Carrier 48MA User Manual
Page 11
Attention! The text in this document has been recognized automatically. To view the original document, you can use the "Original mode".
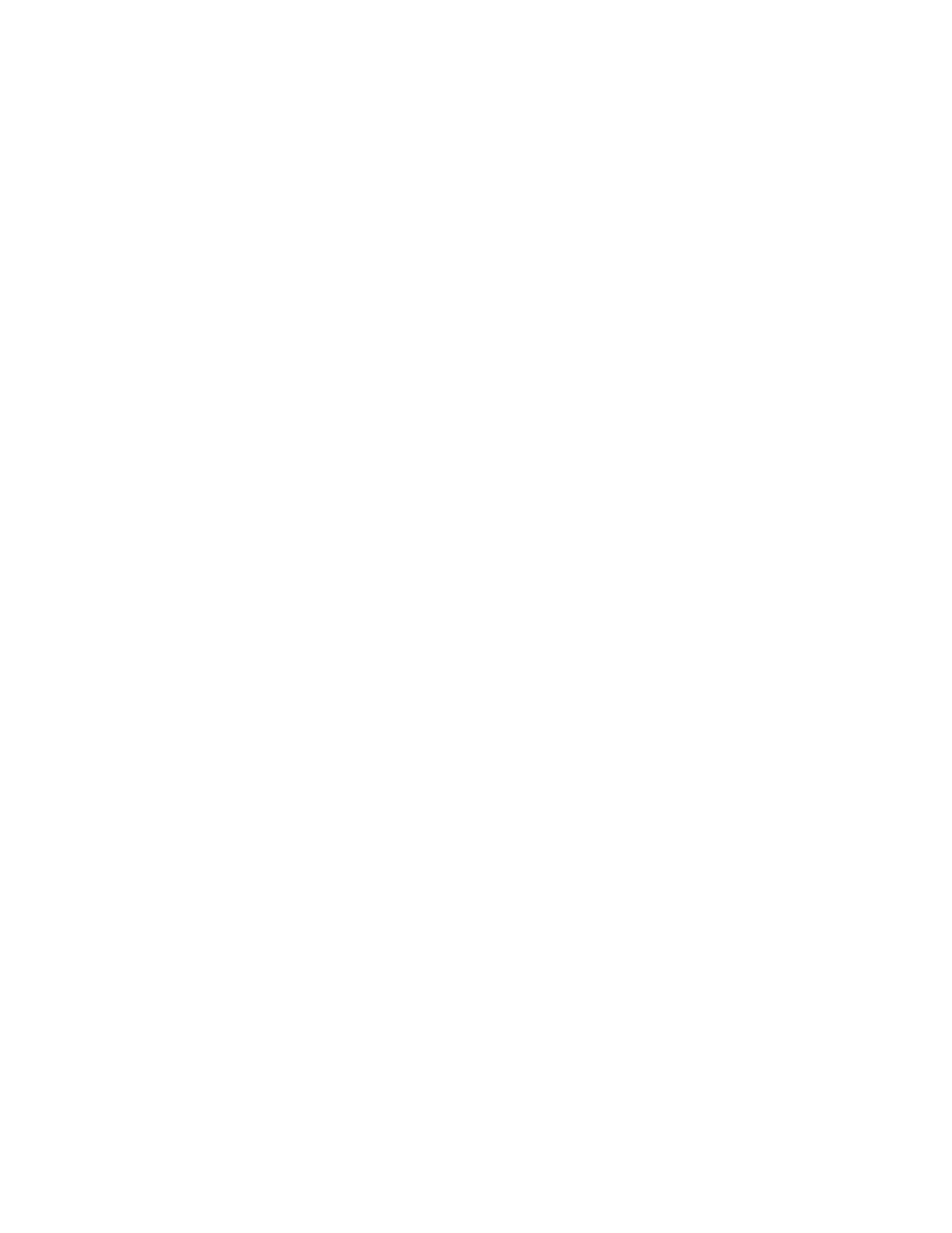
outboard zones in the 8-, 10- and 12-module units
are limited to a maximum of 1000 cfm. The
maximum limit is necessary to prevent blow-off to
the heat exchangers and into the ductwork. The
minimum limit prevents burner cycling on limit
switches and prevents electric heater cycling. At
reduced cfm’s, zone evaporator coils overfeed
refrigerant, but there is no liquid flood-back to the
compressor as it is protected by a suction line
accumulator.
For applications below 600 cfm, it is recom
mended that the heating controls be modified as
follows:
Gas fired (300 to 599 cfm) — Use first-stage
heat only, deactivate second stage.
Electric Resistance (450 to 599 cfm) — Use
first- and second-stage heat on 3-stage units.
Electric Resistance (300 to 449 cfm) — Use
first-stage heat on 2- or 3-stage heat units.
Optimum performance is delivered in the 800 to
1000 cfm range. Extremely low cfm requirements
reduce unit cooling capacity. Low zone cfm
applications may also be handled by sizing the
zone for a higher cfm (to increase unit efficiency)
and diverting the extra air into the return air
system or a larger interior space. Extra air should
not be diverted into spaces with different
perimeter wall orientations.
Fan performance data. Table 4 and Fig. 32, 33
and 34, (Fan Curves) are located in the Fan
Performance Section and are based on 15% out
door air. When the outdoor air dampers are closed
and there is no outdoor ventilation air into the
unit, unit cfm is reduced by 2 to 6%. This
reduction is due to the static pressure drops
existing in the separate airflows thru the unit. This
reduction should be considered in special applica
tions where little or no ventilation is required and
cfm requirements are critically designed.
MAXIMUM
VENTILATION
LIMITS
Under
normal mechanical cooling, the amount of ventila
tion air that can be introduced is a function of the
outdoor air damper setting and negative static
pressure at the return air intake of the unit. Figures
8 thru 11 show ventilation air versus negative static
pressure at various settings of the outdoor air
damper. A 5.5 setting of the ventilation control
dial is the maximum opening of the dampers. The
ventilation dial can be set in any position from 0 to
5.5 to obtain the desired cfm of outdoor air. The
ventilation dial is located on the control panel
adjacent to the heating section.
Reheat Applications
— A space with a high latent
load and a very low sensible load may require
reheat capability for dehumidification. Typical
spaces of this type are conference rooms or visual
aids rooms where people congregate with the lights
out.
Reheat control is achieved on the 48MA/50ME
unit by wiring a humidistat (Fig. 12) in parallel
with the cooling thermostat on any zone requiring
reheat capability. This may be done on one module
or all modules. When using reheat control on
electric resistance heat units, extreme care must be
exercised with power wiring as heating and cooling
can operate simultaneously in each module.
When the zone’s humidity level reaches the
setpoint of the humidistat, mechanical refrigera
tion is activated for that zone module and the air is
dehumidified and then reheated on thermostat
demand before being discharged to the zoned
space.
The 48MA/50ME Economizer
— The 48MA/50ME
units can be equipped with an economizer control.
The control functions as follows: with ambient
temperatures above the economizer changeover
point, the outdoor air damper is set at the
ventilation position, cooling is accomplished by the
compressors when the room thermostat calls for
cooling. If the zone is not calling for cooling, the
mixed air is circulated thru the space. When the
ambient temperature drops below the economizer
changeover point, the compressors are locked out
and the damper motor is under control of a mixed
air thermostat to maintain a mixed air temperature
low enough to provide cooling when the room
thermostat demands it. (See Fig. 13.)
1 1