottom flow limit
) Pr.46 entry
Pr.12
: Width of drive pulse (seconds)
Pr.13
: Time between drive pulses (seconds)
See example 4.6 on page 32.
The penstock drive consists of a pulse train of variable
time base which drives the penstock up and down.
'a'
'b'
In order to even out the wear of pumps it is possible to
alternate the sequence in which pumps are used. (Pr.52
must be set to 1).
Enter
1
Sequence by set points (i.e. no alternation)
2
Alternate RL1 and RL2
3
Alternate RL1, RL2 and RL3
4
Alternate RL1, RL2, RL3 and RL4
5
Alternate RL1, RL2, RL3, RL4 and RL5
Pr. 51 Pump Sequencing (D=1)
The time ’a’ is set by Pr.12 and ’b’ is set by Pr.13 in sec-
onds, this allows any shape drive train to be defined.
The control will maintain the flow between two limits, a
high limit set by Pr.9 and a low limit set by Pr.10.
If the flow exceeds the value in Pr.9 relay 2 drives the
penstock down. If the flow is below the value in Pr.10
relay 1 drives the penstock up. See Example 6.