Carrier 5H User Manual
Page 26
Attention! The text in this document has been recognized automatically. To view the original document, you can use the "Original mode".
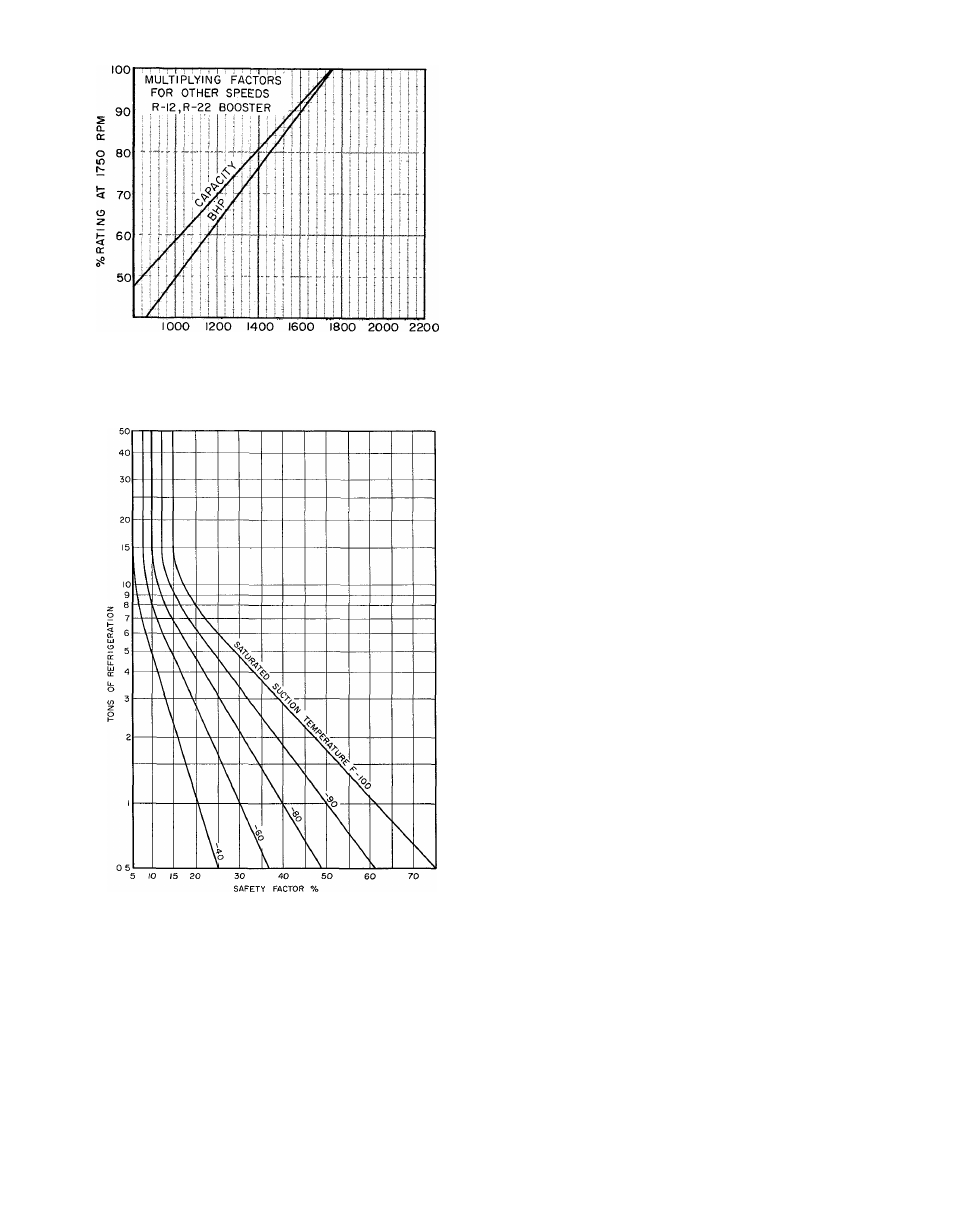
SPEED (RPM)
Fig. 16 - Multiplying Factors - Nonstandard
Speeds
Fig. 17 - Booster Compressor Selection
Safety Factors
Safety Factors
- The use of capacity safety fac
tors
in
selecting
booster
compressors
must
necessarily be a matter of judgment on the part
of the engineer making the selection.
Factors
which
have
a
bearing
on
satisfactory
compressor
selections
are:
the
accuracy
of
the
load estimate, the amount of safety factor included
in the total load, knowledge of the degree of impor-
SECTION
PAGE
DATE
5F,H-1XA
26
10-66
Printed
tance of meeting the specified capacity at the given
condition, the temperature level of operation and
the magnitude of the refrigeration load. All of the
factors must be recognized when considering the
use
of
a
capacity
safety
factor
in
selecting
a
booster compressor.
Figure
17
presents
reasonable
safety
factors
for use in the selection of booster compressors.
These can be employed when it is not desired to
e stablish a factor based on the selector's judgment.
When
a
capacity
safety
factor
is
used,
the
compressor
is
selected
at
its
maximum
speed
to handle the design load plus the amount of safety
factor.
Whether or not the added capacity offered by
the safety factor is incorporated at once is a mat
ter of judgment. If it is, then the compressor will
be operated at maximum speed right at the start
and any excess capacity achieved will be reflected
in faster pulldowns or lower temperatures. It is
also, however, good practice to drive the machine
at the speed which will provide slightly more rated
capacity than is required by the design load. The
additional
speed-up
available
will
then
constitute
reserve capacity in the event that it is needed.
Motors should be sized to run the compressor at
maximum
speed
to
forestall
any
motor
changes,
should
this
maximum
compressor
speed
be
re
quired in the future.
Determining Intermediate Pressure-
in the appli
cation of commercial compressors to staged sys
tems, it is found that the lowest total bhp per ton
and
most
economical
equipment
selection
results
when
using
approximately
equal
compression
ratios for each stage. However, it is also econom
ical to juggle assigned compression ratios slightly
to fit available sizes of machines.
The use of Fig. 18 will allow direct determina
tion
of
the
proper
intermediate
pressure
which
will result in equal compression ratios per stage
for
direct
two-stage
system.
The
information
in
Fig. 18 is given in terms of saturated temperature
instead of pressures, for easier use with the com
pressor ratings.
The existence of a second appreciable load, at
some
higher
suction
pressure
level,
will
very
often
dictate
the
most
convenient
intermediate
pressure.
Gas Desuperheating
- The operation of a direct
staged system requires cooling of the gas between
stages.
Otherwise,
the
highly
superheated
dis
charge gas from the low stage machine would be
taken directly into the suction of the higher stage
compressor
and
further
compression
would
result
in excessive heating of this compressor.
Liquid Cooling
- It is also necessary to employ
liquid
cooling
between
stages
and
increase
the
refrigeration effect of the liquid delivered to the
evaporator
to
realize
the
rated
capacity
of
the
booster
compressor.
The
amount
of
refrigeration
expended in cooling the liquid between stages is
accomplished much more economically at the level
of the high stage compressor suction than at the
level of the low stage suction.
S U P E R S E D E S
SECTION
5F,H-1X
PAGES
1-42
inU.S.A.
DATE
11-63