Data accuracy enhancement, Storage – Atec Agilent-PNA Series User Manual
Page 20
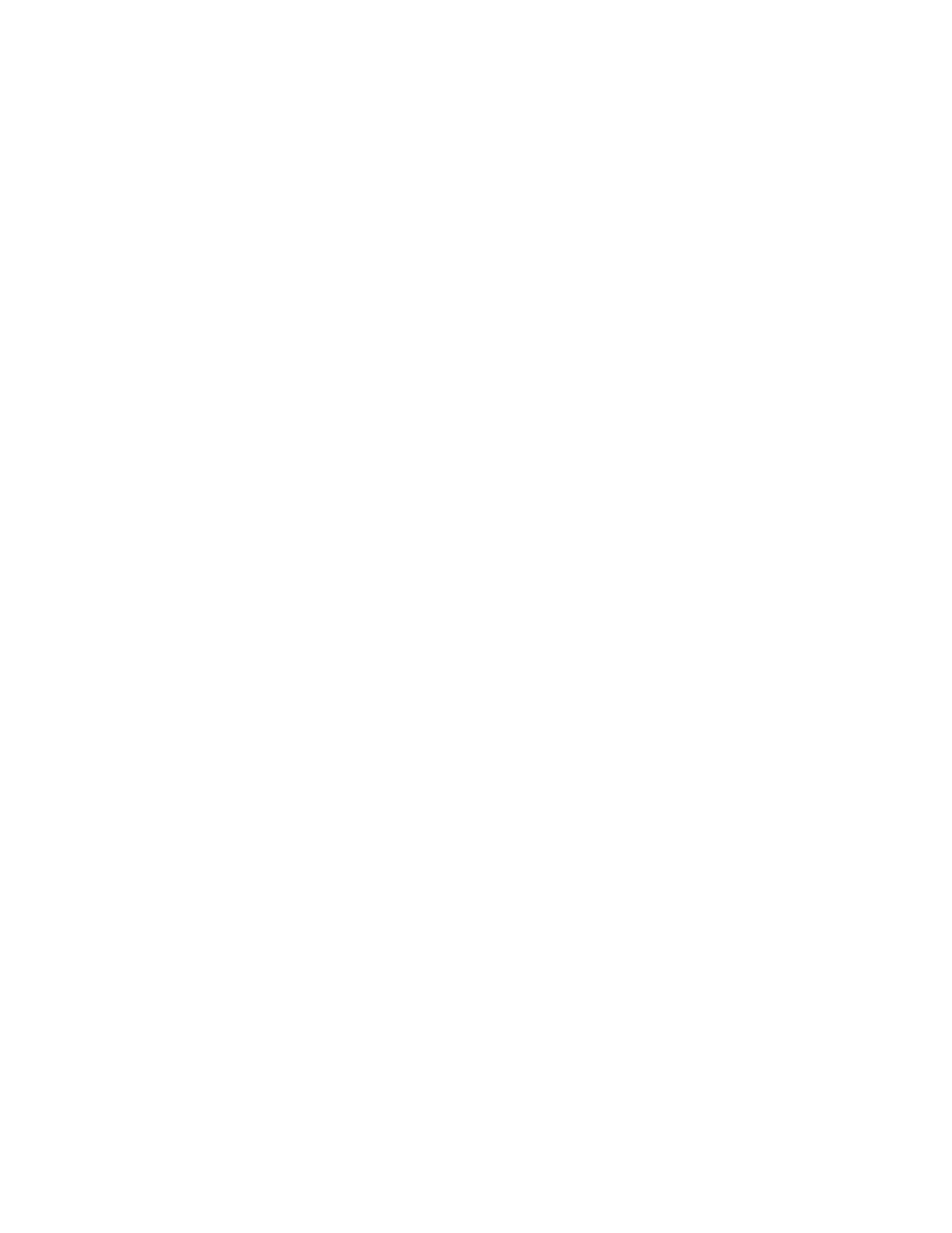
20
Data accuracy enhancement
Measurement calibration
Measurement calibration significantly reduces mea-
surement uncertainty due to errors caused by system
directivity, source and load match, tracking and cross-
talk. Full two-port calibration removes all the sys-
tematic errors to obtain the most accurate measure-
ments.
Calibration types available
Response
Simultaneous magnitude and phase correction of fre-
quency response errors for either reflection or trans-
mission measurements
Response and isolation
Compensates for frequency response and crosstalk
errors of transmission measurements.
One-port calibration
Available on test set port 1 or port 2 to correct for
directivity, frequency response and source match
errors.
Two-port calibration
Compensates for directivity, source match, reflection
tracking, load match, transmission tracking and
crosstalk. Crosstalk calibration can be omitted.
TRL/TRM calibration
Compensates for directivity, reflection and transmis-
sion tracking, source match, load match and crosstalk
in both forward and reverse directions. Provides the
highest accuracy for both coaxial and non-coaxial
environments, such as on-wafer probing, in-fixture
or waveguide measurements.
Interpolated error correction
With any type of accuracy enhancement applied, inter-
polated mode recalculates the error coefficients when
the test frequencies are changed. The number of points
can be increased or decreased and the start/stop fre-
quencies can be changed, but the resulting frequency
range must be within the original calibration frequency
range. System performance is not specified for mea-
surements with interpolated error correction applied.
Velocity factor
Enter the velocity factor to calculate the equivalent
physical length.
Reference port extension
Redefine the measurement plane from the plane where
the calibration was done.
Storage
Internal hard disk drive
Store and recall instrument states and calibration data
on 6 GB, minimum, internal hard drive. Instrument data
can also be saved in binary or ASCII (including S2P)
format. All files are MS-DOS
®
-compatible. Instrument
states include all control settings, active limit lines,
active segment sweep tables, and memory trace data.
Disk drive
Instrument data, instrument states, and calibration
data can be stored on an internal 3.5 inch 1.4MB flop-
py disk in MS-DOS
®
-compatible format.
External storage options
Instrument data, instrument states and calibration
data can also be stored on external CD-RW drive or
servers using Windows
®
2000 drive mapping.
Data hardcopy
Printouts of instrument data are directly produced on
any printer with the appropriate Windows
®
2000 print-
er driver. The analyzer provides USB, parallel, serial
and LAN interfaces.