Warning – Pro-Cut Warthog User Manual
Page 24
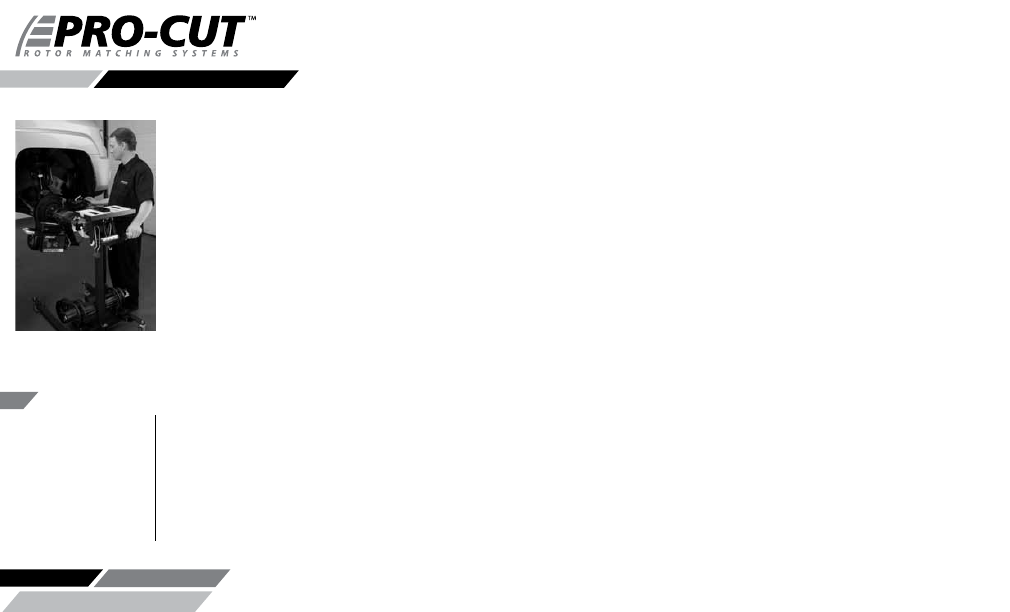
PG /
Ø24
800.543.6618
MACHINING ROTORS
Step 4: MAKE THE CUT
(4 Minutes)
With the motor still running, loosen the forward lock lever on the cutting head to allow cutting depth
adjustment.
STEP 4. Technician sets cut
depth.
*SPINDLE GUARD 50-
1740 NOT SHOWN!
1.
It is extremely important
not to touch the hat of
the rotor with the outer
tool holder. This will
damage or break the tool
holder plate. This type of
damage is
NOT COVER
BY THE WARRANTY.
WARNING
Turn cut-depth knobs counter-clockwise until the tips can clear both sides of the rotor. Crank the cutting
head in to the middle of the braking surface of the rotor.
Start with the inside (behind the rotor) tool arm. Turn the depth knob clockwise (tighten) until the tool tip
just barely makes contact (scratches) with the rotor surface. You can listen for the contact. Next move
the outside tool arm in until it also makes contact.
Now advance the cutting head in towards the center of the rotor making a "running light scratch". If there
is a large ridge on the outer edge of the rotor, you may remove that as well by manually feeding the cutting
head slowly over that ridge. Be careful not to crank the cutting arms into the “hat” of the rotor.
Damage
caused by advancing the cutting arm into the hat of the rotor is not covered by warranty.
When you are at the inside edge of the pad contact surface, you may adjust for depth by turning the depth
knobs clockwise. Each line of the knob represents cutting tip movement of 0.0025” / 0.064mm. Cut
at least 0.005” / 0.13mm (or two lines) on each side with each pass. The maximum depth is 0.020” /
0.51mm per side, per pass. The exceptions to this rule would be extremely large and thick rotors such
as on a Medium Duty truck like the Ford F550 or larger, or very thin solid rotors such as on the rear of a
Cadillac DeVille. In these applications, the depth rule is reversed and the minimum cut can be reduced to
0.0025” / 0.13mm per side per pass, and the maximum cut depth should be limited to 0.005” per side
per pass. Other specialty rotors, such as cross-drilled or slotted, may also require a reduced cut depth.
Note: see our web site for tech-tips on cutting larger and specialty rotors.
2.
3.
4.
5.