Balancer mode, Chapter 7 – CEMB USA N500 User Manual
Page 43
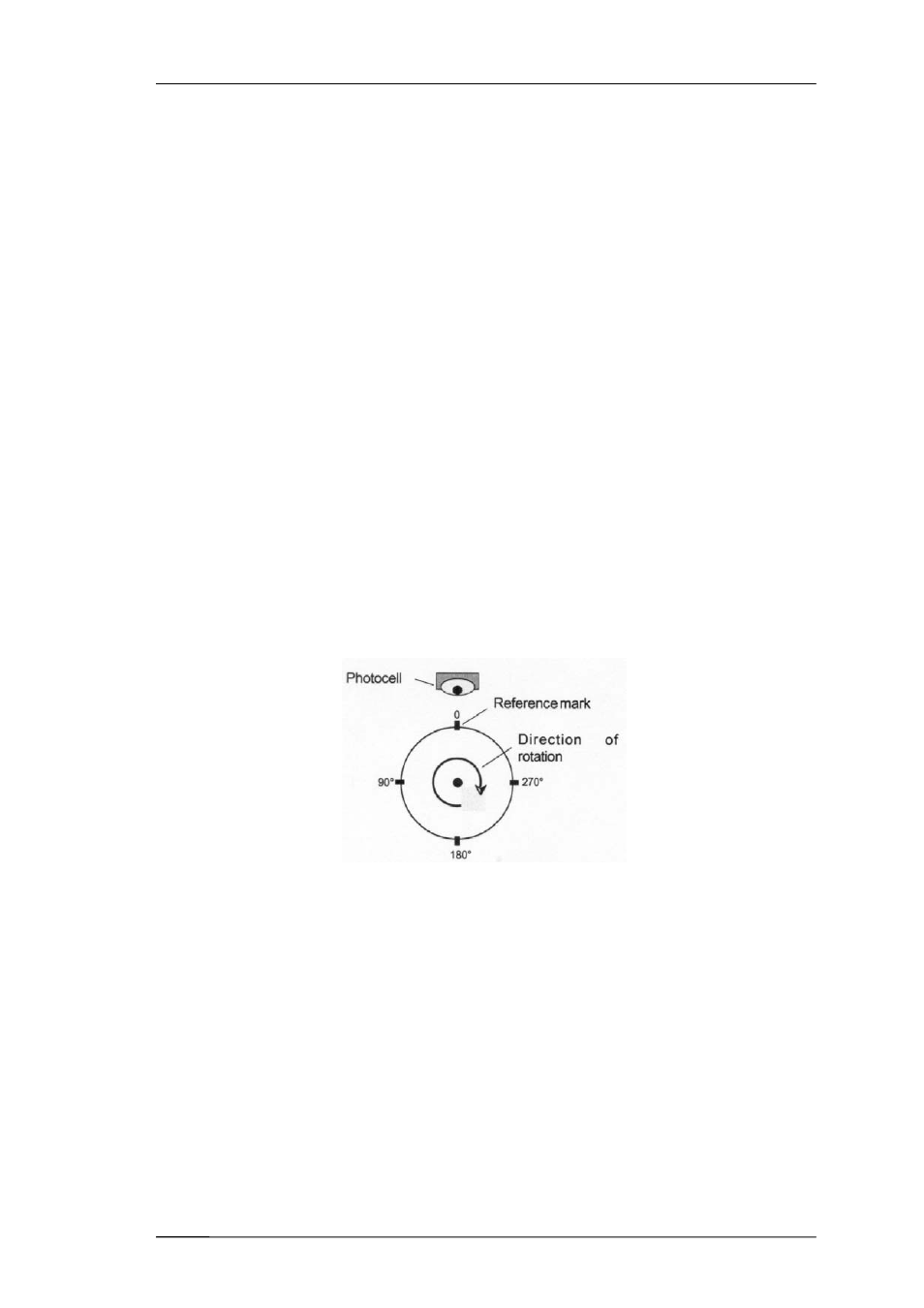
Balancer mode
7 - 1
Chapter 7
Balancer mode
One of the causes of vibration most frequently encountered in actual practice, is the
unbalance of a rotating part (lack of uniformity of the mass about its axis of rotation); such
unbalance can be corrected with a balancing procedure.
The N500 instrument allows balancing any rotor under service conditions in one or two
planes, by using one or two vibration pick-ups and a photocell.
Ad hoc procedures have been drawn up for the most frequent situations (balancing on one
plane with just one sensor and balancing on two planes with two sensors). These
procedures guide the operator step-by-step through the sequence of operations. A general
guided procedure is available for all the other cases (rarely used).
Some rules to be observed in order to perform correct balancing are as follows:
- place the sensors as close as possible to the supports of the rotor to be balanced, by
using the magnetic base or by fastening via a tapped hole to ensure good
repeatability;
- apply a reflecting label on the rotor as reference mark (0°). The angles are measured,
starting from this position, in direction opposite to that of shaft rotation.
–
Connect the photocell and place it in correct position (50 – 400 mm), so that the led
at the back of the photocell lights up only just once per rev. when the light beam
illuminates the reference mark. If operation is incorrect, either retract or approach
the photocell or else incline it with respect to the workpiece surface.
For further consideration, see attached brochure Balancing accuracy for rigid rotors.
The balancing procedure consists of two parts, namely:
–
calibration: a series of spins allows determining the parameters required for balancing
in the case of a given rotor
–
measurement of the unbalance and calculation of the correction.