Auto-cut 200 xt – Tweco 200 XT Auto-Cut 380V User Manual
Page 129
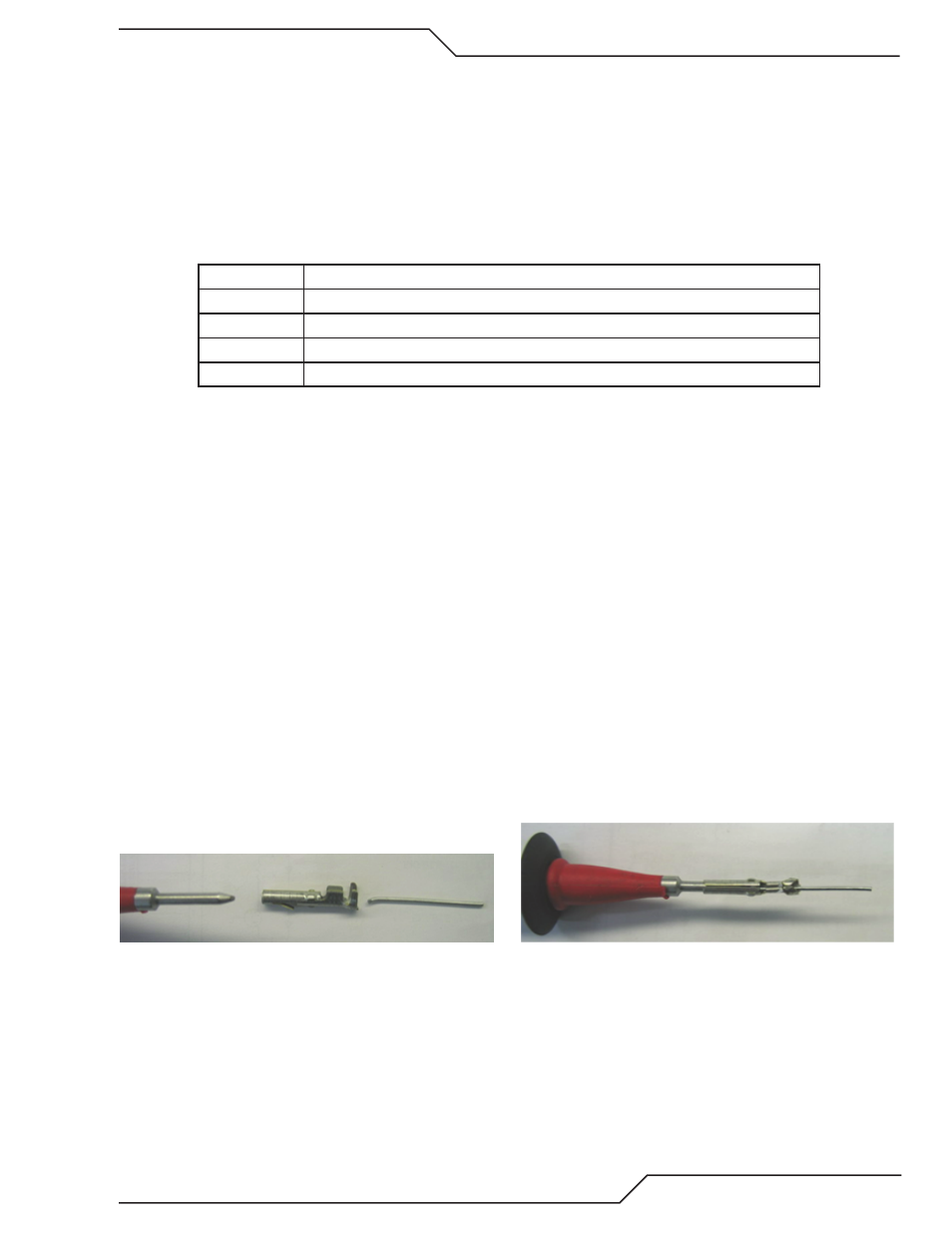
AUTO-CUT 200 XT
Manual 0-5253
APPENDIX
A-43
Status codes.
The codes for the power supply are displayed on the Display PCB 4 digit numerical display. Some codes refer to
the Gas Controls but more detailed Gas Control codes will be found on the individual gas controls. The gas con-
trols used with the XT family of plasma supplies have not changed. They have their own set of status codes which
should be covered in another section. This guide assumes you have first considered the Status Code Tables in the
Operation Section of the unit manual. Individual codes will point to different inverter sections while this guide
groups similar codes together. For example code E (or L) 249 indicates an inverter fault in Inverter 2A. This guide
covers codes 247-252 in one section as they are all the same, varying only by which inverter and section they refer to.
The codes are separated into 6 groups.
Group 1
Plasma Process -- Relating to pilot, transfer, torch voltages, etc.
Group 2
Plasma Power Supply -- Primarily the Inverter Sections
Group 3
Interface to Gas controls -- Mainly the DFC 3000
Group 4
Cooling System -- The liquid cooling system for the torch and inverters
Group 5
CCM -- Communications port to the gas controls
For the XT units we are using a 3 digit code with group 1 codes in the 100’s, group 2 in the 200s etc. These correspond
to the older codes used in previous units, where 1-1 is now 101. For the most part the codes have the same mean-
ing. Where an older code no longer applies to the XT system we don’t use it over again and have left it reserved to
avoid confusion. For example the code 204 (2-4) which meant the inverter module wasn’t ready. We now detect
that error in a different way that has a somewhat different meaning so we have reserved the 204 Code.
While most of the codes indicate a fault has occurred, a few of them, such as 304 (formerly 3-4), simply refer to
the current status. 304 indicates either “priming” where the pump is filling the system with coolant or more often
“purging” where the gas is flowing to dry the consumables after replacing them or purging the gas lines when a
different gas type has been selected.
Troubleshooting (General)
In many cases where the cause may be listed as a cable or wire disconnected but also includes loose or broken.
All Ribbon cables have an extra receptacle near one end for measuring signals on the cable.
A number of the measurements will require probing of some small connectors or measuring signal on ribbon cables.
For probing the small connectors, standard meter probes are usually too big. We suggest making a couple probes
using steel wire. Copper buss wire isn’t stiff enough. A paper clip is a little too big. One idea is take a socket from
an Amp mate-n-loc or similar connector into which your meter probe will fit and crimp a small piece of steel wire,
(0.020 to 0.025” dia.; (0.5-0.6 mm) works best), into where wire would normally be crimped. The wire should be
soldered and crimped. The steel wire may be found in hobby stores that cater to model building.
Art # 12302
Art # 12303
Insulate all but the end of the wire and slide these onto your meter probe. If your meter has alligator clip adaptors
you could hold the wire in these as well, be sure they don’t short together.
Problems that do not set Status or Fault codes:
1. At power on GAS LED blinks continuously, no code set. Real problem is no or low coolant flow but it takes
4 minutes before code is set and people don’t wait that long.