Start-up, Do gits, Oism to ebeili. tot ^ feafc – Carrier 48KH User Manual
Page 9
Attention! The text in this document has been recognized automatically. To view the original document, you can use the "Original mode".
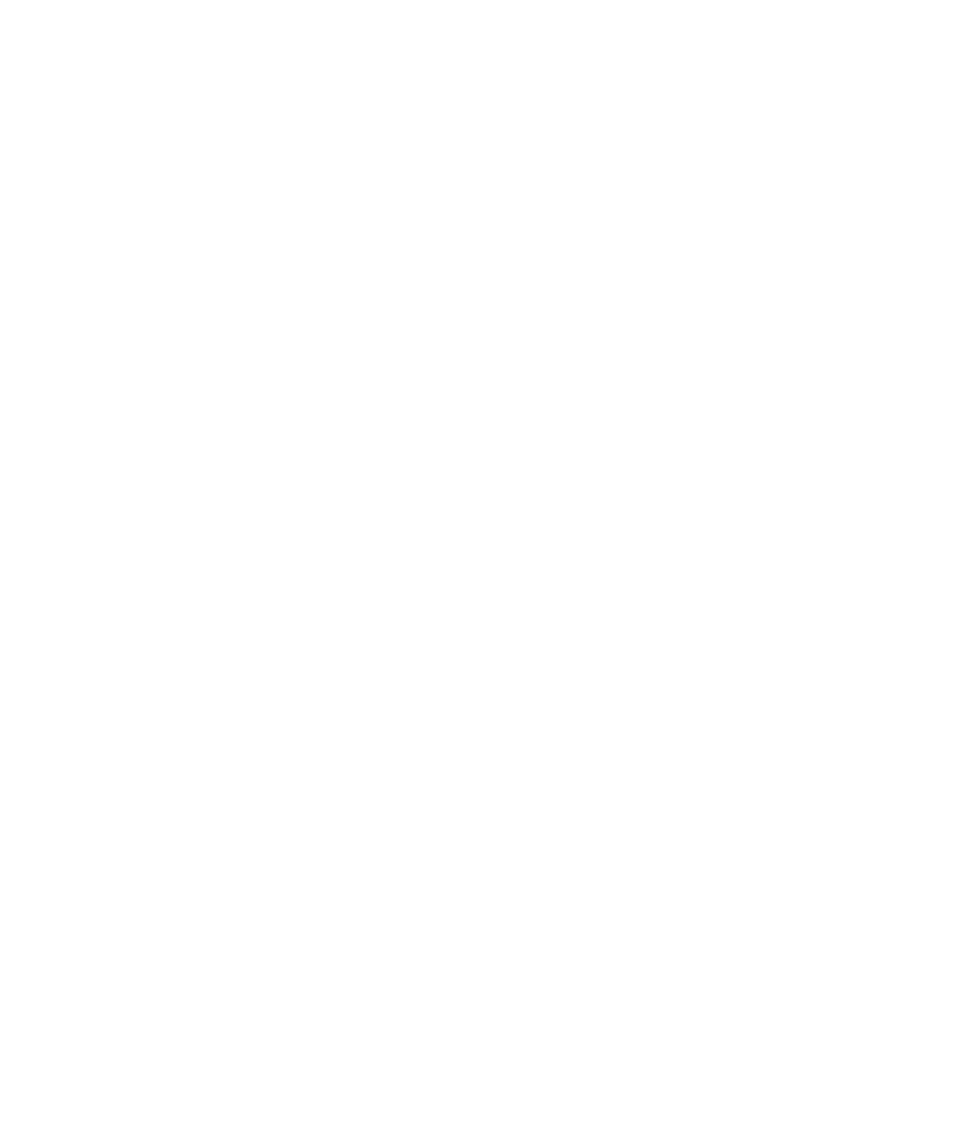
#
Using cover removed from red lead, insulate loose
terminal on orange lead. Wrap cover with electrical
tape so that metal terminal cannot be seen.
NOTE: For some 48KH,KL units, the factory-wired
blower-motor
speed
connections
may
require
ehanging for 208-v operation to ensure adequate air
flow at the rated external static pressure. See unit
wiring label. Insulate all unused motor leads follow
ing same procedures deseribed for transformer leads.
LOW-VOLTAGE CONNECTIONS Use a suit
able room thermostat as specified on unit wiring
label.
Locate room thermostat on an inside wall in space
to be conditioned where it will not be subjected to
either a cooling or heating source, or direct exposure
to sunlight. Mount thermostat 4 to 5 ft above floor.
Use no. 18 AWG color-coded, insulated (35 C
minimum) wires to make low-voltage connections
between thermostat and unit. If thermostat is located
more than 100 ft from unit (as measured along the
low-voltage wires), use no. 16 AWG eolor-coded,
insulated (35 C minimum) wires.
A grommeted, low-voltage inlet hole is loeated in
the panel adjaeent to control access panel. See Eig. 4.
Run low-voltage leads from thermostat, thru inlet
hole and to low-voltage flagged pigtail leads that run
thru a hole in bottom of unit control box. See Fig. 6.
Connect thermostat leads to pigtail leads as shown
in Fig. 8.
HEAT
ANTICIPATOR
SETTING
—
Room
thermostat heat anticipator must be properly ad
justed to ensure proper heating performance. Set
heat anticipator, using ammeter to determine exaet
required setting.
NOTE: For thermostat selection purposes, use 0.85
amps for approximate required setting.
Failure to make a proper heat anticipator adjust
ment will result in improper operation, discomfort
to occupants of conditioned space and inefficient
energy use; however, required setting may be
changed slightly to provide a greater degree of com
fort for a particular installation.
START-UP
Unit Preparation
WA
î
^N
î
NG: Fa:iio£e to obsem the foilowiag
wamngs coaid resali to
1. Follow recognized safety practices and wear pro
tective goggles when checking or servicing refrig
erant system.
2. Do not operate compressor or provide any elec
tric power to unit unless compressor terminal
cover is in place and secured.
3. Do not remove compressor terminal cover until
all electrical sources have been disconnected.
4. Relieve all pressure from system before touching
or disturbing anything inside terminal box if a
refrigerant leak is suspected around compressor
terminals.
5. Never attempt to repair a soldered connection
while refrigerant system is under pressure.
6. Do not use a torch to remove any component.
System contains oil and refrigerant under pres
sure. To remove a component, wear protective
goggles and proceed as follows:
a. Shut off gas supply
first, and then electrical
power to unit.
b. Relieve all pressure from system.
c. Use tubing cutter to cut tubing that connects
component, and remove component from
unit.
d.
Carefully unsweat remaining tubing stubs
when necessary. Oil can ignite when exposed
to torch flame.
PRE-START-UP PROCEDURES — Proceed as
follows to inspect and prepare unit for initial
start-up:
1. Remove all access panels.
2. Read and follow instructions on all WARNING,
CAUTION
and
INFORMATION
labels
at
tached to or shipped with the unit, such as blower
rotation labels, etc.
3. Remove these shipping components on the fol
lowing sizes of Models 48KH,KL.
a. 030 and 036 sizes — remove styrofoam block
wedged between header and unit side panel.
b. 048 size — remove shipping clamps that hold
compressor to unit base.
c. 060 size — remove styrofoam block wedged
between compressor and unit divider panel.
4. Make following inspections:
a.
Inspect for shipping and handling damages
such as broken lines, loose parts, disconnected
wires, etc.
b. Inspect for oil at all refrigerant tubing connec
tions and on unit base. The presence of oil
generally indicates a refrigerant leak. Leak-
test all refrigerant tubing connections using
electronic leak detector, halide torch or liquid-
soap solution. If refrigerant leak is detected,
see Refrigerant Leaks in next part of this
section.
c. Inspect all field- and factory-wiring connec
tions. Be sure connections are completed and
tight.
d. Inspect coil fins. If damaged during shipping
and handling, carefully straighten fins with a
fin comb.
Do
gits
it ¡Balaam
oism to ebeili.
tot
^ feafc«.