Welding process, Troubleshooting, Material choice – Dukane Dual Servo Spin Welder 403570-01 User Manual
Page 79: Parameter effects
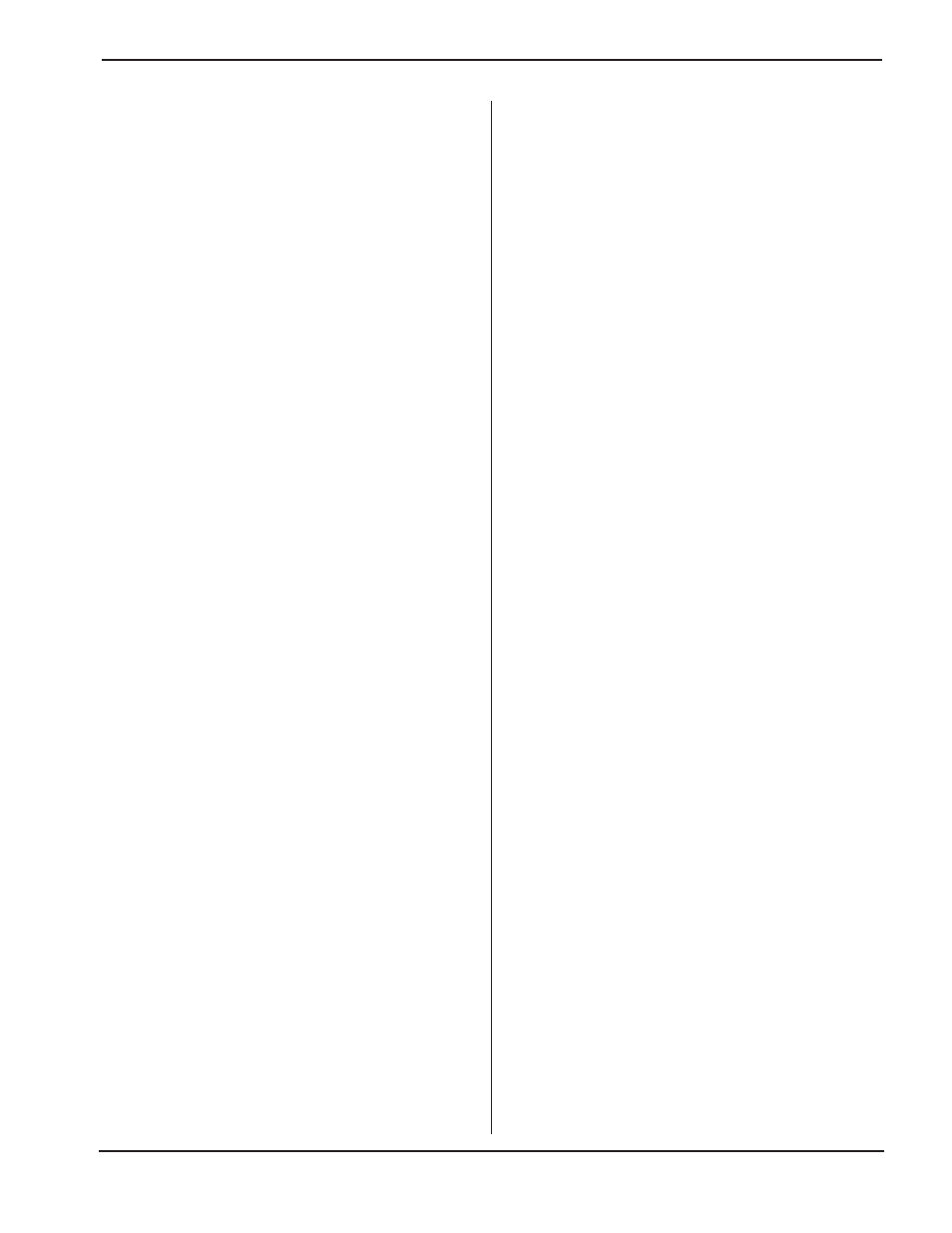
Dukane Manual Part No. 403-570-01
Page 73
Section 9 - Troubleshooting
Welding Process
Material Choice
A family of thermoplastics is usually compatible
with its own type and sometimes with other types.
Characteristics to consider are the melting point and
coefficient of linear expansion. Even members of the
same family may cause problems due to differences in
the manufacturing process. For example, an extruded
Polyethylene (PE) piece may not weld as well to an
injection molded PE piece as it would to another
extruded PE piece.
Parameter Effects
Surface Speed
Insufficient surface speed may not allow the plastic to
reach its melting temperature. Instead, it may simply
erode away part of the material and stick by a clawing
effect. The surface speed is determined by both the weld
joint diameter and the spin motor speed.
Axial Speed
In conjunction with surface velocity, axial speed
determines whether the plastic reaches the melting
temperature. Both surface and axial speed are needed
to produce sufficient frictional heating. Excessive axial
speed may cause one part to scrape away part of the
surface and produce a lot of flash but insufficient melt
volume.
Weld Depth
Insufficient welding depth may not allow the melt to
propagate far enough into the plastic to achieve the
necessary melt volume and the required weld strength.
Hold Time
Insufficient holding time may prevent the plastic from
solidifying and forming a strong permanent bond.
Troubleshooting
Table 9-I lists some potential problems with the weld
process and suggested solutions.