Troubleshooting, Function descriptions – Yaskawa A1000 User Manual
Page 25
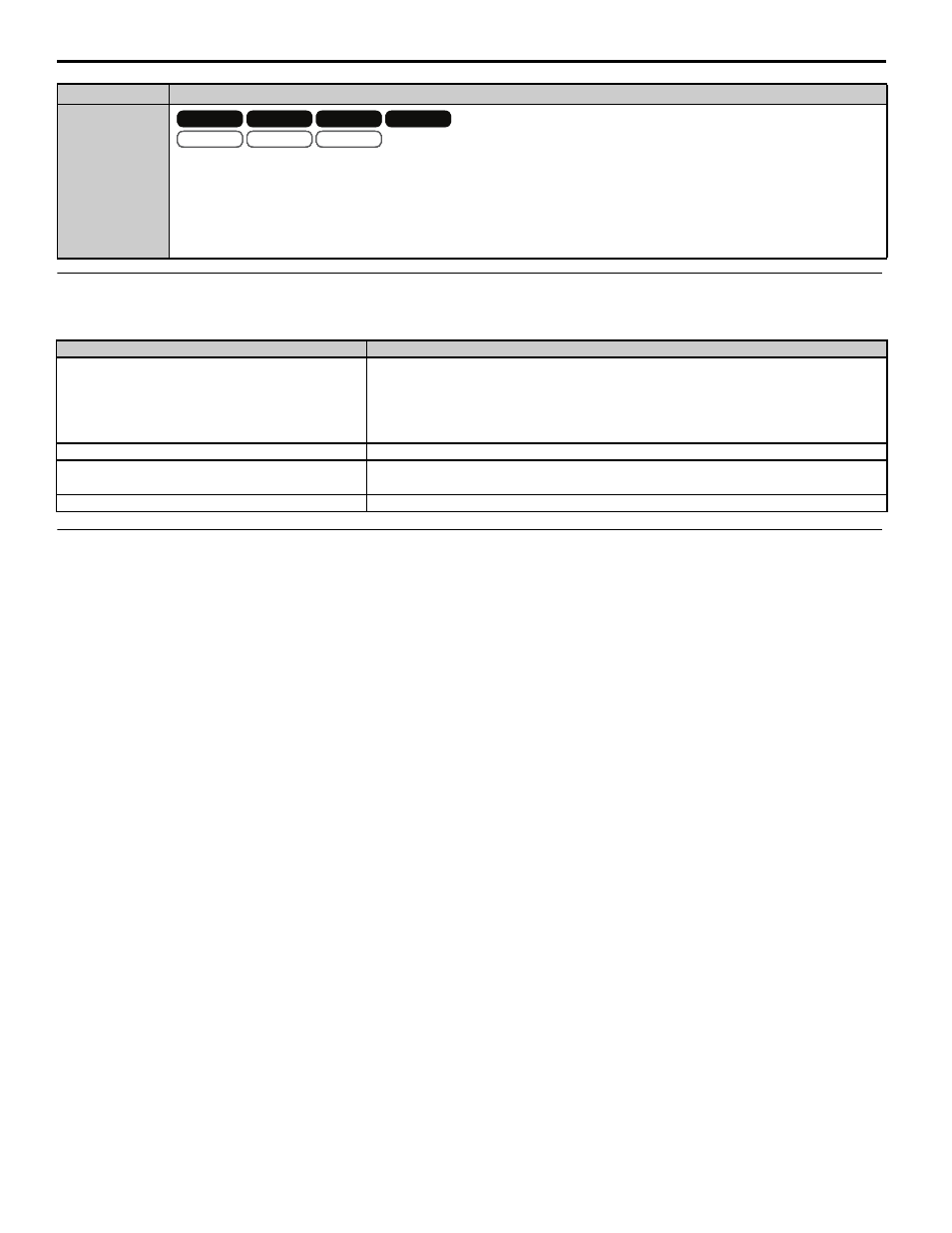
3 Simple Automation Alignment
YASKAWA TM.A1000SW.064 Electronic Line Shaft with Alignment A1000 Custom Software Supplement
25
Troubleshooting
Table 20 Fault Displays, Causes, and Possible Solutions
Function Descriptions
Alignment Enable
To enable the alignment function, it is necessary to program the master and the follower trigger multi-function digital
input functions into the H1-
parameters and set parameter P4-01, Alignment Select, to a non-zero value.
The alignment function will NOT operate under the following conditions:
• Drive is faulted
• Drive is not running
• Follower is ramping between forward and reverse Run commands
• Electronic Line Shaft is disabled via multi-function input (H1-
= 80)
• Electronic Line Shaft is disabled via parameter setting (P1-01 is set to 1, 2, or 3)
• Drive is in LOCAL mode
• A “Jog” is being commanded of the follower drive
• Drive is ramping to speed due to a gear ratio change or Line Shaft being re-enabled
• Position error is being cleared via multi-function input (H1-
= 87).
Alignment Select
Parameter P4-01, Alignment Select, enables and disables the alignment feature. When P4-01 is set to 0, the drive will not
perform an alignment and the two digital outputs associated with alignment (H2-0
= 41 and H2-0
= 42) are de-
energized.
• When P4-01 is set to 0 - Disabled. The drive will not perform an alignment.
• When P4-01 is set to 1 - Manual Align. The drive must see the rising edge of the align command (H1-
= 8B) to start
the alignment process. The drive will not attempt another alignment until there is another rising edge on the align
command.
• When P4-01 is set to 2 - Auto Align at Start. The drive will immediately begin the alignment process when the Run
command is applied. The drive will not attempt another alignment until there is another rising edge on the align
command.
42
In Alignment
Closed after both trigger inputs are received and the distance between them is shorter than the P4-04 value.
Open after:
• The first trigger has been received and the accumulated distance exceeds the sum of P4-03 and P4-04.
• The follower is stopped, faulted, or an electronic line shaft position error is cleared or disabled.
• An advance/retard command is given.
Digital Operator Display
Description
AF
Alignment Fault
Too much distance (follower motor revolutions) was counted between the two trigger inputs
during an alignment routine.
The distance measured between the two trigger pulses (during alignment) or the entire
alignment error (including offset and position error) has exceeded 21,474,836 encoder
counts. (Regardless of the P4-07 setting).
Cause
Possible Solution
The distance between the master and the follower
exceeded the allowable amount (P4-07).
Check the machine integrity.
Malfunctioning or miswired trigger switches.
Check the trigger switches for proper wiring and operation.
Setting
Description
V/f
OLV/PM
V/f w PG
AOLV/PM
OLV
CLV/PM
CLV
V/f
OLV/PM
V/f w PG
AOLV/PM
OLV
CLV/PM
CLV
OLV/PM
AOLV/PM
CLV/PM
OLV/PM
AOLV/PM
CLV/PM