Why use a double valve – Ross Controls SERPAR AND CROSSFLOW DOUBLE VALVES SERIES 35 User Manual
Page 3
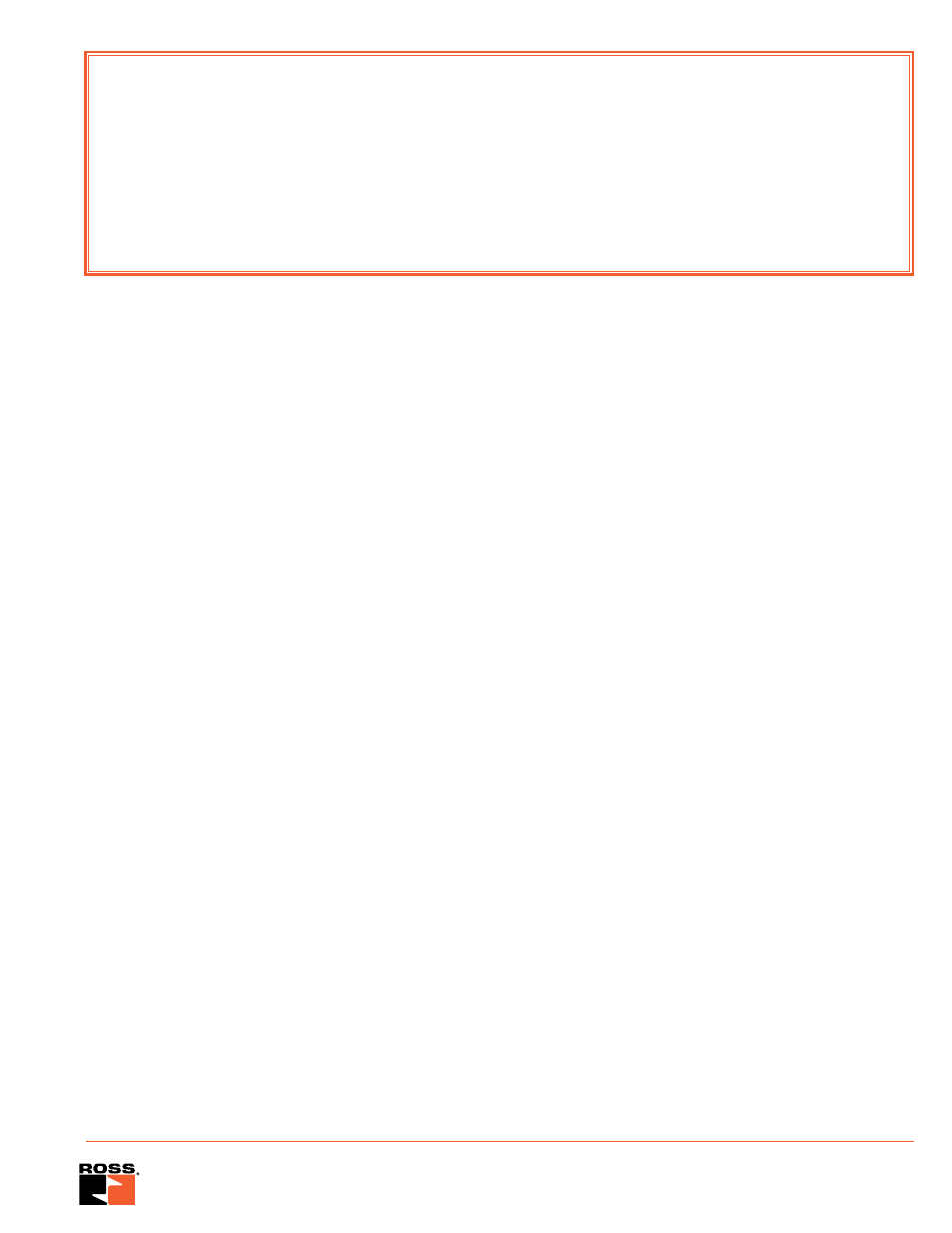
www.rosscontrols.com
3
Why Use A Double Valve?
A double valve is designed to help promote safety in the
operation of many pneumatically controlled machines,
and fully satisfies the OSHA requirements for valves used
on mechanical power presses employing pneumatically
controlled clutch and brake mechanisms.
A ROSS double valve has two valve elements independently
controlled by two solenoid pilot valves. The two valve elements
share common inlet, outlet, and exhaust ports. When the pilot
valves are simultaneously energized, the two main elements are
operated simultaneously so that during normal operation the
valve functions like a three-way valve with a single element.
However, if one of the valve elements does not behave normally
(either failing to open or failing to close), the valve is designed
to keep the pressure on the outlet port at less than two percent
of the inlet pressure. This is an inherent safety characteristic
of ROSS’ double valve design. Valve element redundancy
provides a safety factor as the likelihood of both valve elements
malfunctioning on the same cycle is considered extremely
remote.
IMPORTANT NOTE: A mechanical power press or other
hazardous machines using a pneumatically controlled clutch
and brake mechanism should use a double valve with a self-
contained monitoring device and/or external monitoring system
which inhibits further operation of the valve and machine in the
event of a failure within the valve. Of course, a double valve is
just one of the components in a press control system, and all
other elements of the system should be planned with safety as
a primary consideration.
ROSS double valves, also known as “Control-Reliable” or “Press
Safety” valves, are pneumatic control valves with two internal
elements (redundant), both of which must operate correctly in
order to supply pressure to the outlet port. The general function
of these valves is that of a 3/2 normally closed valve. The main
difference between ROSS double valves and standard pneumatic
valves is that any circumstance which might cause one of the
double valve elements to operate improperly will result in no
output to the work device. This means that solenoid failures,
loose electrical connections, broken wires, contamination inside
the valve body, broken internals or even faulty valve signals will
result in an exhausting or “fail-to-safe” condition.
ROSS double valves come in many shapes and sizes to fit
any safety application. Size 1 and 2 Crossflow
TM
valves with
pressure switches (for external monitoring) are available from
¼” to ¾” port sizes. Externally monitored double valves provide
feedback signals (via the pressure switches), which allows the
main press controls, or separate monitoring device, to check for
proper operation of each valve element on every cycle. Series
35 Serpar
®
valves are internally monitored double valves and
are available in Size 4, 8, 12 and 30 ranging from 3/8” – 1½”
port sizes. Internally monitored double valves contain a built-in
monitoring device that checks for the proper operation of each
valve element. If the internal monitor detects a valve fault on
a particular cycle, the double valve will fail to a safe condition
(all downstream air is exhausted) and the monitor will lock-out
to inhibit further operation of the device. Normal operation can
only be resumed by a momentary reset signal to the valve,
either pneumatic or electric.
The original application for these double valves was in the
control of clutch/brake mechanisms on stamping presses, but
they have found their way into many other critical applications
such as alternative lockout systems for energy isolation, air
cylinder press load-holding systems, as well as other Category
-3 and -4 safety circuits. ROSS double valves are a vital part
of any control-reliable fluid power control system.
Control reliability does not end at the wire. The final element of
control in pneumatic safety systems must be a control-reliable
valve; otherwise the integrity of the entire system is limited. All
Category 4 electrical devices implemented into safety systems
are reduced to Category 1 if they control a standard pneumatic
valve in a critical machine operation. Failure of the standard
pneumatic valve, for example, to become de-energized when a
light curtain is broken could easily result in a hazardous condition.
Consider the ROSS line of double valve and see what we can
do to improve the integrity of your safety equipment.
ROSS Double Valves
The Leader in Double Valve Design
ROSS has long been in the forefront of double valve research and development. For over 54 years ROSS has been responding
to the needs of press manufacturers by supplying double valves of different types. Internal flow patterns have included series
flow, parallel flow, and combined series flow.
Monitoring devices have also been offered in a variety of designs to satisfy differing requirements. The culmination of all this
experience is seen in the present line of SERPAR
®
and Crossflow
TM
double valves described in this brochure.
Selecting the double valve best suited to each application requires considerable technical knowledge. If you need information
or application assistance, please consult ROSS. (See back cover.)