Condec UPC5110 User Manual
Page 24
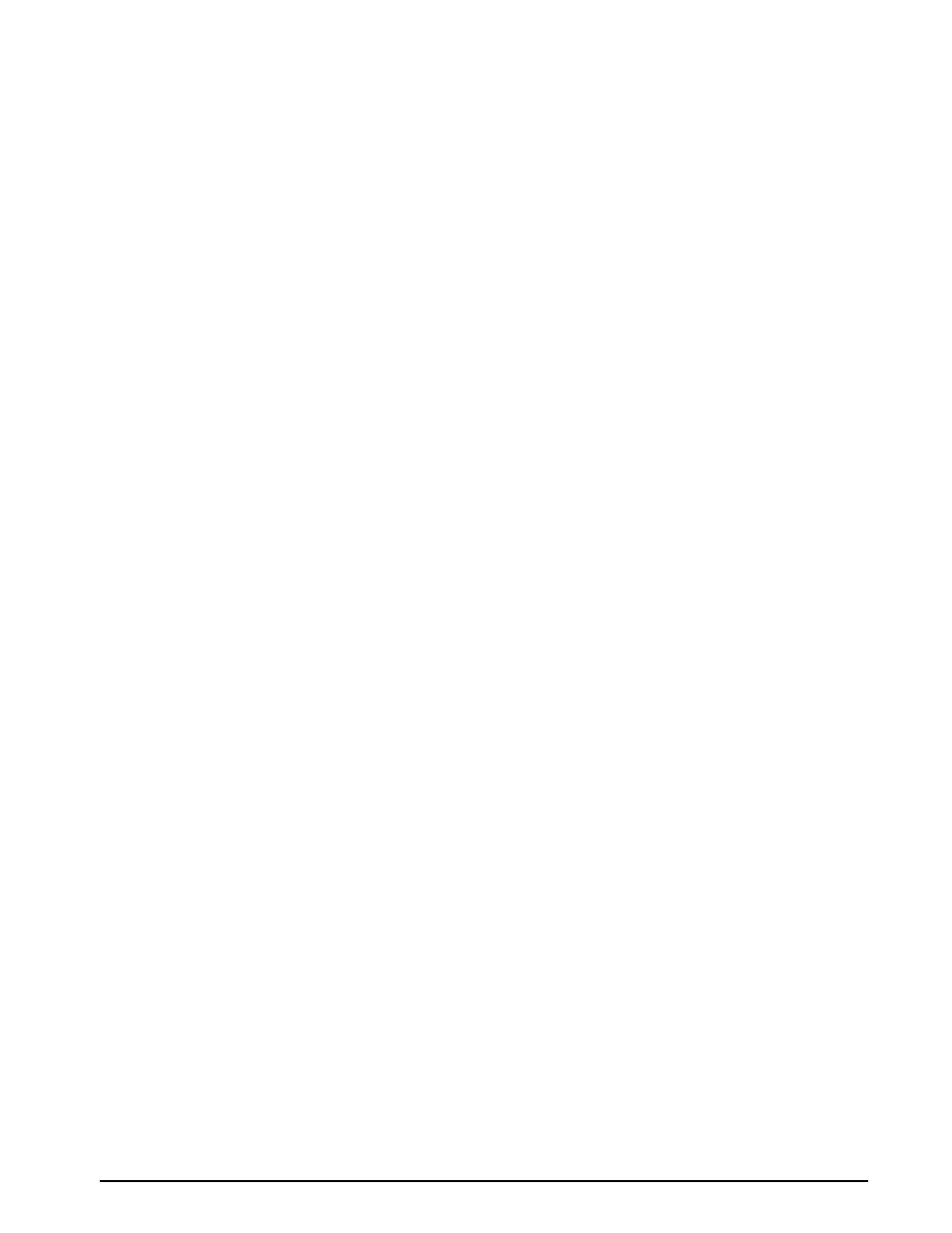
Maintenance and Service
21
4.2.10
Chassis Mounted Regulator (PN 55502) - Removal, Installation and Adjustment
Tools required:
channel locks
adjustable wrench
flat blade screwdriver (small)
7/16" open end wrench
9/16 " open end wrench
hex wrench (1/4")
A/R 1/4" wide Teflon tape, (PN 60575)
A/R 1/2" wide Teflon tape, (PN 60911)
snoop, liquid leak gas detector (PN 64781)
1/2" socket
socket wrench
plug fitting (PN 69199)
Removal:
1. Vent any remaining nitrogen from cylinder to atmosphere. Disconnect power cord from power source.
2. Remove front panel from its enclosure as described in Section 4.2.1 on page 14, and carefully place on a
bench top.
3. Note the orientation and remove the tubing sections that connect to the regulator inlet and outlet fittings.
4. Loosen and remove the locknut using channel locks while holding the assembly from bottom of chassis.
5. Remove the regulator by sliding out from the panel rear.
6. Remove rupture disk identification label and mount the regulator in a bench vise by the flats in the base.
7. Note the orientation of the inlet and outlet fittings in the regulator. Remove the fittings and any remnants
of Teflon tape from the pipe threads.
Installation:
NOTE:
After installation regulator must be adjusted for an output pressure of 150-155 PSI.
1. If applicable, remove top cap, loosen locknut on shaft with 1/2" socket. Remove shaft locknut, and knob.
Discard top cap and knob. Replace shaft locknut finger tight.
2. Wrap two layers of Teflon tape on the pipe threads of each fitting and install into the inlet and outlet of
the regulator and ensure that each is oriented properly (same as old regulator assembly). Use a bench
vise when doing this.
3. Replace rupture disk identification label on bottom of regulator and use wire to hold in place.
4. Remove large locknut from body and insert the new regulator into the chassis through bottom of
mounting hole.
5. Orient assembly such that Burst Disk is perpendicular to fill port side of panel. Verify MODE SELECT
assembly does not interfere.
6. Tighten the locknut using channel locks while holding the assembly from bottom of chassis.
7. Install the tubing sections to the inlet and outlet fittings.
8. Fill the cylinder to approximately 1000 PSIG and check all fittings for leaks. If there are no leaks, vent
unit and continue to adjustment procedure.
Adjustment:
NOTE:
Customer must supply: Standard which has, test port and display capable of reading the test port pressure. A
regulated N
2
pressure source of 250 PSI with an on-off valve. 5/32" O.D. Nylon tube with a .025 wall rated at a minimum
working pressure of 275 PSI. Fittings to go from the nylon tubing to the test port on the customer’s standard.
1. Verify COARSE valve and PRESSURE LIMIT MONITOR are closed. To close PRESSURE LIMIT
MONITOR pull regulator knob outward and turn counter-clockwise. When closed, push knob inward.
VENT valve should be left open.
2. Rotate SUPPLY SELECT to N
2
position.
3. Turn customer supplied N
2
source valve to the off position, vent pressure line, then install line to fill port
of UPC5100/UPC5110.