6operating and monitoring sd sensor system, 1 preventive maintenance plan (pmp) – K-Patents PR-23-SD Generation 1 User Manual
Page 31
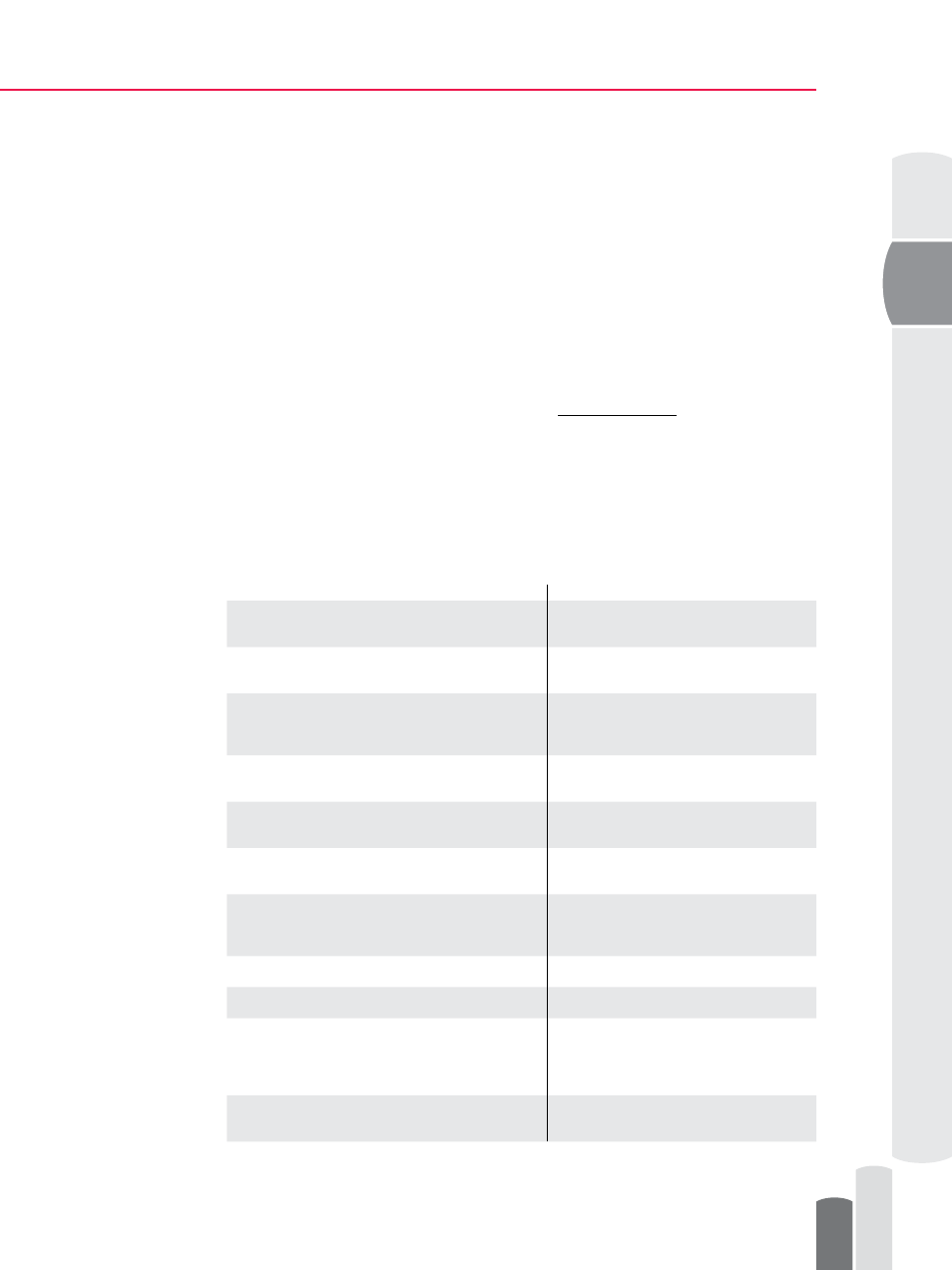
Safe-Drive™ Process Refractometer PR-23-SD Best Practices, Generation 1
© Copyright K-Patents 2013. All rights reserved.
31
If there is a need for frequent calibration, make sure that wash is functional and remove the
sensor to check visually that the prism is clean and has not been damaged. Re-install the
sensor and run complete field calibration (see chapter Entering field calibration parameters
in K-Patents PR-23 Instruction Manual). After this, contact your local supplier.
6
Operating and Monitoring SD Sensor System
The SD sensor system runs automatically and does not need to be separately operated. If
there are no alarming changes in the diagnostic values or no alarm messages, you do not
need to adjust the operation. The main task of the operator is to make sure that the washes
and steam connections are functioning as they should.
To rehearse the use of DTR transmitter, please visit demo.kpatents.net.
K-Patents recommends that all new users participate in K-Patents training before using
the product.
6.1 Preventive Maintenance Plan (PMP)
Preventive Maintenance Plan (PMP) should be adopted in order to prevent bigger
maintenance procedures. Here are the recommended tasks:
Task
Weekly
Annual
Notes
Check the functionality of
diagnostics:
X
See the attached PMI checklist.
CONC (measurement value
of output)
This value should be closely monitored
daily for a week to set the default reading
for weekly inspections
CALC (chemical curve of
calibration)
This is the default reading from the
chemical curve concentration reading set in
calibration, to which you can compare the
CONC values to.
TEMP (temperature)
Process temperature.
QF (quality factor)
Typically 30-100. If QF drops 20 units
below the normal level, perform a prism
wash test (see Commissioning checklist).
LED (exposure time)
Typically <30. If the LED value increases
significantly, perform a prism wash test
(see Commissioning checklist).
HD HUM (internal humidity%
of sensor)
If HUM HD rises above 50%, the system
issues an alarm to replace the desiccant.
For more information, see K-Patents PR-23
Instruction Manual.
Check the functionality of
wash system.
X
See Prism wash test in Commissioning
checklist.
Check the steam pressure.
X
Typically 5-6 bar (75-90 psi) over process
pressure.
Remove the sensor and
check the prism visually for
dirt and wear.
X
If the prism looks worn, run an nD
verification and replace the prism,
if needed. For more information on
nD verification, see K-Patents PR-23
Instruction Manual
Inspect the check valve: clean
the small holes and see that
the valve sealing is intact.
X
Replace the check valve every 2 years. For
more information, see chapter 6.3 Check
Valve Maintenance.