Brooks, Model 5861 i – Brooks Instrument 5861i User Manual
Page 30
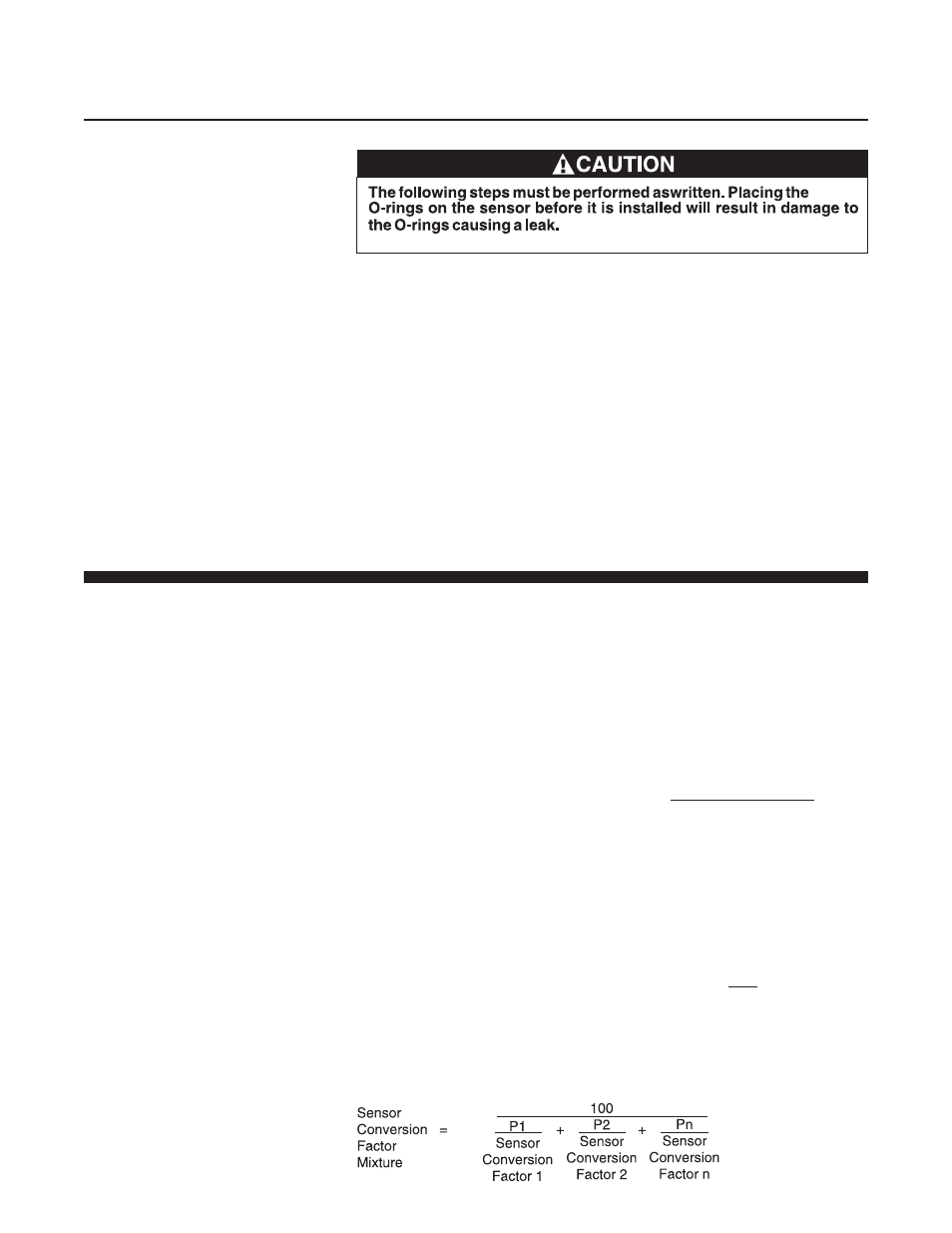
4-6
Installation and Operation Manual
X-TMF-5861i-MFM-eng
Part Number: 541B111AAG
November, 2008
Brooks
®
Model 5861
i
Section 4 Maintenance
6. Press the lubricated sensor O-rings (8) into the flowmeter body (1).
7. Install the sensor assembly (7) as shown in Figure 5-1 and secure with
the 2 allen nuts (9) and washers (10). Tighten the allen nuts to 10 inch
lbs.
8. Install the printed circuit board(28), secure with bracket (26) and 2
screws (27). Plug the connector from the sensor assembly (7) into the
PC board.The flow arrow on the connector should be pointing in the
direction of the flow.
9. Install the electronics cover (40) on the meter and secure with 3 screws
(27).Tighten the upper jack post on the "D" connector.
10. Prior to installation, leak and pressure test the assembled flowmeter to
any applicable pressure vessel codes.
4-5 Use of the Conversion Tables
If a mass flowmeter is operated on a gas other than the gas it was
calibrated with, a scale shift will occur in the relationship between the
output signal and the mass flow rate. This is due to the difference in heat
capacities between the two gases. This scale shift can be approximated by
using the ratio of the molar specific heat of the two gases, or sensor
conversion factor. A list of sensor conversion factors is given in Table 4-3.
To change to a new gas, multiply the output reading by the ratio of the
sensor factor for the desired gas to the sensor factor for the calibration
gas.
Actual gas
=
Output
x
factor of the new gas
flow rate
reading
factor of the calibrated gas
Example:
The flowmeter is calibrated for 100slpm Nitrogen.
The process gas is Carbon Dioxide.
The flowmeter output is 75 % (3.750 volts).
What is the actual carbon dioxide flow?
Actual CO
2
=
75 slpm
x
.773
flow rate
1
= 57.98 slpm
In order to calculate the conversion factor for a gas mixture, the following
formula should be used: