Press (axial) speed, Weld depth – Dukane Dual Servo Spin Welder 403570-01 User Manual
Page 68
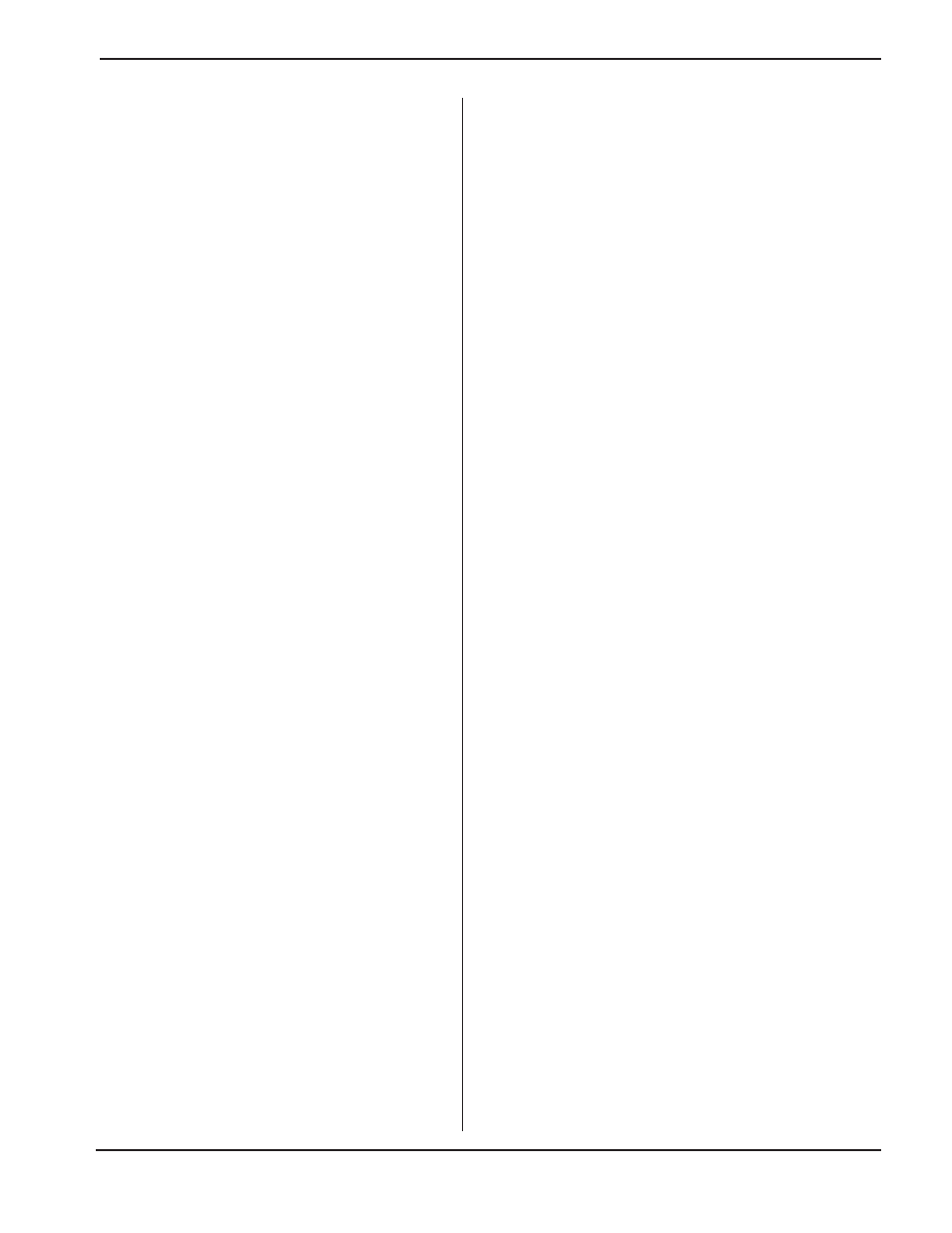
Dual Servo Spin Welder User’s Manual
Dukane Manual Part No. 403-570-01
Page
Press (Axial) Speed
The press speed affects the amount of contact
pressure between the parts being welded, which is
required to generate frictional heat. The larger the
speed, the larger the rate of heat rise. In combination
with the surface speed, press speed must be high
enough to cause melting at the interface as opposed
to grinding, but not too high as to damage the parts.
Excessive press speed can also lead to stalling of the
spin motor as more torque is required to maintain
constant spin speed.
The Dual Servo Spin Welder is capable of operating
in two different press speed modes. With the
Constant Torque Option (in SETUP > WELD tab)
disabled, the press speed is constant during the
weld. With the Constant Torque Option enabled, the
press speed is variable so as to keep the spin torque
constant (see Chapter 5). The latter case resembles
the operation of a pneumatically driven press, where
the press speed is the result of the melt rate under
given air pressure and spin speed conditions.
Selection of the optimum press speed depends on the
material and joint geometry of the parts, as well as
the surface speed. A range for initial experimentation
is 0.5 to 2.0 mm/s.
Weld Depth
The determination of the proper weld depth is
highly dependent on the application. The weld joint
is typically designed for a specific weld penetration.
Ideally, the weld is sufficiently deep to produce a
strong, hermetically sealed assembly. An excessive
depth may lead to the formation of flash (material
that is ejected from the joint area during the weld
and adheres to the assembly), the drawing out of
reinforcing filler material and realignment of the
interchain bonds in the weld plane resulting in a
weak axial weld joint, and possibly part distortion.