York PREDATOR DJ 150 User Manual
Technical guide, Magnum
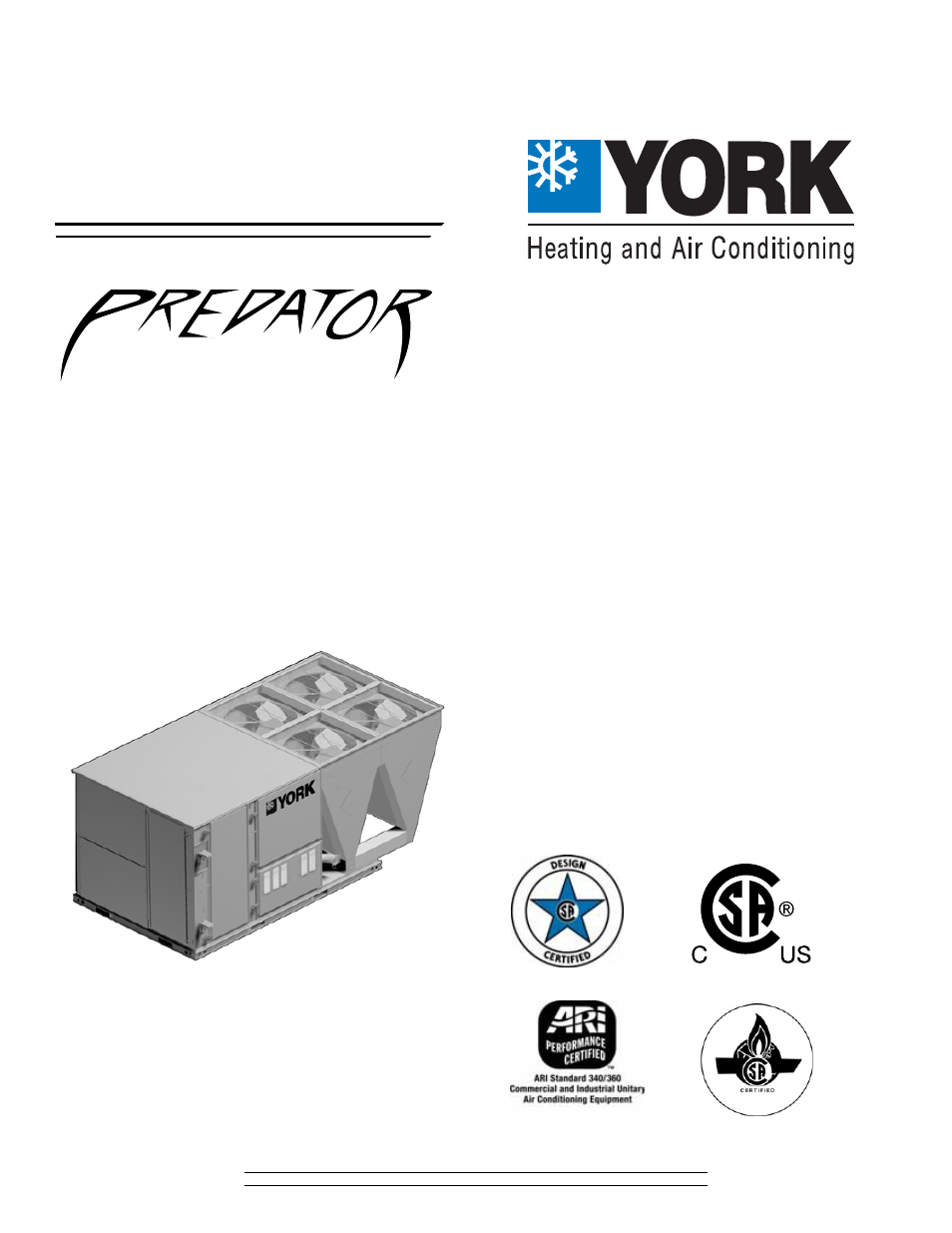
246695-YTG-C-0708
FOR DISTRIBUTION USE ONLY - NOT TO BE USED AT POINT OF RETAIL SALE
ULTRA HIGH EFFICIENCY
SINGLE PACKAGE AIR CONDITIONERS AND
SINGLE PACKAGE GAS/ELECTRIC UNITS
DJ 150
12-1/2 NOMINAL TONS
11.35 EER
TECHNICAL
GUIDE
TECHNICAL
GUIDE
®
MAGNUM
®
DESCRIPTION
YORK
®
Predator
®
Magnum is a convertible single package unit
with a common footprint cabinet and common roof curb for 12-
1/2 ton models. All units have two compressors with indepen-
dent refrigeration circuits to provide 2 stages of cooling. The
units were designed for light commercial applications and can
be easily installed on a roof curb, slab, or frame.
All Predator
®
Magnum units are self-contained and assembled
on rigid full perimeter base rails allowing for 3-way forklift
access and overhead rigging. Every unit is completely charged,
wired, piped, and tested at the factory to provide a quick and
easy field installation.
All units are convertible between side and down airflow. Inde-
pendent economizer designs are used on side and down dis-
charge applications, as well as all tonnage sizes.
Predator
®
Magnum units are available in the following configu-
rations: cooling only, cooling with electric heat, and cooling with
gas heat. Electric heaters are available as factory-installed
options or field-installed accessories.
Tested in accordance with:
Document Outline
- DESCRIPTION
- TABLE OF CONTENTS
- DESCRIPTION 1
- FEATURES 3
- FACTORY INSTALLED OPTIONS 5
- FIELD INSTALLED ACCESSORIES 6
- NOMENCLATURE 9
- MECHANICAL SPECIFICATIONS 26
- LIST OF FIGURES
- Fig. # Pg. #
- 1 Predator® Magnum componeNt location 3
- 2 unit 4 point load 16
- 3 Unit Center of Gravity 16
- 4 unit with 6 point load 16
- 5 Unit Dimensions 17
- 6 Predator® Magnum Roof Curb dimensions 18
- 7 sUNLINE™ TO Predator® Magnum tRANSITION roof curbs 18
- 8 bottom duct openings (from above) 19
- 9 sideflow duct dimensions 19
- 10 downflow economizer hood detail 20
- 11 factory installed Downflow economizer 20
- 12 FIELD INSTALLED Downflow economizer W/POWER EXHAUST 21
- 13 FIELD INSTALLED HORIZONTAL economizer W/POWER EXHAUST 21
- 14 sLAB economizer dOWNFLOW W/POWER EXHAUST 22
- 15 SLAB economizer END RETURN W/POWER EXHAUST 22
- 16 Cooling unit with gas heat wiring 230 V. diagram 23
- 17 cooling unit w/wo electric heat wiring diagram 24
- 18 cooling unit with gas heat wiring 460, 575 & 50 hz diagram 25
- LIST OF TABLES
- Tbl. # Pg. #
- 1 ACCESSORIES 8
- 2 PHYSICAL DATA 10
- 3 dJ 150 (12-1/2 Ton) cAPACITY RATINGS 10
- 4 UNIT VOLTAGE LIMITATIONS 10
- 5 DJ 150 (12 1/2 Ton) COOLING CAPACITY 11
- 6 electrical data dJ150 (12-1/2 ton) W/o PWRD CONVENIENCE OUTLET 12
- 7 electrical data dJ150 (12-1/2 ton) With PWRD CONVENIENCE OUTLET 12
- 8 ELECTRIC HEAT Multipliers 12
- 9 BLOWER PERFORMANCE 12-1/2 TON SIDE DUCT 13
- 10 BLOWER PERFORMANCE 12-1/2 TON DOWNSHOT 14
- 11 Additional static resistance 15
- 12 electric heat MINIMUM SUPPLY AIR CFM 15
- 13 INDOOR BLOWER SPECIFICATIONS 15
- 14 POWER EXHAUST SPECIFICATIONS 15
- 15 4 Point Load Weight 16
- 16 6 Point Load Weight 16
- 17 UNIT WEIGHTS 16
- 18 Unit Clearances 17
- 19 Economizer Usage 20
- FIGURE 1 - Predator® Magnum componeNt location
- FEATURES
- FACTORY INSTALLED OPTIONS
- FIELD INSTALLED ACCESSORIES
- 1. Compressor Lockout (CLO): To prevent mechanical (compressorized) operation of the unit during cold outdoor conditions where there is a risk of returning liquid refrigerant back to the compressors.
- 2. Low Limit Control (LLC): To prevent the supply air from dropping below a specified setpoint by utilizing the units first stage heating means when there is a demand for cooling during cold outside conditions.
- TABLE 1: ACCESSORIES
- NOMENCLATURE
- NOTES FOR TABLEs 9 and TABLE 10:
- TABLE 9: BLOWER PERFORMANCE 12-1/2 TON SIDE DUCT
- TABLE 10: BLOWER PERFORMANCE 12-1/2 TON DOWNSHOT
- TABLE 11: Additional static resistance
- TABLE 12: electric heat MINIMUM SUPPLY AIR CFM
- TABLE 13: INDOOR BLOWER SPECIFICATIONS
- TABLE 14: POWER EXHAUST SPECIFICATIONS
- TABLE 15: 4 Point Load Weight
- TABLE 16: 6 Point Load Weight
- TABLE 17: UNIT WEIGHTS
- TABLE 18: Unit Clearances
- TABLE 19: Economizer Usage
- FIGURE 11 - factory installed Downflow economizer
- FIGURE 12 - FIELD INSTALLED Downflow economizer W/POWER EXHAUST
- FIGURE 13 - FIELD INSTALLED HORIZONTAL economizer W/POWER EXHAUST
- FIGURE 14 - sLAB economizer dOWNFLOW W/POWER EXHAUST
- FIGURE 15 - SLAB economizer END RETURN W/POWER EXHAUST
- FIGURE 16 - Cooling unit with gas heat wiring 230 V. diagram
- FIGURE 17 - cooling unit w/wo electric heat wiring diagram
- FIGURE 18 - cooling unit with gas heat wiring 460, 575 & 50 hz diagram
- MECHANICAL SPECIFICATIONS
- SINGLE PACKAGE AIR COOLED GAS/ELECTRIC UNITS FOR 12.5 NOMINAL TONS
- PREDATOR® MAGNUM - DJ 150
- 11.35 EER
- GENERAL
- DESCRIPTION
- UNIT CABINET
- INDOOR (EVAPORATOR) FAN ASSEMBLY
- OUTDOOR (CONDENSER) FAN ASSEMBLY
- REFRIGERANT COMPONENTS
- a. Shall be scroll type, direct drive, internally protected with internal high-pressure relief and over temperature protection. The hermetic motor shall be suction gas cooled and have a voltage range of + or – 10% of the unit nameplate voltage.
- b. Shall have internal spring isolation and sound muffling to minimize vibration and noise, and be externally isolated on a dedicated, independent mounting.
- a. Evaporator and condenser coils shall have aluminum plate fins mechanically bonded to seamless internally enhanced copper tubes with all joints brazed. Special Phenolic coating shall be available as a factory option.
- b. Evaporator and condenser coils shall be of the direct expansion, draw-thru design.
- a. Independent fixed-orifice or thermally operated expansion devices.
- b. Solid core filter drier/strainer to eliminate any moisture or foreign matter.
- c. Accessible service gage connections on both suction and discharge lines to charge, evacuate, and measure refrigerant pressure during any necessary servicing or troubleshooting, without losing charge.
- d. The unit shall have two independent refrigerant circuits, equally split in 50% capacity increments.
- a. Unit shall be complete with self-contained low-voltage control circuit protected by a resetable circuit breaker on the 24-volt transformer side.
- b. Unit shall incorporate a lockout circuit which provides reset capability at the space thermostat or base unit, should any of the following standard safety devices trip and shut off compressor: (1) loss-of-charge/Low-pressure switch, (2) high-press...
- c. If any of the above safety devices trip, a LED (light-emitting diode) indicator shall flash a diagnostic code that indicates which safety switch has tripped.
- d. Unit shall incorporate “AUTO RESET” compressor over temperature, over current protection.
- e. Unit shall operate with conventional thermostat designs and have a low voltage terminal strip for easy hook-up.
- f. Unit control board shall have on-board diagnostics and fault code display.
- g. Standard controls shall include anti-short cycle and low voltage protection, and permit cooling operation down to 0 °F.
- h. Control board shall monitor each refrigerant safety switch independently.
- i. Control board shall retain last 5 fault codes in non volatile memory, which will not be lost in the event of a power loss.
- GAS HEATING SECTION (If Equipped)
- ELECTRIC HEATING SECTION (If equipped)
- UNIT OPERATING CHARACTERISTICS
- ELECTRICAL REQUIREMENTS
- STANDARD LIMITED WARRANTIES
- ADDITIONAL FACTORY INSTALLED OPTIONS
- OTHER PRE-ENGINEERED ACCESSORIES AVAILABLE