Control parameters, Surface speed – Dukane Dual Servo Spin Welder 403570-01 User Manual
Page 66
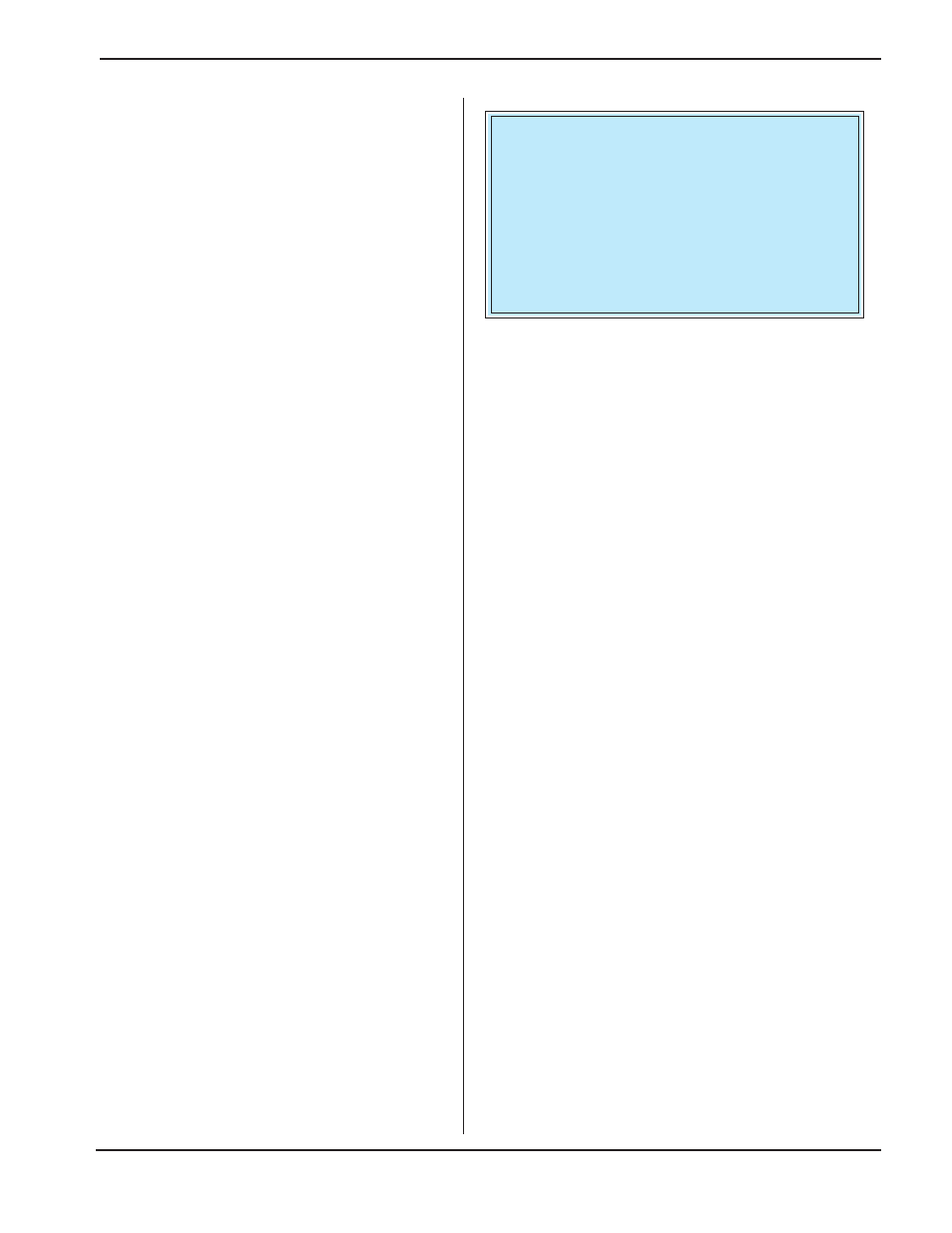
Dual Servo Spin Welder User’s Manual
Dukane Manual Part No. 403-570-01
Page 0
NOTE
Common hygroscopic thermoplatics:
ABS/Polycarbonate (Cycoloy)
Polyoxymethylene (Acetal, Delrin)
Polyamides (Nylon, Zytel)
Polycarbonate (Lexan)
Polycarbonate/Polyester (Xenoy)
Polysulfone (Udel)
Material filler and surface contaminants (e.g.
mold release agent) are two factors that will affect
consistency and weld repeatability. Spin welding
is more tolerant of contaminants than ultrasonic
welding. Spin welding is also less affected by
hygroscopic polymers, although they may still
require special handling for critical applications.
The moisture content can lead to bubble formation
in the joint resulting in decreased weld strength.
Control Parameters
There are several primary process control parameters
that affect weld quality. They are the surface velocity
of the weld joint, press (axial) speed, weld depth,
and hold distance and time.
The following sections are presented for informational
purposes only and are in no way meant to serve as
a rule or formula. The information is collected from
publicly available books and papers. It is presented
here to provide you with a general guideline for
setting the initial parameters.
Surface Speed
For a fixed rotational spin speed (RPM), linear
surface speed increases with weld joint diameter. For
a fixed weld joint diameter, surface speed increases
with motor RPM. Smaller diameter parts therefore
usually require more RPM than larger parts of the
same material. If the surface speed is too low, an
adequate amount of heat will not be generated to
cause sufficient melting. If the speed is too high,
excessive heat in the joint could result in material
degradation or reduction in viscosity leading to
material flow away from the joint.
The selection of the proper surface speed depends to
a large degree on the material and joint geometry of
the parts being welded. Some materials, such as PVC,
can be readily welded for a wide range of values,
while others require a narrow range. Commonly
quoted values in the literature recommend using