System operation – Sonics E-Press User Manual
Page 8
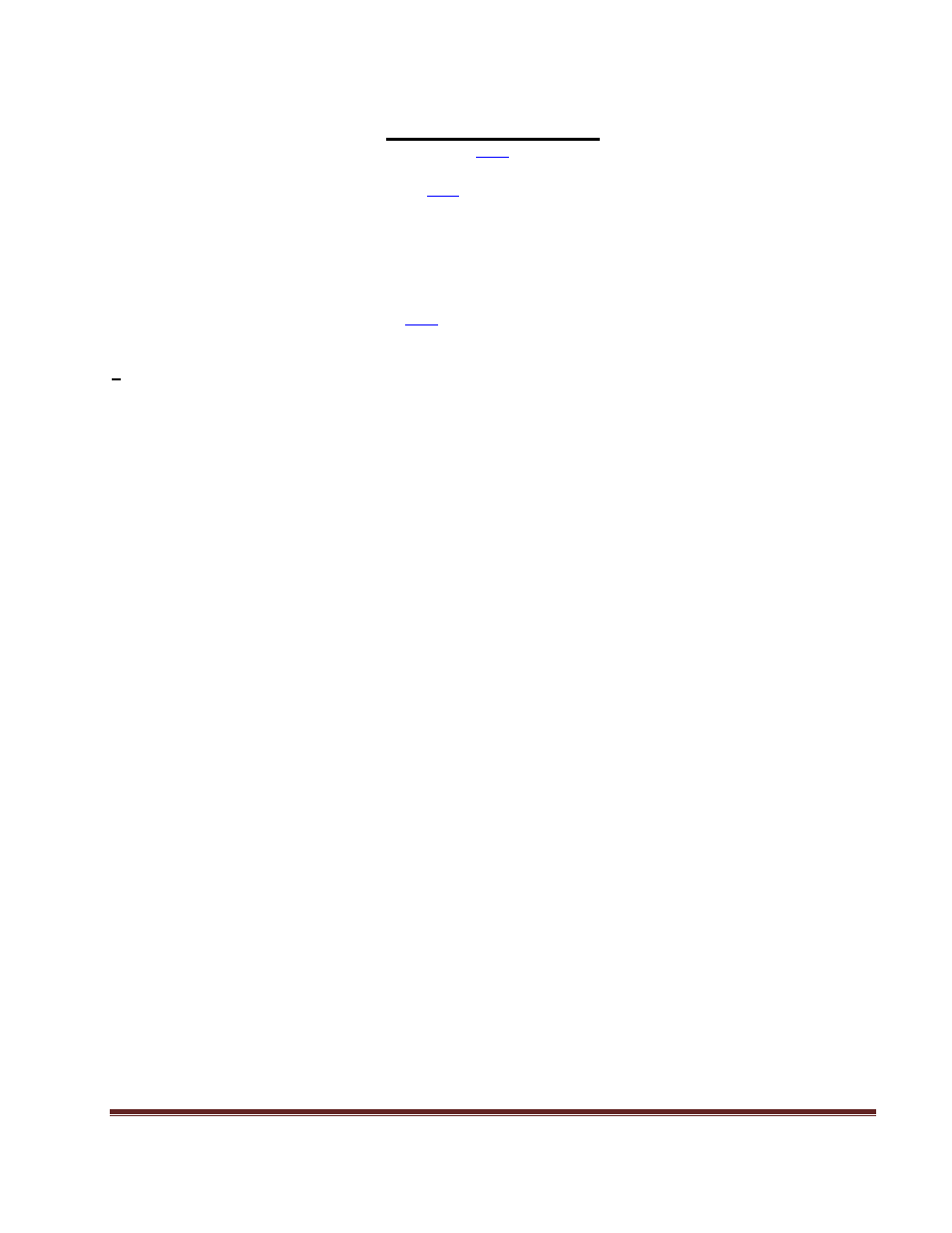
Sonics E-Press Manual
Page 8
System Operation
TOC
1.0 Introduction to Plastic Welding
TOC
-
For an introduction to ultrasonic plastic assembly – Refer
to the GX Power Supply Instruction Manual supplied with the ultrasonic power supply - pages 6 through 8.
These sections discuss the basic principles of ultrasonic assembly and the major ultrasonic components –
converter, booster and horn. The E-Press welding system is identical except that a solid mount booster is
used that will not flex under applied pressure. To achieve the best desired assembly accuracy of the stepper
system, a solid mount booster is required.
2.0
The Stepper Welding System
TOC
-
The Stepper Welder System (E-Press Model) is designed for
precision plastic welding applications with dimensional requirements beyond the capabilities offered with a
standard air actuated ultrasonic press. The system will control the final weld position with a tolerance of
+0.0003 inches. Finished assemblies are produced with a weld repeatability that is not possible with any other
plastic welding process. The advancing speed of the ultrasonic horn is controlled with a stepper motor drive,
which exactly repeats the defined profile for position and velocity every time. The results are repeatable welds
with exact final dimensions of the bonded components when compared with air driven actuators (material
dependent). The system is offered as a transport option with standard Sonics & Materials 20 kHz and 40 kHz
ultrasonic power supplies.
The E-Press actuator assembly is a completely rigid system. Solid booster technology is used to mount the
stack assembly into the actuator head. These boosters do not contain O-rings, which are found in
conventional ultrasonic boosters. O-rings can move and distort as pressure is applied resulting in horn
movement on the parts and weld quality problems. With this rigid system the horn will not move and full
capability of the stepper motion controls can be achieved.
Welding with an E-Press driven actuator is very unique, compared to a conventional pneumatic welder. With a
pneumatic welder the applied force on a part is adjusted by changing the air pressure regulation to the cylinder
which drives the horn assembly. Continuous pressure is applied to the parts during the welding process.
Attempts to modify the applied pressure are only marginally successful due to the volume of air that is present.
Pressure cannot be changed instantaneously as long as the air system has pressure. A notable lag will occur
between changing the regulator settings and any actual pressure change. In most cases, the weld will be
completed long before the pressure change could affect the weld in any appreciable way. With the stepper
system, force can be controlled precisely through a digital velocity profile.
The E-Press system uses the programmed weld velocity to control the applied force directly. This applied
force is also dependent on ultrasonic amplitude, which controls the level of heat available, and therefore the
amount of molten plastic that will be produced between the parts. The resultant force will be a function of
heat (ultrasonics) to melt the plastic and velocity to drive the parts together. The faster the horn moves into
the parts the greater the force. The greater the heat that’s available to melt the plastic, the lower the force,
because the plastic will flow out from under the horn. Best application results will be provided by careful
balance of velocity, distance and ultrasonic amplitude. With the velocity and distance precisely controlled, the
actual weld cycle time will also be exactly repeatable because the velocity profile will be the same every time.
The E-Press controls are packaged in the same size chassis as the Sonics & Materials ultrasonic power
supply so that they can be stacked together. This provides a standard ultrasonic supply whether the customer
application requires velocity controls with the stepper transport or a standard air actuated system. Both units
should be located so that they are accessible to the operator for initial setup and programming.