Sonics E-Press User Manual
Page 17
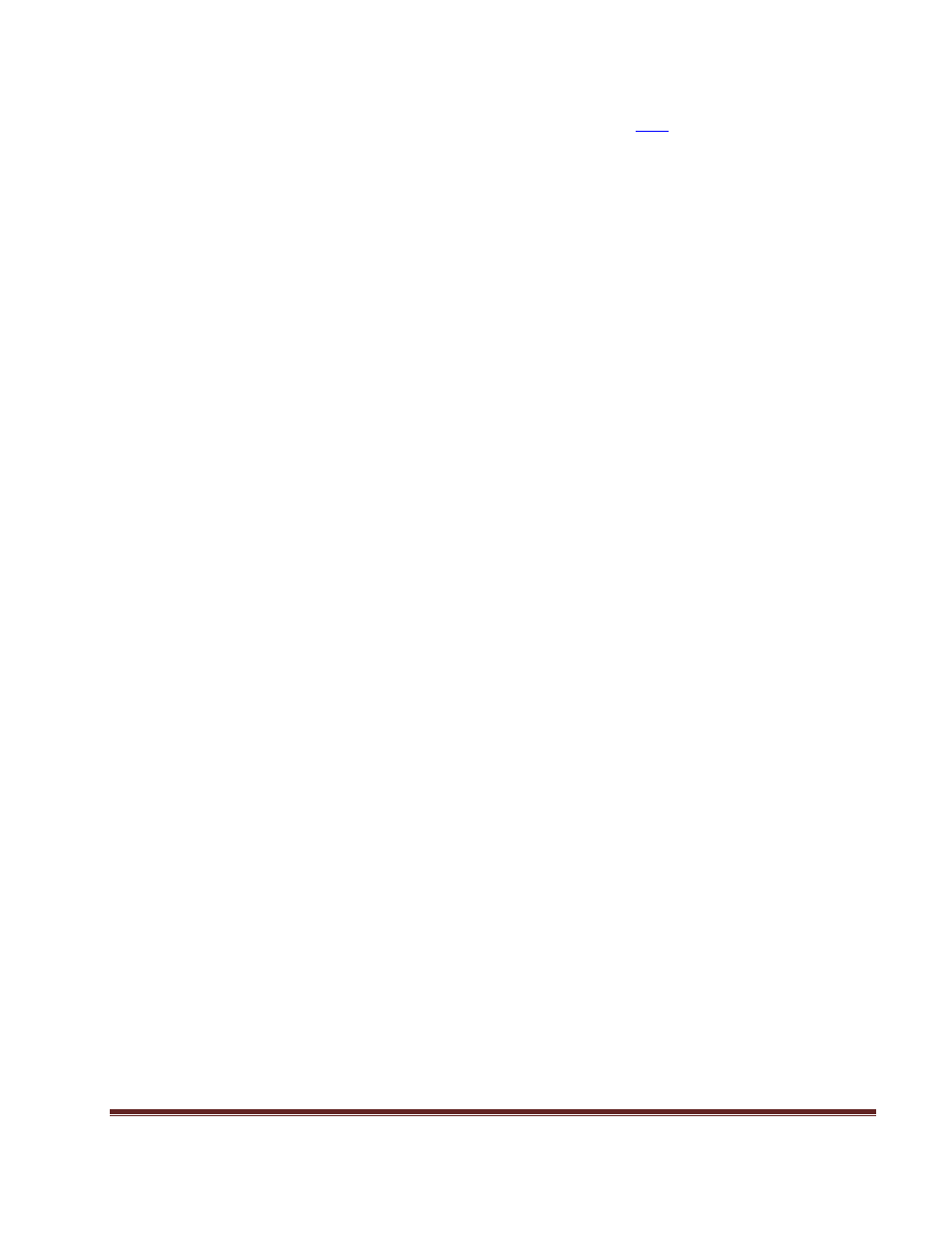
Sonics E-Press Manual
Page 17
7.0 Quick Start Setup Procedure for a Typical Application
TOC
– This section is intended to
be a quick startup checklist for an operator who is familiar with the E-Press welding system. Users who are
unfamiliar with the system should read this manual and the GX power supply manual, prior to welding any
parts. After reading those manuals, return to this section with a full understanding of the system interactions
between distance, speed and ultrasonic controls.
Setting up the system to weld a typical part is really very easy but can seem involved due to the movement
and ultrasonic controls required. In order to make full use of the precise distance and velocity welding
functions, the ultrasonic power supply will be set so that the time or energy settings are beyond the expected
weld requirements. The stepper movement should reach the programmed position before either time or
energy settings are reached. Steps to prepare a typical part for welding are identified below. The computer
interface must be connected and running properly to set up a part for welding. Once the machine is set up,
the computer can be disconnected without effecting the welding process provided that the termination jumper
supplied is installed on the back Stepper Controller chassis. Details of the settings are further described
below, but the quick start directions can help the proficient user.
1. Install the horn and fixture on the machine.
2. Release the column locking clamps, raise the Ultrasonic head to provide clearance of at least 4
inches (101.6 mm) above the parts and fixture. Secure the clamps.
3. Set the unwelded parts into the fixture with proper orientation.
4. Set the desired travel and welding parameters using the stepper utility software program. (click SET
function to transfer values). See section 9.0 for the stepper controls description. Set the travel
distance value large enough to place and remove the parts. Enter the upper and lower tolerances
expected. These numbers should account for the variation in the molded parts. Set the upper
tolerance to 0.0100 in (0.300 mm); Set the lower tolerance to the thickness of the top part (0.100
inches max). This prevents the horn from contacting the fixture while looking for the parts. Enter the
force trigger level desired before sonics starts. This is the force applied to the parts before the weld
begins. Again use the SET function to send these values to the machine.
5. Extend the ultrasonic horn using the Align function on the stepper controls front panel. Press the
Align button and then the system palm buttons. The system will extend the horn to the programmed
Travel Distance. Maintain the button command until “Head is Down” is displayed on the LCD
screen.
6. Again release the locking clamps and lower the head assembly so that the horn contacts the top of
the unwelded parts. Now position and align the horn, parts and fixture. Lock the column clamps
and secure the fixture.
7. Return the Head to the Home position by pressing the HOME button.
8. Teach the system where the parts are located: Press the TEACH button. Per screen instructions,
press the palm buttons and keep depressed until the distance to the part is displayed on the LCD
screen. The system will move the horn to the unwelded parts and apply the programmed pressure.
This contact distance will be remembered for the welding function.
9. Press the HOME button to return the press head to the home position.
10. Set the Weld mode for Incremental, the Weld Velocity #1 to .02 in/sec and Weld Distance #1 to
0.0100 inches (let’s go slow for the first weld). Set Weld Distance #2 to 0. Again use the SET
function to send these values to the machine.
11. Set the ultrasonics on the GX power supply for a longer weld time than necessary to complete the
weld. Force Trigger must be disabled. The Delay Time must be set to 0.01 seconds (stepper
controller needs this delay); Hold time to 1 second (or desired); Afterburst to 0.00 and the Time Limit
High to 9.99 seconds. Set the amplitude to approximately 80% to assure sufficient melt. These
parameters are programmed from the GX power supply. See the GX manual for further assistance.
12. If using a GXE power supply with energy welding controls, set the Energy parameters for a higher
Energy number than will be delivered during the weld time. The distance should control the weld in
most cases when using the Stepper system. If the ultrasonics times out or reaches the energy limit
before the programmed distances are achieved, then the cycle will not be complete. The control
parameter (distance, energy or time) which wins the race to its programmed setting will end the
present weld cycle. If a distance is not achieved, check the time or energy settings to see that the