Overview, Installation, Set-up – Omega Engineering CN9400 User Manual
Page 7: Autotune
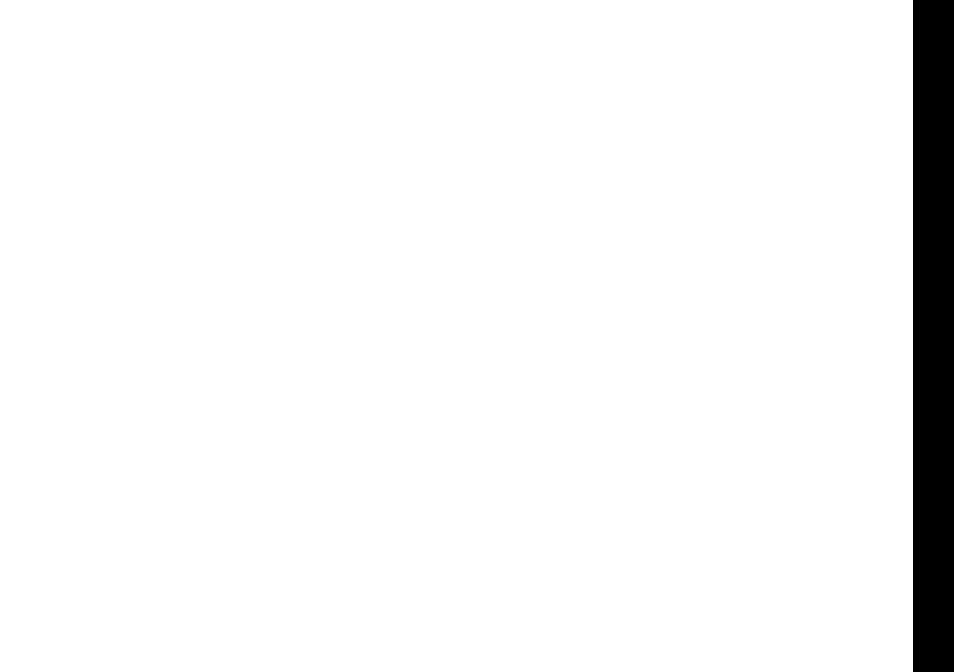
Overview
OVERVIEW
INSTALLATION
The Model CN9400 controller is designed to be mounted in a 1/16
DIN panel cut-out. See the INSTALLATION section.
SET-UP
After installation the controller requires programming with the
following information:
Type of Input Sensor
Operating unit (C or F etc)
Type of Output Device
Temperature Setpoint
Note:
The controller will not be operational until this
information is entered.
When the above information has been programmed into the
controller it will be operational with the following factory PID
(proportional band, integral time, derivative time) settings.
Proportional band/Gain
10°C/18°F
Integral time/Reset
5 mins
Proportional cycle-time
20 secs
Derivative time/Rate
25 secs
DAC Derivative approach control
1.5
AUTOTUNE
To precisely control an application the controller will need to be
‘tuned’ using the built-in ‘AUTOTUNE’ feature. Autotune ‘teaches’
the controller the main characteristics of the process and ‘learns’ by
cycling the output on and off. The results are measured and used to
calculate optimum PID values which are automatically entered in the
controller memory.
During AUTOTUNE the optimum cycle-time is calculated but is not
automatically implemented. The cycle-time requires manual
acceptance unless pre-selected.
To ensure good control over a wide range of applications two
versions of the Autotune program are provided, TUNE and TUNE AT
SETPOINT.
The TUNE method normally achieves the best results. Starting with
the load cool, tuning occurs during warm-up preventing overshoot.
This method of tuning is recommended.
The TUNE AT SETPOINT method is used for specialist applications.
eg. Heat-cool, multizones and processes below 100°C/200°F. During
the tuning cycle some overshoot occurs because the tuning cycle is
at set point.
The DAC setting is not re-calculated.
3