Control pressurestat for booster application – Carrier 5H User Manual
Page 28
Attention! The text in this document has been recognized automatically. To view the original document, you can use the "Original mode".
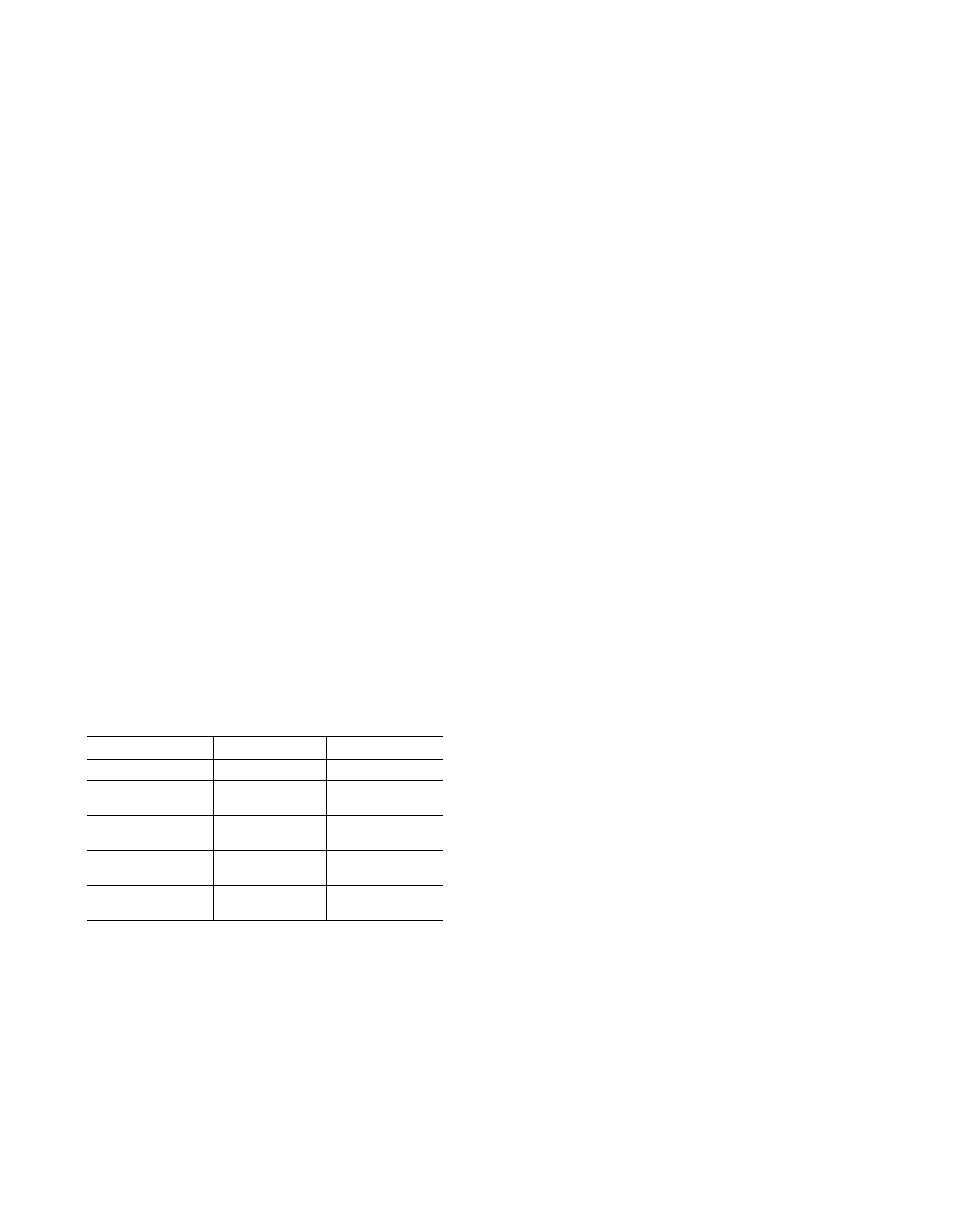
Three
common
methods
of
gas
desuperheating
and
liquid
cooling
for
direct
stage
systems
are
illustrated in Fig. 15. In the open type systems,
the refrigerant liquid is cooled down to the satura
tion
temperature
corresponding
to
the
interme
diate pressure. In the closed type systems, good
intercooler
design
usually
results
in
the
refrig
erant liquid being cooled down to 10 to 20 degrees
above
the
saturation
temperature
corresponding
to
the intermediate pressure.
Oil Separators and Lubrication
- In Freon cas
cade type systems, where evaporators and suction
lines are properly designed for oil return to the
compressor, oil separators are not usually used.
In
direct
staged
systems,
however,
oil
may
tend to accumulate in one of the stages and thus
result in lack of lubrication in the other machine.
By the use of oil transfer lines, equalization of
the oil level between crankcases can be achieved
by
manual
operation
at
periodic
intervals.
Auto
matic control of proper oil return to both com
pressors is effected by the use of a high stage
discharge line oil separator, returning oil to the
high stage machine, and a high side float, connected
to the high stage machine crankcase, which contin
ually drains excess oil from this crankcase down
to the next lower stage compressor (Fig. 15).
For booster application, the factory oil charge
should
be
drained
and
replaced
with
a
suitable
viscosity oil for the low temperature application.
Control Pressurestat for Booster Application -
The standard dual pressure switch furnished with
the
5F,H
compressors
is
not
suitable
for
use
with booster application. It must be replaced with
one of the appropriate low temperature dual pres
sar estats from Table 21.
Table 21 - Control Pressurestats for Low
Stage Application
REFRIGERANT 12
REFRIGERANT 22
CARRIER PART NO
HK04HN-068
HK04HN-164
Switch Action - High
Open on press, rise
Open on press ri se
■ Low
Open on press fall
Open on press fall
Range - High
20" Vac. to 65 psig
30" Vac to 110 psig
- Low
30" Vac to 20 psig
30" Vac to 25 psig
Differential - High
8 to 30 psi adjust.
12 to 30 psi adjust
- Low
5 to 15 psi adjust.
9 to 30 psi adjust.
Max Pressure - High
200 psig
300 psig
- Low
120 psig
300 psig
Discharge Valve Springs
- When 5Hcompressors
are used for booster applications where the dis
charge
pressure
is
below
10
psig,
the
standard
discharge valve springs furnished with the machine
should be replaced with an equal number of lighter
weight springs. Part Number 5H41-1801.
No change in discharge valve springs is rec
ommended for the 5F compressors.
SECTION
PAGE
DATE
5F,H-1XA
28
10-66
Printed
Water-Cooled Heads
- The standard 5F,H com
pressors are not equipped with water-cooled heads
but
they
are
available
on
special
order.
Water
cooling of the heads is not generally necessary in
R-12
and
R-22
booster
applications.
For
these
applications with R-22 involving high compression
ratios,
5
or
above,
5F,H
booster
compressors
should be equipped with water-cooled heads.
Motor Selection Data
- In staged refrigeration
systems,
the
high
stage
compressor
starts
first
and runs until the low stage pressure has been
reduced to a predetermined level before the low
stage machine starts. With direct staged arrange
ments,
the
high
stage
machine
draws
gas
from
the evaporator thru the low stage machine bypass
during this initial period. The size of the selected
motor must be related to the maximum condition
at which the booster compressor can operate.
The
compressor
may
run
under
heavy
loads
during
periods
of
high
suction
pressure,
espe
cially on starting when the system is warm. To
handle these situations the motor must be sized
larger
than
the
actual
balanced
operation
brake
horsepower
indicates,
or
special
attention
must
be paid to the operation of the system when starting
initially.
If the system is to operate only at a fixed low
temperature,
it
is
generally
possible
to
avoid
oversizing of motors to any great extent, provid
ing careful operation is followed when the system
is first put in operation.
For
those
cases
where
definite
pulldown
pe
riods are involved, the motors must be sized to
handle
the
highest
brake
horsepower
occurring
during pulldown.
On
applications
requiring
reduction
in
tem
perature
from
ambient
conditions
to
some
ex
tremely
low
temperature,
the
compression
system
will
be
operated
at
high
suction
pressures
for
considerable
periods
of
time.
General
practice
here is to drive the high stage compressor with
a motor that will carry the compressor at the
highest
expected
evaporator
temperature.
This
is generally the "air conditioning" rating of the
unit.
For
intermediate
or
low
stage
compressors,
it is generally sufficient to size the motor to take
care of double the balance load indicated horse
power plus the friction horsepower.
It
is
also
necessary
to
consider
compressor
starting
torque
requirements
when
selecting
the
motor
for
a
booster
compressor.
The
starting
torque of a motor only large enough to provide the
required normal operating bhp for booster appli
cations, may not be large enough to start the com
pressor.
The
recommended
minimum
motor
sizes
shown in Table 22 have been selected to assure
adequate
starting
torque.
The
actual
motor
size
selected
is
usually
larger;
however,
depending
on the maximum bhp conditions under which the
compressor
will
run
during
pulldown
or
other
abnormal operating periods.
.
S U P E R S E D E S
SECTION
5F,H-1X
PAGES
1-42
inU.S.A.
DATE
11-63