4 propane combustion calibration, Initial start-up – AERCO BMK 2.0 LN Nat. Gas June 2010 User Manual
Page 40
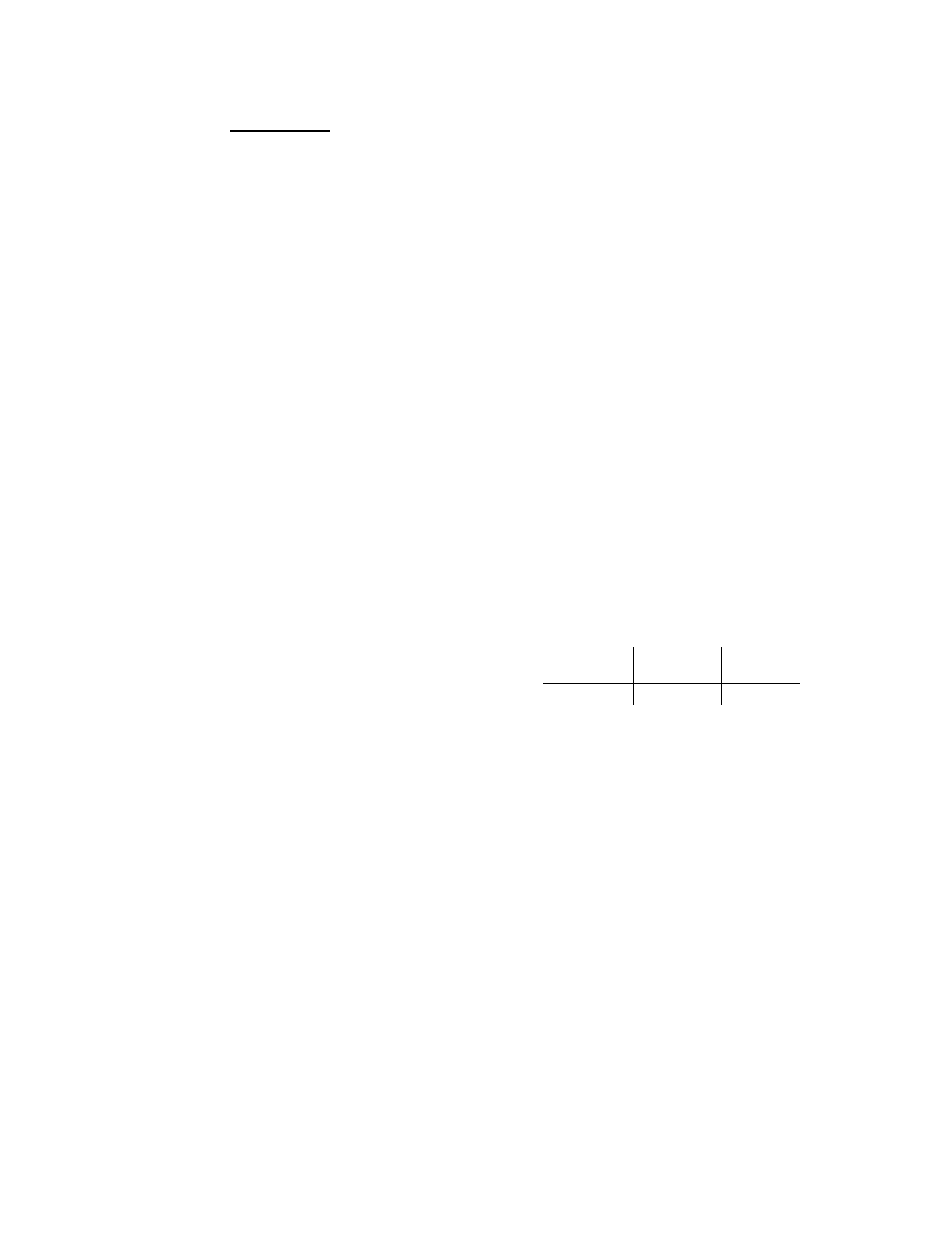
INITIAL START-UP
IMPORTANT
The unit is shipped from the factory set up
for either Natural Gas or Propane as
specified by the Style No. on the Sales
Order.
Since the required gas pressures and
oxygen (O
2
) levels for Propane differ from
those required for Natural Gas, the
Propane Combustion Calibration
procedures are repeated in paragraph
4.4.
4.4 PROPANE COMBUSTION
CALIBRATION
The Benchmark 2.0LN Boiler is combustion
calibrated at the factory prior to shipping.
However, recalibration as part of initial start-up
is necessary due to changes in the local altitude,
gas BTU content, gas supply piping and supply
regulators. Factory Test Data sheets are
shipped with each unit. These sheets must be
filled out and returned to AERCO for proper
Warranty Validation.
Prior to starting these procedures, ensure that
the Benchmark 2.0LN has been set up as
specified in paragraphs 4.2 through 4.2.3.
It is important to perform the following procedure
as outlined. This will keep readjustments to a
minimum and provide optimum performance.
1. Open the water supply and return valves to
the unit and ensure that the system pumps
are running.
2. Open the propane supply valve(s) to the
unit.
3. Set the control panel ON/OFF switch to the
OFF
position.
4. Turn on external AC power to the unit. The
display will show LOSS OF POWER and the
time and date.
5. Set the unit to the Manual Mode by pressing
the AUTO/MAN key. A flashing Manual
Valve Position
message will be displayed
with the present rate in %. Also, the
MANUAL
LED will light.
6. Adjust the valve position to 0% by pressing
the ▼ arrow key.
7. Ensure that the leak detection ball valve
(Figure 4-1) down-stream of the SSOV is
open.
8. Set
the
ON/OFF
switch to the ON position.
9. Change the valve position to 29% using the
▲ arrow key. The unit should begin its start
sequence and fire.
10.
Next, verify that the gas pressure
downstream of the SSOV is 2.3” W.C. for
both FM and IRI gas trains. If gas pressure
adjustment is required, remove the brass
hex nut on the SSOV actuator (IRI gas train)
containing the gas pressure regulator
(Figure 4-3). Make gas regulator adjust-
ments using a flat-tip screwdriver to obtain
2.3” W.C.
11. Raise the valve position to 100% and verify
that the gas pressure downstream of the
SSOV remains at 2.3” W.C. Readjust
pressure if necessary.
12. With the valve position at 100%, insert the
combustion analyzer probe into the flue
probe opening and allow enough time for the
combustion analyzer to settle.
13. Compare the measured oxygen % level to
the range shown below. Also, ensure that
the carbon monoxide (CO) and nitrogen
oxide (NOx) readings do not exceed the
values shown.
Combustion Oxygen Levels for a 100%
Valve Position
Oxygen %
± 0.2
Carbon
Monoxide
NOx
4.8 %
<100 ppm
<100 ppm
14. If necessary, adjust the iris air damper
shown in Figure 4-4 until the oxygen level is
within the range specified in Table 4-2.
15. Once the oxygen level is within the specified
range at 100%, lower the valve position to
80%.
NOTE
The remaining combustion calibration
steps are performed using the
Combustion Cal Menu
included in the C-
More Control System. The combustion
calibration control functions will be used
to adjust the oxygen level (%) at valve
positions of 80%, 60%, 45%, 30% and
20% as described in the following steps.
These steps assume that the inlet air
temperature is within the range of 50°F to
100°F.
4-6