Yaskawa A1000 User Manual
Page 26
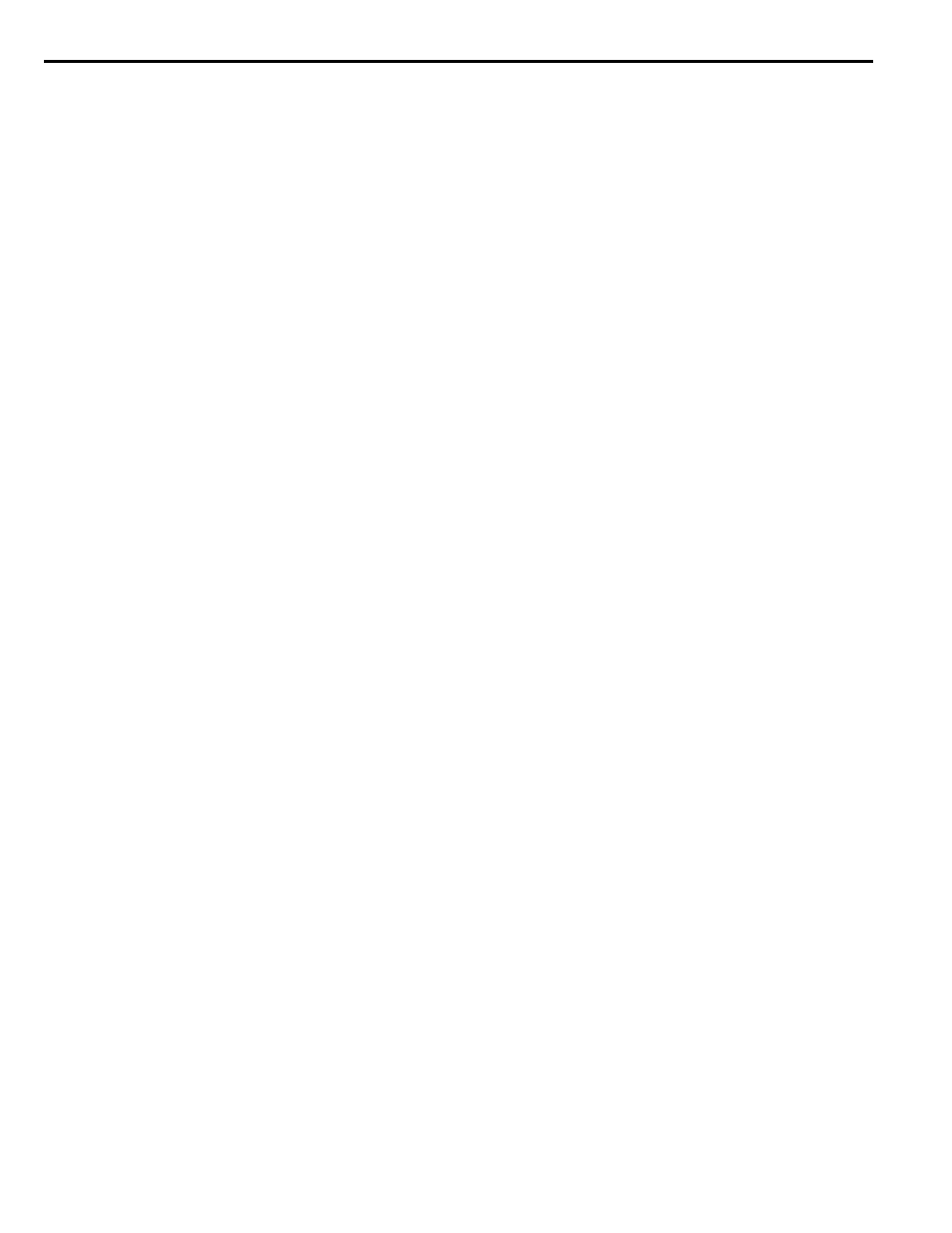
3 Simple Automation Alignment
26
YASKAWA TM.A1000SW.064 Electronic Line Shaft with Alignment A1000 Custom Software Supplement
• When P4-01 is set to 3 - Continuous Alignment. The drive will immediately begin the alignment process when the Run
command is applied. When two valid trigger inputs are received, the drive automatically re-starts the alignment process.
Trigger pulses will be ignored if the drive has not completed the previous alignment.
• When P4-01 is set to 4 - Window Alignment. The drive will perform an alignment at start and measure alignment
during subsequent trigger pulses. When the alignment is off by more than the P4-09 setting, the U7-13 count will
increment. When the alignment is within the P4-09 setting, the U7-13 count will decrement. Alignment is also
performed when the U7-13 count is equal to P4-10, at which time U7-13 is reset to zero.
Alignment Process
The alignment function aligns the follower to the master using fixed trigger positions. This process does not control the
master drive; all corrections are made by the follower drive. The amount of the correction is controlled by the quadrature
counts accumulated from the time when the first or leading trigger starts the process and continues until the trailing
trigger stops it and the speed of the correction is controlled by parameter P4-02, Alignment Trim Rate.
The correction is made when the trailing trigger input becomes active. The rate at which the drive accelerates or
decelerates during the alignment procedure is fixed. For a 1024 PPR encoder, the ramp rate will be approximately 20Hz/
1 sec. The alignment process is intended to be performed at low speeds, but will function as long as the triggers provide at
least a 15 millisecond signal so the follower drive can see the trigger inputs.
Note:
If consecutive master triggers occur before a follower trigger occurs, the first master trigger will be used
and subsequent master triggers will be ignored. If consecutive follower triggers occur before a master
trigger occurs, the first follower trigger will be used and subsequent master triggers will be ignored.
Maximum alignment speed: If an alignment is in process and the follower needs to run faster to catch up to the master, it
will only be allowed to compensate at a rate of up to 95% of the follower’s maximum frequency setting. If the follower is
already running at or above the 95% speed level, the alignment function will not complete.
Minimum alignment speed: If an alignment is in process, and the follower needs to slow down in order for the master to
catch up, the follower drive could run in reverse. If reverse on the follower is disabled (b1-04 = 1), the follower drive will
only be allowed to run at a minimum of zero speed (no reverse).
Alignment Fault Select
When parameter P4-06 is set to 0, “Disabled”, there is no settable limit to the number of follower motor revolutions that
can elapse between master and follower trigger inputs.
Note:
To prevent internal overflow, the maximum number of encoder counts allowed between the two trigger
inputs is 268,435,456. (65,536 motor revolutions with a 1024 PPR encoder).
When parameter P4-06 is set to 1, “Ignore 1st Pulse”, it will disregard the first trigger input (regardless of master or
follower) when the P4-07 distance (either direction) has elapsed.
If the align command is asserted between the time that the master and follower trigger inputs are read and the P4-07
distance elapses, the drive will disregard the first input and wait for two valid trigger inputs. When using this mode, it is
useful to program the P4-07 distance to between 50% and 90% of the total trigger-to-trigger distance.
When parameter P4-06 is set to 2, “Fault”, the drive will fault out on an “AF - Alignment Fault” and coast to stop when
the number of P4-07 revolutions have passed after the first trigger input (regardless of master or follower). When this
mode is used, it is useful to set P4-07 to a value greater than the normal trigger-to-trigger distance.
Align Complete / In Alignment Multi-function Digital Outputs
The “Align Complete” digital output (H2-0
= 41) will close when a successful align procedure has been completed. The
Align Complete digital output will de-energize after detecting the rising edge of an Align Follower Command. If the drive
is set to reset position error at stop (P1-09 = 0), the Align Complete digital output will also de-energize when the Run
command is removed or if electronic line shaft is disabled (H1-
= 80). If the drive is set to accumulate position error
at all times (P1-09 = 1), the Align Complete will de-energize only if electronic line shaft is disabled or another align
command is received.