Sonics E-Press User Manual
Page 15
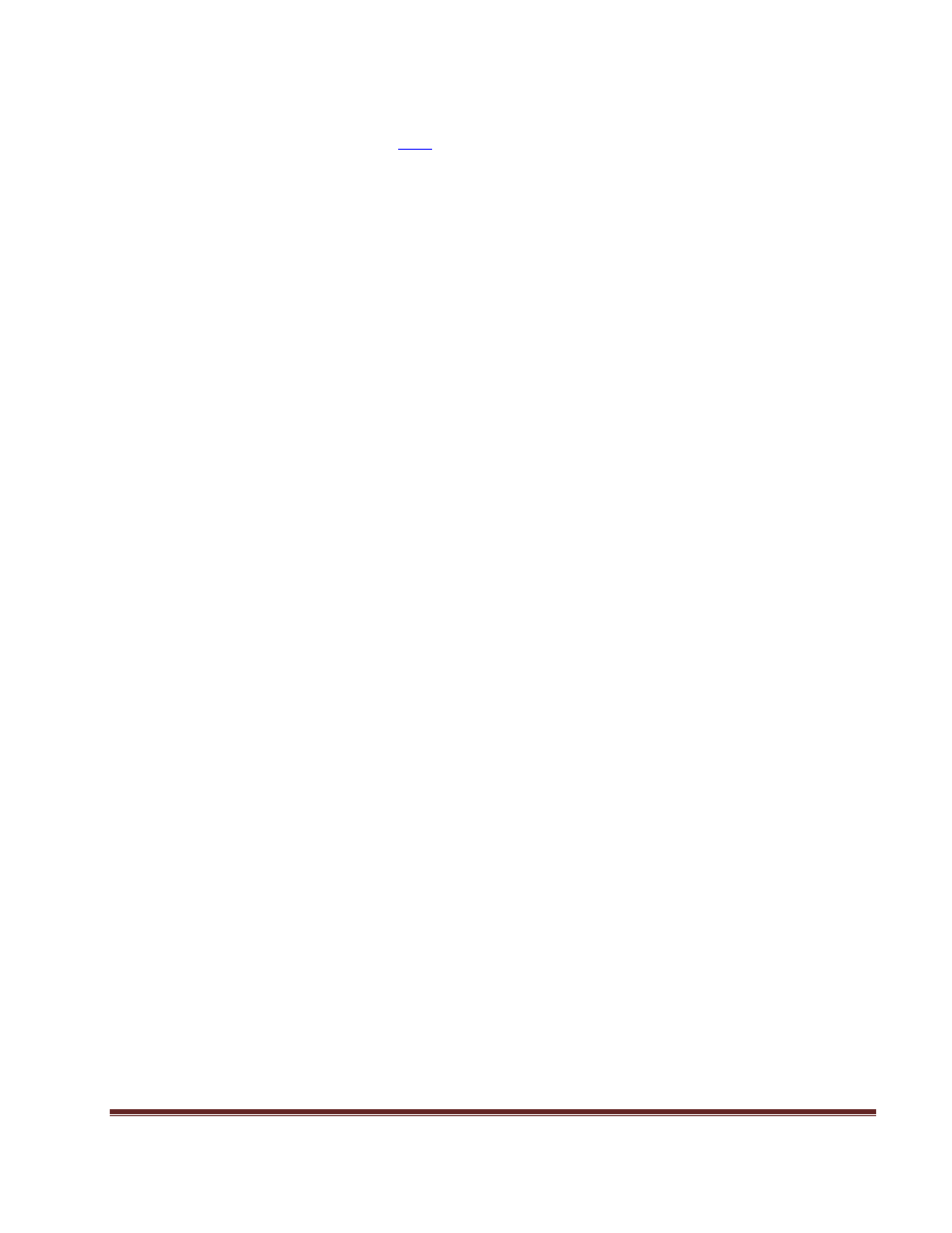
Sonics E-Press Manual
Page 15
6.0 Stepper Welding Operation
TOC
– The stepper welding process is similar to the conventional
ultrasonic process. The application parts are positioned in the fixture and dual palm buttons are pressed
simultaneously to initiate a weld. A cycle begins by advancing the horn to the parts at a fixed approach
velocity. The approach velocity has been selected based on the mass of the head mechanism and the
maximum acceleration that can be used without stalling the stepper motor.
Just above the parts, the velocity is reduced to a search speed in order to locate the parts for assembly. This
protects the parts from impact damage that could result from a higher speed contact. The parts search will
continue for a distance equal to the width of the programmed tolerance window or until the parts are found.
When the ultrasonic horn contacts the assembly, pressure will increase quickly. The applied force is
measured and monitored until the trigger set-point is reached defining the parts’ location and positively seating
the plastic interface joints. The trigger is satisfied and ultrasonics will be turned on to begin the plastic weld.
The defined weld motion profile will continue as the ultrasonic energy melts the plastic joints.
When the weld velocity and distance profiles have been executed, the weld is complete and ultrasonics will be
turned off. If a hold time has been programmed, the motion will be stopped and the system will wait for the
specified time period. Hold time is normally used to allow the plastic joint to solidify while the parts are held in
position to complete the bonding process.
The system will retract to the home position to end the weld cycle. The final weld distance will be reported on
the stepper controller display and the system will be ready for another weld operation.
The following sequence of events defines the “typical” weld cycle. See section 12.0 for the details of
programming the stepper settings.
Typical Weld cycle:
1. The weld cycle is initiated by simultaneous palm button commands.
2. The stepper drive head assembly will descend at a high speed to the parts position taught by the
“Teach Command”, less the upper tolerance setting.
3. The system searches for the parts at a slower search speed. The parts are detected when the force
builds to the programmed Force Trigger set-point. If the parts are not found by the time the system
has traveled to the lower tolerance setting, the cycle is aborted and the head retracts automatically.
Parts may not be positioned in the fixture.
4. When the parts are found, the specified incremental or absolute weld will begin. The ultrasonics is
turned on and the motor continues to travel at the programmed Velocity #1 until the programmed
Distance #1 is reached.
5. If a second weld distance has been entered (anything but a zero value) then the weld will continue
after the first distance using the parameters for the second distance settings. The travel motion
proceeds using welding Velocity #2 until Distance #2 is reached. Ultrasonics will be on or off during
this period controlled by the Weld indicator associated with the Travel #2 parameters. If “Off” has
been selected for ultrasonics during this period then the ultrasonic hold time must be set long enough
to allow for the movement plus any additional Hold time is required by the application after the move is
complete. See section 12.10.
6. When the distance has been satisfied, the ultrasonics will be turned off by a cutoff command issued to
the GX power supply.
7. The system waits for the hold time specified for the welder controls.