3-11. projected calibration at, 3-1. actual ma1, 3-2. actual ma2 – Yokogawa ISC450 4-Wire Analyzer for Inductive Conductivity User Manual
Page 25: 3-3. s1/s2/s3/s4, 3-4. c.c. (factory), 3-5. c.c. (adjusted), 3-6. temp. comp 1, 3-7. temp. comp 2, 3-8. sensor ohms, 3-9. last calibrated at
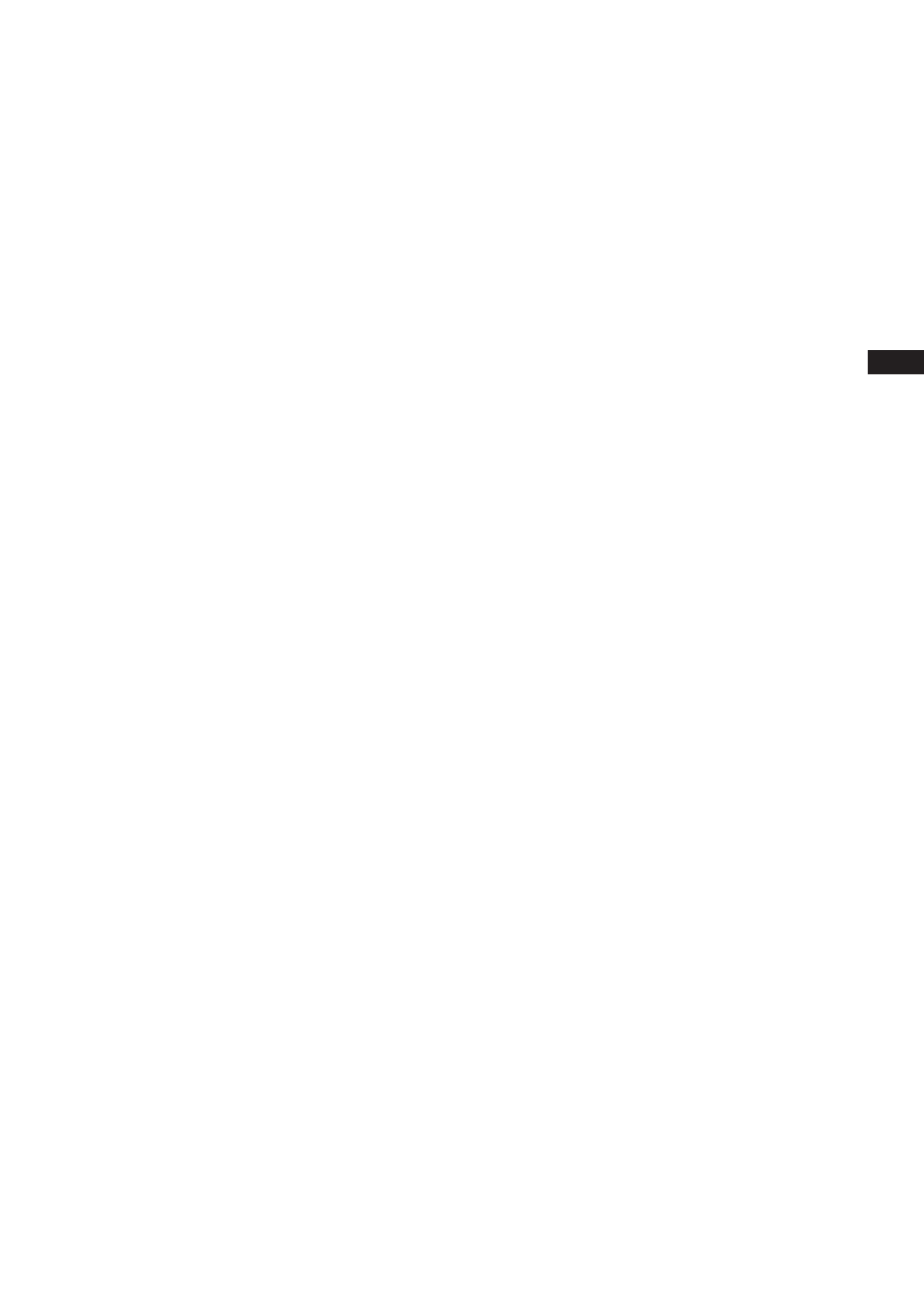
17
IM 12D06D05-01E
4
OPERATION
OF
EXAxt
ISC450G
4-3-1. Actual mA1 = the current output in mA of
the first current output, which is defined as mA1.
The range and function of this mA output can be
set in:
Routing: Commissioning >> Output setup
>> mA1
4-3-2. Actual mA2 = the current output in mA of
the second current output, which is defined as
mA2. The range and function of this mA output
can be set in:
Routing: Commissioning >> Output setup
>> mA2
4-3-3. S1/S2/S3/S4 = the current state of
contacts 1 to 4. The functions and settings of the
contacts can be set in:
Routing: Commissioning >> Output setup
>> S1/S2/S3/S4
4-3-4. C.C. (factory) = the nominal cell constant
as determined by the factory calibration during
production. This value is set during commission-
ing, and is found on the nameplate of the sensor
or the calibration certificate.
Routing: Commissioning >> Measurement
setup >> Configure sensor
4-3-5. C.C. (adjusted) = the calibrated cell
constant. When the cell constant of the system is
adjusted on-line by grab sample or by calibrated
solution technique, the new cell constant is
recorded here. This value should not deviate
greatly from the original factory calibration. In
the event that there is a significant discrepancy
seen between this reading and the C.C. (factory)
value, the sensor should be checked for damage
and cleanliness.
Routing is via the “Calibration” menu.
4-3-6. Temp. comp 1 = the chosen temperature
compensation method for the primary measure-
ment.
Routing: Commissioning >> Measurement
setup >> Temp.compensation
4-3-7. Temp. comp 2 = the chosen temperature
compensation method for the secondary meas-
urement.
Note: This does not imply two separate meas-
urements. There is the possibility to set two
separate compensation methods so that two
different stages of the same process can be
monitored accurately. An example is process/
cleaning fluid interface.
Routing: Commissioning >> Measurement
setup >> Temp.compensation
4-3-8. Sensor ohms = the input measurement
as an uncompensated resistance value.
4-3-9. Last calibrated at = the date of the last
calibration
4-3-10. Calibration due at = in the time frame
scheduled for the next calibration. This field is
determined by the calibration interval.
Routing: Commissioning >> Measurement
setup >> Calibration settings
4-3-11. Projected calibration at =
a diagnostic output, showing the time frame
when the unit should next be maintained ac-
cording to the sophisticated self-diagnostic
tools built into the EXAxt software. Prior to
calibration the sensor should be well cleaned
and rinsed.
4-3-12. HART ID = a part of the HART device ID
(descriptor)
4-3-13. Software revision = the revision level of
the software in the instrument.