Start-up, Service – Carrier 09DK054-094 User Manual
Page 32
Attention! The text in this document has been recognized automatically. To view the original document, you can use the "Original mode".
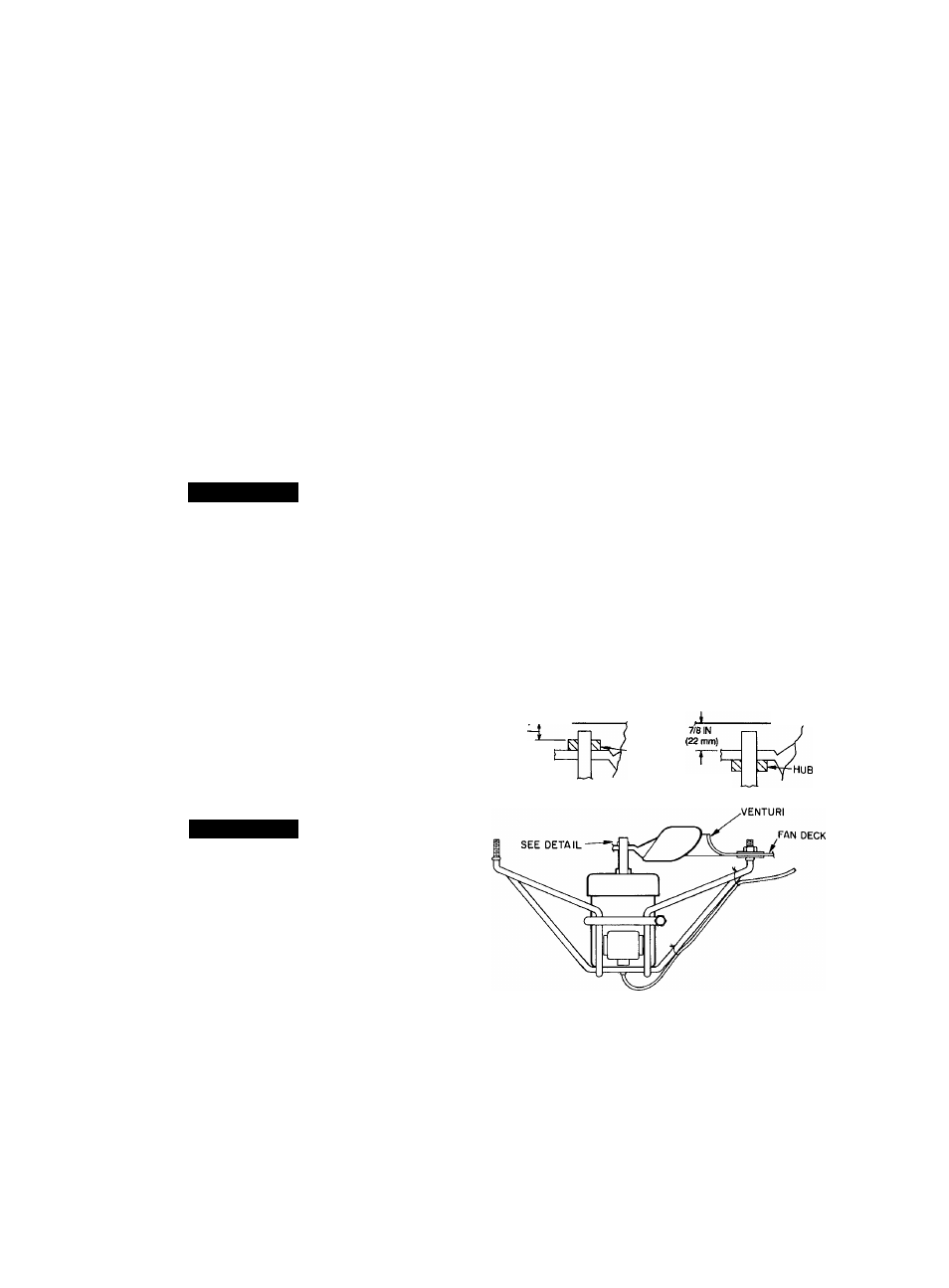
START-UP
System Evacuation and Dehydration
- Refer
to GTAC II, Module 4, “Dehydration for Proper Evacua
tion and Dehydration techniques.”
Charging Procedure
— BEFORE CHARGING THE
SYSTEM, INSTALL OR REPLACE THE FILTER-
DRIER(S) CONNECTED TO THE LIQUID LINE WITHIN
THE INDOOR UNIT(S) TO PREVENT CONTAMINA
TION WITHIN THE SYSTEM. Charge to a clear sight glass.
Refer to GTAC II, Module 5 “Charging, Recovery, Recy
cling, and Reclamation” for proper charging techniques.
Add 10 lbs (4.5 kg) of R-22 over clear sight glass to flood
subcooler sections of the condenser coils. This 10 lbs
(4.5 kg) is added to the total unit charge, and must be
proportioned by the percentage of circuits when multiple
circuits are employed. For example, in Table 2, add .67 x
10 lbs (4.5 kg) (approximately 6.7 lbs [3.0 kg]) for the 67%
circuit. Refer to Table 6 for condenser coil refrigerant cir
cuit data.
Check Operation of Condenser Fan Motor Con
trols and Rotation of Fans —
Rotation should be
clockwise as viewed from top of unit.
A
CAUTION
To prevent personal injury, be sure wire fan guards are
secured in place over each fan before starting the unit.
IMPORTANT. Check for proper fan rotation (clock
wise viewed from above). If rotation needs to be re
versed on one motor, disconnect main power supply
and switch motor leads at the fan contactor. If rota
tion needs to be reversed on all motors, disconnect
main power supply and switch two leads at TB1.
Head Pressure Control
— Reduces condensing ca
pacity under low ambient temperature conditions. See Fan
Cycling section below.
FAN CYCLING — The capacity of an air-cooled con
denser increases with increased temperature difference (de
fined as entering saturated condenser temperature minus
entering outdoor-air temperature) and decreases with de
creased temperature difference. A drop in entering outdoor-
air temperature results in a lower saturated condensing tem
perature. When outdoor-air temperature drops below the
minimum temperatures listed in Table 7 for standard units,
additional head pressure control is required.
Model 09DK units have fully automatic intermediate-
season head pressure control through condenser fan cycling
using electromechanical fan cycling controls. Standard head
pressure controls regulate the 100 and 50/50% condenser
capacity applications. Head pressure can also be controlled
by fan cycling controls supplemented by the accessory Motor-
master® III solid-state head pressure control. See Motor-
master III installation instructions for more information. Other
circuit split applications (67/33, 33/33/33, 33/33/17/17% ca
pacity splits) require the accessory fan control kit which in
cludes a control panel and additional fan cycling pressure
switches. See fan control installation instructions for more
information.
In the standard control scheme, fans 1 and 2 are on when
there is a call for cooling from the respective coil circuits.
Fans 1 and 2 are non-cycling. On 054 and 064 units, fans 3
and 4 are controlled by using a fan cycling pressure switch
on each of the primary coil circuits in response to condens
ing pressure. On 074-094 units, fans 3 and 4 are controlled
using a fan cycling pressure switch in each of the primary
coil circuits in response to condensing pressure. Fans 5 and
6 are controlled by using two air temperature switches, which
respond to the outdoor ambient temperature. The air tem
perature switches are located on the control box shelf. For
temperature and pressure setting details, see Table 8.
SERVICE
Cleaning Condenser Colls
— Clean coils with a vac
uum cleaner, fresh water, compressed air, or a bristle brush
(not wire). Units installed in corrosive environments should
be cleaned as part of a planned maintenance schedule. In
this type of application, all accumulations of dirt should be
cleaned off the coil.
A
CAUTION
Do not use high-pressure water or air. Damage to fins
may result.
Condenser Fans
— Each fan is supported by a formed
wire mount bolted to the fan deck and covered with a wire
guard. The exposed end of the fan motor shaft is protected
by grease. If the fan motor must be removed for service or re
placement, be sure to grease fan shaft and reinstall fan guard.
For proper performance, fan should be 7/8 in. (22 mm)
below the top of the venturi on the fan deck for 60 Hz units,
or 1/2 in. (13 mm) to top of the fan hub for 50 Hz units.
Tighten set screws to 15 ± 1 ft-lbs (20 ± 1.3 N-m). Fig
ure 31 shows the proper position of the mounted fan.
After servicing condenser fan motors, recheck their ro
tation. See the preceding Start-Up section.
Lubrication
— Fan motors have permanently lubricated
bearings.
TOP OF VENTURI
ON FAN DECK
(13 mm)
TOP OF VENTURI
ON FAN DECK
L
HUB
ALL 50-Hz
UNITS
ALL 60-Hz
UNITS
NOTE: Fan rotation is clockwise as viewed from top of unit
Fig. 31 — Condenser Fan Adjustment
32