Veris Industries Badger 200 SERIES Install User Manual
Page 3
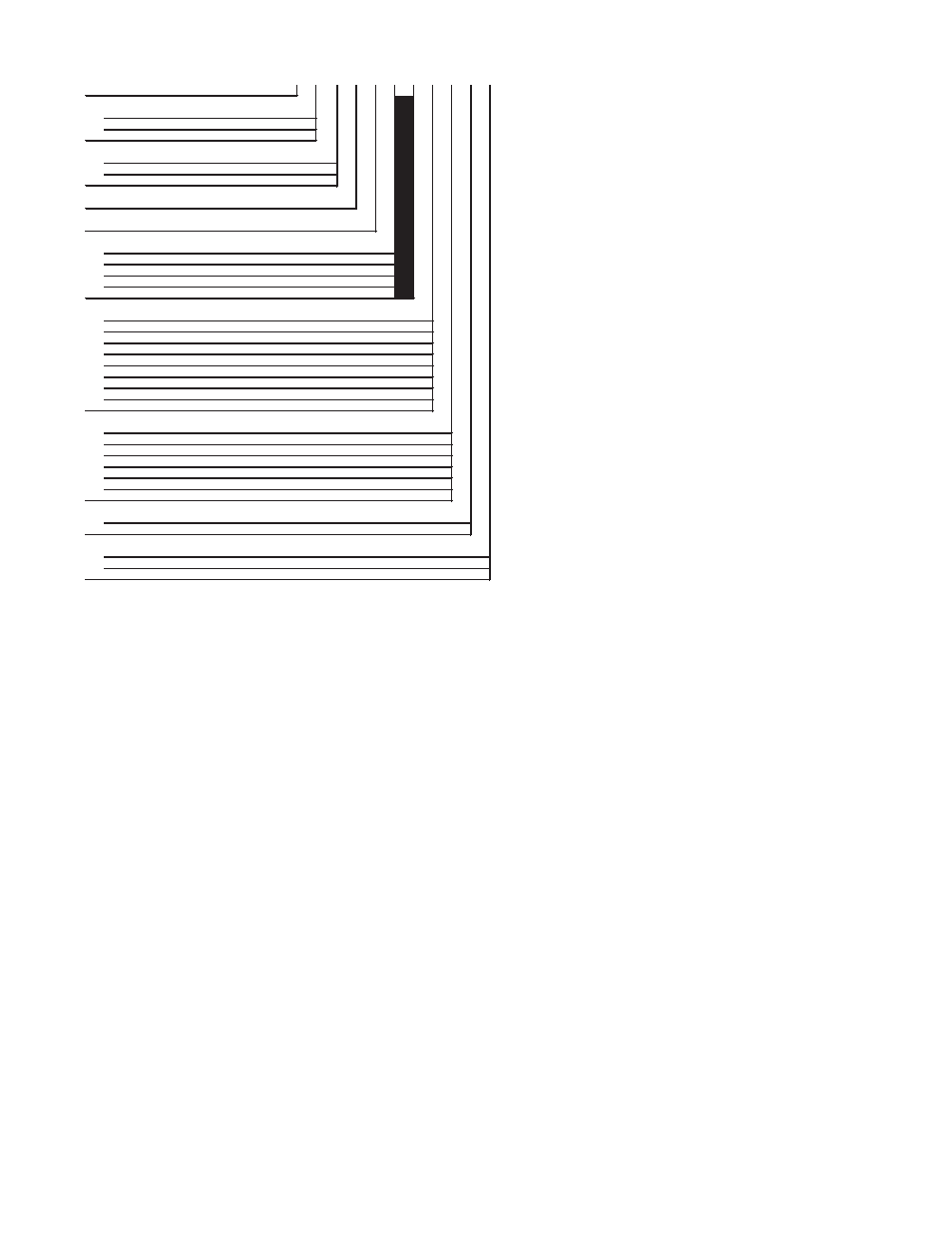
3
200 Series Insert Style Matrix (sizes 2½" and up)
Example: 2
x
x
x
x
x
-
x
x
x
x
STYLE
Short Insert
20
Hot Tap Insert-Gate Valve
25
Hot Tap Insert-Ball Valve
26
MATERIAL
Brass
BR
Stainless Steel
SS
PVC Sleeve w/Stainless Steel Trim
PVS
Size
Insert Style
00
Electronics Housing
PPS
0
ELECTRONICS
Magnetic
2
FM/CSA Approved
4
Standard
5
IR-Irrigation
6
High Temperature
8
O-RING
Viton®
0
EPDM
1
Kalrez®
2
Food Grade Silicon
3
Neoprene
4
Chemraz®
5
Teflon Encapsulated Viton
6
Teflon Encapsulated Silicone
7
Buna N
8
SHAFT
Zirconia Ceramic
0
Hastalloy® C
1
Tungsten Carbide
2
Titanium
3
Monel®
5
316 Stainless Steel
6
Tantalum
7
IMPELLER
Nylon
1
Tefzel®
2
BEARING
Pennlon®
1
Tefzel
2
Teflon®
3
Models 226SS, IR226SS
This is the same as Model 226BR respectively, except that
the hot tap hardware, ball valve, and sensor sleeve are made
of Series 300 stainless steel.
Model HTT
This is the insertion tool for use with any of the hot tap sen-
sor units. It is used to insert and remove the sensor while
under pressure. Generally, only one HTT tool is needed on
each job site.
MECHANICAL INSTALLATION
General
The accuracy of flow measurement for all flow measuring
devices is highly dependent on proper location of the sensor
in the piping system. Irregular flow velocity profiles caused
by valves, fittings, pipe bends, etc. can lead to inaccurate
overall flow rate indications even though local flow velocity
measurement may be accurate. A sensor located in the pipe
where it can be affected by air bubbles, floating debris, or
sediment may not achieve full accuracy and could be dam-
aged. Badger Meter flow sensors are designed to operate
reliably under adverse conditions, but the following recom-
mendations should be followed to ensure maximum system
accuracy:
1) Choose a location along the pipe where 10 pipe diam-
eters upstream and 5 pipe diameters downstream of the
sensor provide no flow disturbance. Pipe bends, valves,
other fittings, pipe enlargements and reductions should
not be present in this length of pipe.
2) The preferred location around the circumference of a hori-
zontal pipe is on top. If trapped air or debris will interfere,
then the sensor should be located further around the pipe
from the top but not more than 45 degrees from top dead
center. The sensor should never be located at the bottom
of the pipe, as sediment may collect there. Locations off
top dead center cause the impeller friction to increase,
which may affect performance at low flow rates. Any
circumferential location is correct for installation in vertical
pipes.
3) An insertion depth of 1 1/2 inches for pipe sizes 2.5
inches and larger is required for accurate flow rate
calibration. Detailed installation instructions for various
sensor mounting configurations on the following pages
include methods for ensuring correct insertion depth.
4) Alignment of the sensor to ensure that impeller rotation
is parallel to flow is important. Alignment instructions are
also included on the following pages.
INSTALLATION FOR 220BR, 220SS
Installation Procedure
The insertion depth and alignment of the sensor assembly
are critical to the accuracy of the flow measurement. The
flat end of the sensor tube assembly MUST BE INSTALLED
1-1/2 inches from the inside wall of the pipe. In order to allow
for variations in wall thickness, lining, or coatings the depth
adjustment is controlled by the position of the Hex Nuts on
the three (3) threaded studs of the hex mounting adapter.
The hex mounting adapter is provided with a 2 inch male
NPT connection.
There are two methods of mounting these Badger Meter
sensors in a 2.5 inch or larger pipe. One is with a 2 inch
NPT threaded pipe saddle. The other is with a welded-on
fitting such as a Thredolet
®
, also tapped for a 2 inch NPT
connection. In either case, cut a 2 inch hole through a
depressurized pipe and then secure the saddle or weld-on
fitting to the pipe. (For drilling into a pressurized pipe, see
instructions for Series 225 and 226 sensors.) Install the 2
inch NPT adapter provided, using a thread sealant to prevent
leakage. Tighten as necessary. Badger Meter insert style
sensors are calibrated with the sensor inserted 1 1/2 inches
into the pipe flow.
To determine the proper insertion depth, proceed as follows:
1) Apply anti-seize thread lubricant , supplied with the
sensor, to the threaded studs of the mounting adap-
tor.
2) Insert the depth gauge into the mounting adapter and set
it against the inside wall of the pipe as shown. Set the
top of the upper adjusting nut to 3¾ inches as measured.
Lock it in place with the bottom nut on the same stud.
Repeat for the other adj. nuts.
Note:
For Model 220PVS: Set nuts 6.5
inches above inside wall of pipe.