York YCAL0041 User Manual
Page 78
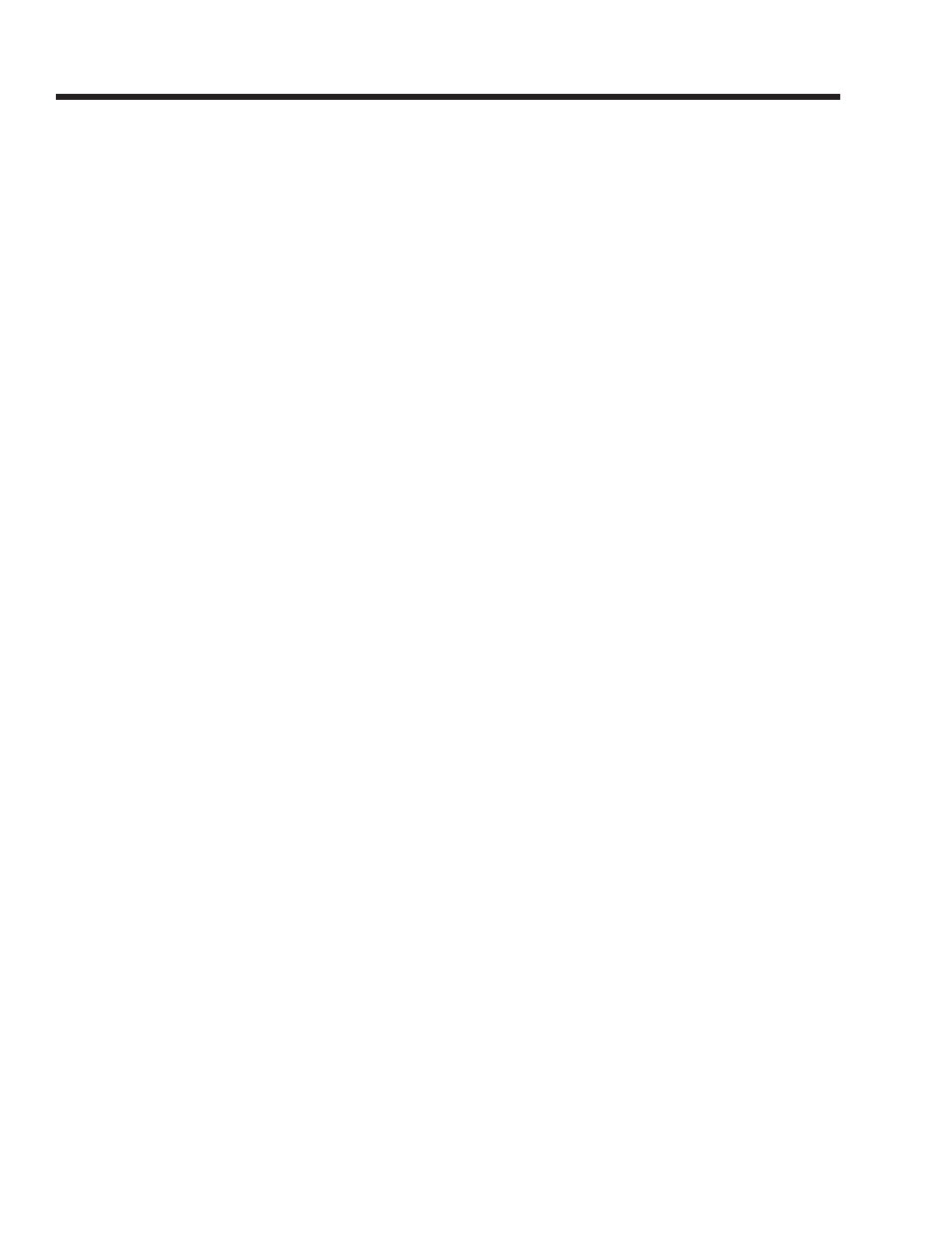
YORK INTERNATIONAL
78
water sensors, and liquid line components (solenoid
valves, filter driers, sight glasses, and TXVs), as
discrete elements of a complete factory system.
Contractor shall be field erect system and provide
interconnecting refrigerant piping and wiring in
accordance with Manufacturer recommendations,
and project plans and schedules. Where not oth-
erwise specified, Contractor provided system piping
shall be in accordance with applicable sections of
ASHRAE Handbook.
O. Hot Gas By-Pass: Permits continuous, stable op-
eration at capacities below the minimum step of
unloading to as low as 5% capacity (depending on
both the unit & operating conditions) by introducing
an artificial load on the cooler. Hot gas by-pass is
installed on only one refrigerant circuit (System
#1).
P. Microprocessor Membrane Keypad Graphics on in
lieu of Standard English:
1. French language.
2. German language.
3. Spanish language.
4. Italian language.
Q. Thermal Storage: Leaving chilled liquid setpoint
range for charge cycle from 25°F to 20°F minimum,
with automatic reset of the leaving brine temperature
up to 40°F above the setpoint. (Works with Option
T)
R. Low Temperature Process Brine: Leaving chilled
liquid setpoint range 20°F to 30°F.
S. Chicago Code Relief Valves to meet Chicago Code
requirements.
T. Building Automation System (EMS) Reset Interface:
Chiller to accept 4 to 20mA, 0 to 10 VDC, or discrete
contact closure input to reset the leaving chilled
liquid temperature.
U. Remote Control Panel (Field-mounted): Auxiliary
panel for remote user interface for functions nor-
mally made at the unit control center. Available on
YCAL0014-0080 models.
V. OptiView Remote Control Panel (Field-mounted):
Graphical interface panel to remotely control and
monitor up to 8 different units.
W. Multi-Unit Sequencing Panel (Field-mounted):
Separate Sequencing control center is provided to
permit control of up to eight chillers in parallel based
on mixed liquid temperature.
X. Sound Reduction (Factory-mounted):
1. Ultra quiet, low speed, reduced noise fans
2. Compressor Acoustic Sound Blankets
Y. Vibration Isolation (Field-mounted):
1. Neoprene Pad Isolators.
2. 1 Inch Deflection Spring Isolators: Level ad-
justable, spring and cage type isolators for
mounting under the unit base rails.
3. 2 Inch Deflection Seismic Isolators: Level ad-
justable, restrained mounts in rugged welded
steel housing with vertical and horizontal limit
stops. Housings shall be designed to withstand
a minimum 1.0g accelerated force in all direc-
tions to 2 inches.
PART 3 - EXECUTION
3.01 INSTALLATION
A. General: Rig and Install in full accordance with
Manufacturers requirements, Project drawings, and
Contract documents.
B. Location: Locate chiller as indicated on drawings,
including cleaning and service maintenance clear-
ance per Manufacturer instructions. Adjust and level
chiller on support structure. If equipment provided
exceeds height of scheduled chiller, installing con-
tractor is responsible for additional costs associated
with extending the height of parapet or screening
walls/enclosures
C. Components: Installing Contractor shall provide and
install all auxiliary devices and accessories for fully
operational chiller.
D. Electrical: Coordinate electrical requirements and
connections for all power feeds with Electrical Con-
tractor (Division 16).
E. Controls: Coordinate all control requirements and
connections with Controls Contractor.
F. Finish: Installing Contractor shall paint damaged and
abraded factory finish with touch-up paint matching
factory finish.