3 troubleshooting for polarity detection errors – Yaskawa Sigma-5 User Manual: Setup for Linear Motors User Manual
Page 157
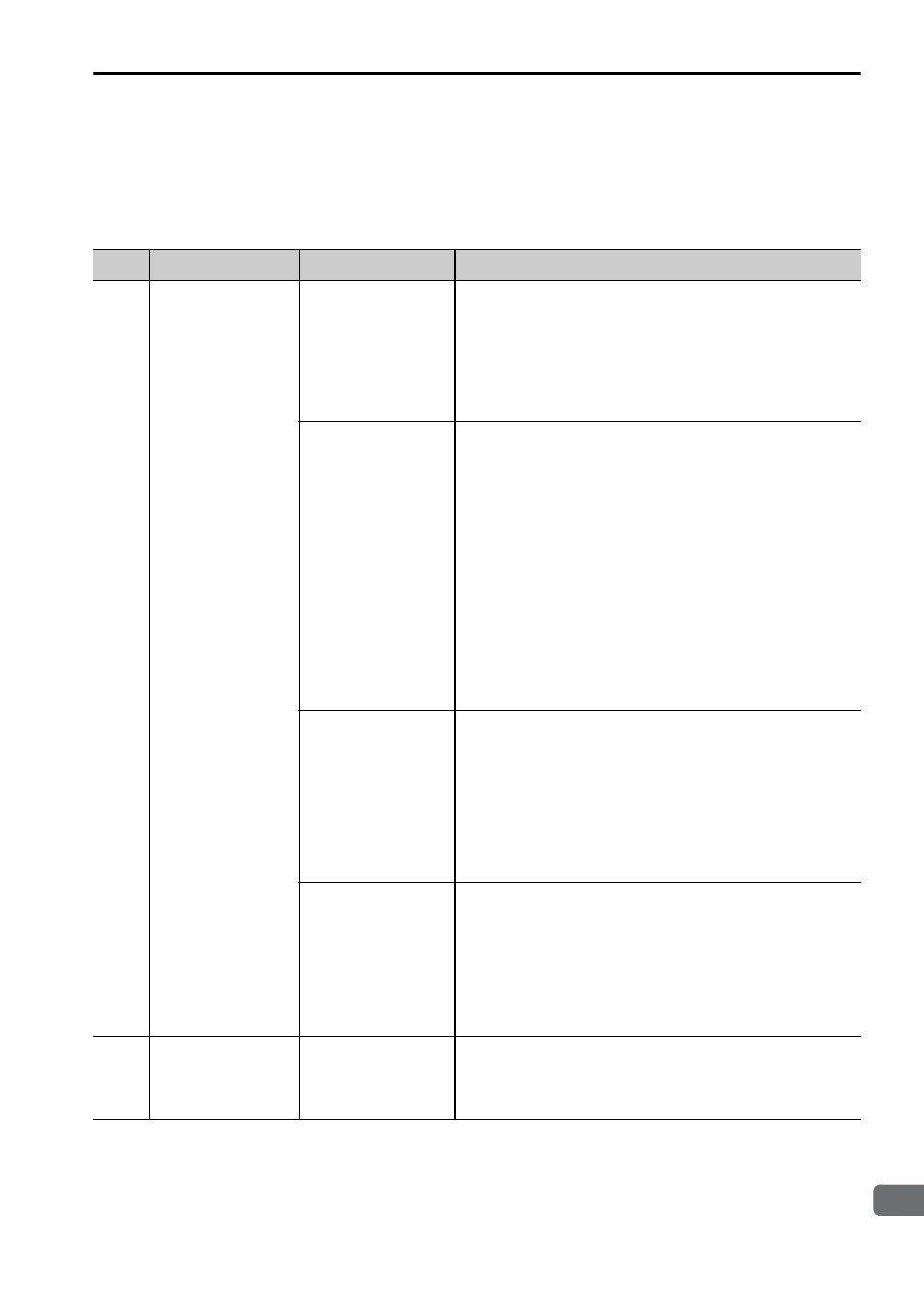
5.5 Polarity Detection
5-21
5
T
rial Operation (Checking Linear Servomotor Operation)
5.5.3 Troubleshooting for Polarity Detection Errors
Refer to the following table for troubleshooting if polarity detection is not completed
normally.
No.
Problem
Cause
Correction
1
Polarity detection
error (A.C50)
Parameter
settings are
incorrect.
The parameter settings may not be appropriate for the
device. Check the following points.
• Pn282 (linear scale pitch) and the linear scale
specifications (Check these only if you are using a
serial converter unit.)
• Pn080.1 (motor phase selection) and the feedback
signal status
Noise is present
in the scale
signal.
When the detection reference is repeatedly output sev-
eral times in the same direction, noise may occur in the
scale signal, resulting in malfunction. Check the fol-
lowing points.
• Make sure that the FG of the serial converter unit is
connected to the FG of the SERVOPACK.
• Make sure that the FG of the linear scale is
connected correctly. Refer to the manual for the
linear scale for details.
• Make sure that the FG of the linear servomotor is
connected to the FG of the SERVOPACK.
• Make sure that the FG of the SERVOPACK is
connected to the FG of the power supply.
• Make sure that the linear scale cable is shielded
properly.
The moving coil is
being subjected to
an external force.
If the moving coil is subjected to a gravity or/and an
external force such as cable tension, and the speed feed-
back is not 0 regardless of a 0 detection reference,
polarity detection will be poor.
Reduce the external force and make the speed feedback
0.
If the external force can not be reduced, increase the
value of the changes in the sequence input signal allo-
cation for each signal (Pn481).
The linear scale
resolution is
rough.
When the linear scale pitch is 100
μm min., the SER-
VOPACK cannot detect correct speed feedback.
Use a linear scale with good scale pitch precision
(within 40
μm is recommended).
Alternatively, increase the value of the polarity detec-
tion reference speed (Pn485).
The range of linear servomotor movement at polarity
detection, however, will increase.
2
Overtravel
detection at
polarity detection
(A.C51)
The OT signal
was detected
during polarity
detection
The alarm A.C51 occurs when the OT signal is detected
during polarity detection. Before executing the polarity
detection, place the motor to the position where the OT
signal is not detected.