Veris Industries TURBO SERIES Recordal Install User Manual
Page 4
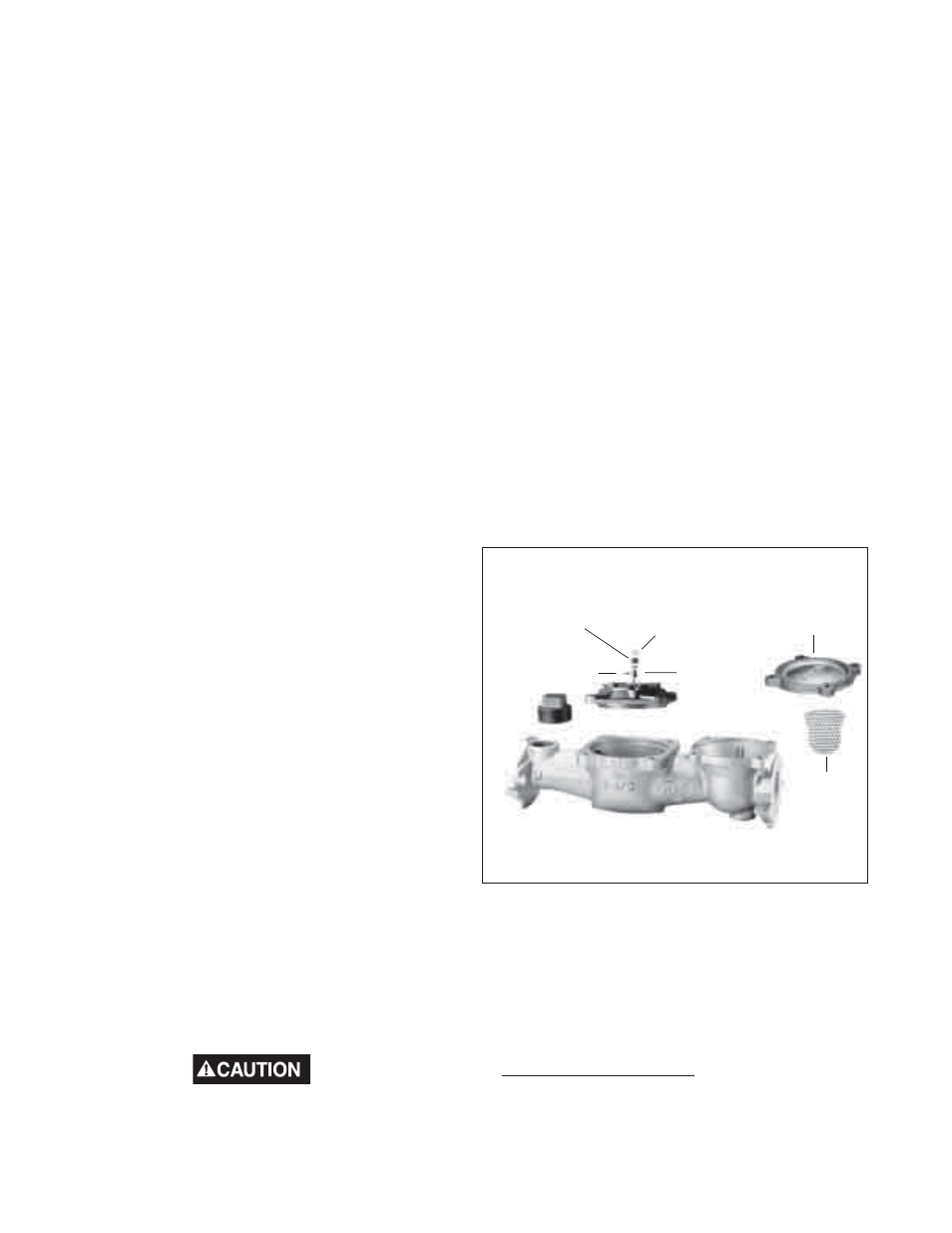
4. Operate the meter until the test tank is filled to the calibrated
level or the predetermined quantity has registered on the calibrated
test meter. Because accuracy may vary slightly with flow rate, it is
recommended that the meter be tested at low, intermediate and high
flows.
5. Record the quantity registered on the meter during the test.
6. Perform the following calculations to determine meter accuracy:
Quantity Registered on Meter
Test Tank or Test Meter Quantity
x 100 =
Meter Accuracy
b. CALIBRATION. The meter's calibration ring is preset at the
factory and sealed. In normal service, it should not have to be reset.
If a retest is required in which a calibrated test stand reveals that the
meter needs recalibration, proceed as follows (see Figure 2):
meter flushing, open the drain valve to relieve pressure
within the meter. If the installation does not have a drain
valve, carefully loosen test plug until it begins leaking.
Stop and wait for pressure to bleed down, then continue
to slowly loosen, making certain pressure is completely
bled off before removing.
1. After installing appropriate connections, meter can be tested
by leaving setting downstream valve closed (if using integral test port),
and slowly opening upstream valve. Finally, the test circuit down-
stream valve can be slowly opened and used to throttle flow for test
purposes.
2. Place a test tank of known volume at the output of the meter.
(An alternative is to connect a calibrated test meter to the output.)
Accuracy testing requires test volumes at least as large as the register
test circle.
3. As in testing the accuracy of any meter, the Recordall Turbo
Series meter must first be purged of air by running water through the
meter.
NOTE
Good test practices are required to perform reliable field
accuracy tests such as those outlined in the AWWA M6
manual. Register "jump" can occur in some instances if
valves are abruptly opened or closed. While this jump is
not accumulative (no affects in service billing), it can
affect accuracy results (1% per division on a one test
circle volumetric test). Care during tests must be taken
to insure this does not occur.
Section III
MAINTENANCE
3-1. GENERAL
This section is limited to information about general preventative
maintenance and calibration procedures for Badger
®
Recordall
®
Turbo
Series meters, whereas instructions for disassembling the meters for
servicing can be found in Section IV. A repair parts list, exploded views
and other illustrations are provided as a supplement to this manual.
3-2. MAINTENANCE EQUIPMENT
The tools and equipment recommended for servicing and mainte-
nance of Recordall Turbo Series meters consist of the usual comple-
ment of hand tools used by plumbers and mechanics.
3-3. PREVENTATIVE MAINTENANCE
The purpose of preventative maintenance is to ensure efficient
operation and long life by detecting and correcting any condition that
may damage the meter or cause it to fail. Maintenance intervals are
a function of the water quality and operating flows experienced by the
meter. Preventative maintenance includes periodic inspection, accu-
racy testing and cleaning procedures.
a. PERIODIC INSPECTION
1. Visually inspect the meter for missing hardware, loose screws,
broken or scratched register lens or any other signs of wear or
deterioration. Replace worn parts as required.
2. Verify that the meter operates at the proper flow rate and
pressure. A loss in pressure coupled with a decrease in flow rate may
indicate that the screen in the upstream strainer or the meter itself is
clogged and needs cleaning.
b. CLEANING
1. Clean all dirt, grease, moisture or other foreign material from
the exterior of the meter. Use a cleaning solvent or volatile mineral
spirits to remove grease or oil. To clean the measuring element, soak
for 12 hours in a mild soap-based cleaner or detergent, and then use
a stiff nylon bristle brush to remove any deposits. After cleaning, rinse
thoroughly with water and dry.
2. In the event that the system pressure has been reduced and the
upstream strainer or meter is clogged, the foreign material must be
flushed out. To flush the strainer, open the cleanout plug and purge the
foreign material with fresh water from the service line. After the strainer
has been cleaned, purge the meter with fresh water and run discharge
out the nearest downstream outlet.
3. Integral Strainer Units. Before attempting service/mainte-
nance of strainer section, system pressure must be removed. See
Section 4-2 to prepare meter for service. After system pressure is
removed, remove cover bolts and cover. Clean out/flush strainer
section of all loose particles/debris. After cleaning is complete,
reinstall screen and reassemble. See Section 2-4 and follow instruc-
tions to return meter to normal service.
3-4. CALIBRATION CHECK AND ADJUSTMENT
The accuracy of Badger Recordall Turbo Series meters is tested at the
factory before shipment. However, after a long period of service, it may
be necessary to recalibrate a meter. The meter can be tested for
accuracy using appropriate connections with either a test tank of
known volume or a test meter. The meter can be tested in the setting
by running output flow through the optional test port, if so equipped.
The Recordall Turbo Series integral calibration mechanism can be
adjusted under line pressure, simplifying and reducing calibration time.
The following instructions are provided to assist in performing a
calibration check and adjustment.
a. ACCURACY TEST
If the optional test port is to be used, upstream and
downstream valves must be closed prior to removing
plug and installing appropriate connections. Failure to
do so can lead to plug being ejected from housing,
causing personal injury and/or property damage. Wher-
ever an installation is equipped with a drain valve for
Figure 2. Calibrating Recordall Turbo Series Meters, shown with
Optional Test Plug
Page 4
CALIBRATION
SHAFT O-RING
CALIBRATION
SHAFT
CALIBRATION
SHAFT SEAL
PLUG
LOCK SCREW
COVER
SCREEN