Sonics E-Press User Manual
Page 16
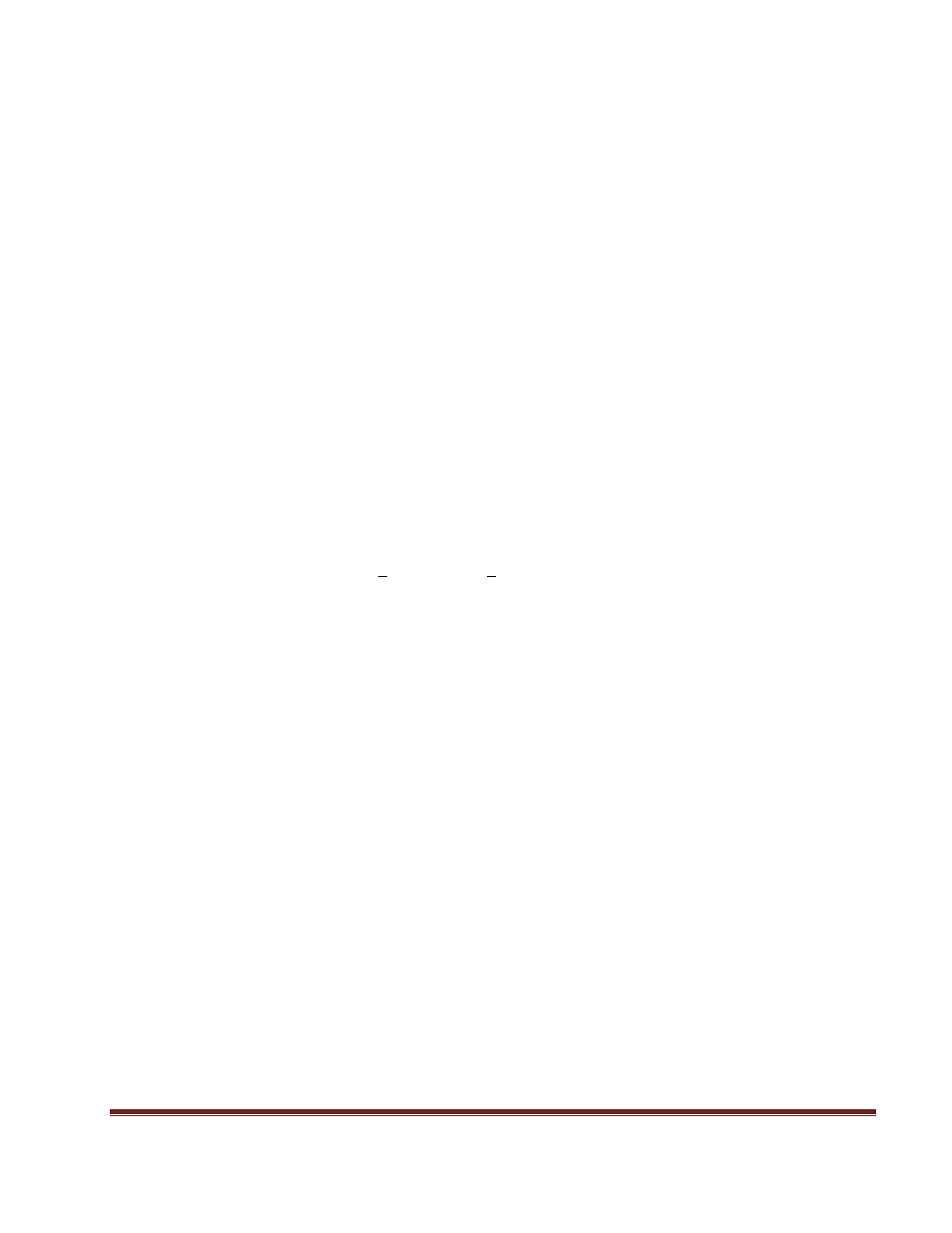
Sonics E-Press Manual
Page 16
8. When the weld cycle is complete, the system ascends to the home position (up).
9. The stepper controller transmits the final distance report and the GX ultrasonic controller transmits the
weld status information.
Power Up
– The stepper system has two separate power switches - a green membrane key on the GX power
supply
and an identical green key on the E-Press Motor Control box. Both units should be powered up before
the computer system is turned on. The order is not critical.
Safety Note
– The stepper welding system will retract to the head up position whenever the Red Emergency
Stop button on the front of the press is engaged. The Stepper Controller will remain powered during an
emergency stop condition in order to step the mechanism in the reverse direction. It does not power down
with engagement of the Emergency Stop button. This action is necessary due to the force that can be applied
by the screw mechanism! Just stopping all movement is not an acceptable action because the applied
pressure will not be removed. The pitch of the screw mechanism is very small, it may not be easy to release
the pressure by human intervention. It could be difficult for the operator to manually lift the press assembly.
Depending on the customer application, additional protection may be required by local laws or the European
community. In some applications where operators may be directly exposed to danger areas additional
guarding may be required. The ultrasonic power supply section is CE marked and has been tested in
standard air actuated ultrasonic systems. The motor controls are not CE marked.
Position Accuracy
–
The system uses a stepper motor drive and ball screw which is controlled to 42666
counts per inch and a feedback encoder which reads to 6660 counts per inch (1679 counts per millimeter and
262 counts per millimeter respectively). Allowing for lower encoder resolution and a small backlash within the
system, the position accuracy will be + 0.0003 inch (+ 0.007 mm). The indicated position numbers on the
stepper and logger screens represent the measured motor movement. Any mechanical deflection caused by
large pressures applied to the “Parts to be Welded” will degrade the accuracy numbers (with respect to the
parts dimensions). Typical deflection measurements for each type of press are provided in the Maintenance
section at the end of the manual. The operator should be aware that large pressures approaching 500 LBS
can be applied very quickly. If the ultrasonic amplitude is too low and the plastic is not hot enough to melt,
then large pressures can be applied with only a few steps of the motor system. If pressures exceeding 500
LBS are applied, the motor system may stall. The system must be reset with the RESET button on the back of
the controller panel.
Applications
– A stepper application project involves careful setting of the stepper and ultrasonic controls.
Distance and velocity controls are set using the stepper setup utility program in combination with the Stepper
Control panel switches and display. The ultrasonic controls are adjusted with the GX power supply control
panel.