Periodic checks, Repairs, Specifications – Banner Compact Plastic Style Safety Interlock Switches User Manual
Page 5
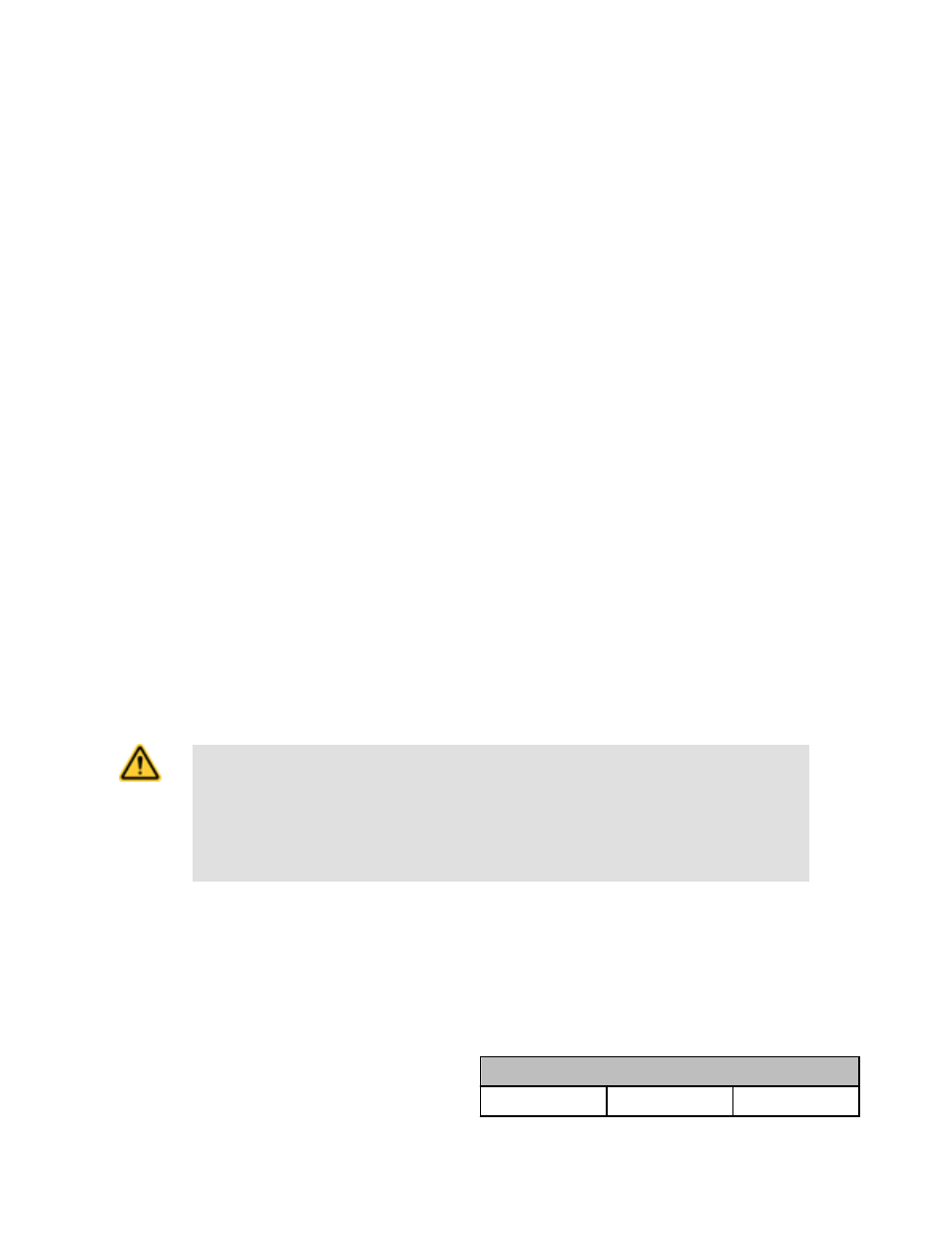
2. provide a reset routine after closing the guard and returning the safety switch contacts to their closed position. This prevents the
controlled machinery from restarting by simply reinserting the safety switch actuators. This necessary reset function is required by
ANSI B11 and NFPA 79 machine safety standards.
Use only a positively driven, normally closed safety contact from each switch for connection to the safety module. The normally open
contact may be used for control functions that are not safety-related. A typical use is to communicate switch status to a process control-
ler. Refer to the installation instructions provided with the safety modules for more information regarding the interface of the safety mod-
ule to the machine stop control elements.
Periodic Checks
Safety switches should be checked at each shift change or machine setup by a designated person for:
1. Breakage of the switch body or actuator,
2. Good alignment and full engagement of the actuator with the receptor,
3. Confirmation that the safety switch is not being used as an end stop,
4. Loosening of the switch or actuator mounting hardware, and
5. Verification that it is not possible to reach any hazard point through an opened guard (or any opening) before hazardous machine
motion has completely stopped.
In addition, a qualified person should check for the following on a periodic schedule determined by the user based upon the severity of
the operating environment and the frequency of switch actuations:
1. Check the wiring chamber for signs of contamination.
2. Check the contacts for signs of deterioration or damage.
3. Inspect the electrical wiring for continuity and damage.
4. Verify the wiring conforms to the instructions given in this datasheet.
A designated person is identified in writing by the employer as being appropriately trained to perform a specified checkout procedure. A
qualified person possesses a recognized degree or certificate or has extensive knowledge, training, and experience to be able to solve
problems relating to the safety switch installation (ANSI B30.2).
Repairs
Do not attempt any repairs to the Module. It contains no field-replaceable components. Return it to the factory for warranty repair
or replacement by contacting Banner Factory Application Engineering. They will attempt to troubleshoot the system from your description
of the problem. If they conclude a component is defective, they will issue a return merchandise authorization (RMA) number for your
paperwork and give you the proper shipping address.
Pack the Module carefully. Damage that occurs in return shipping is not covered by warranty.
CAUTION: Abuse of Module After Failure
If an internal fault has occurred and the Module will not reset, do not tap, strike, or otherwise attempt to
correct the fault by a physical impact to the housing. An internal relay may have failed in such a man-
ner that its replacement is required.
If the Module is not immediately replaced or repaired, multiple simultaneous failures may accumu-
late such that the safety function can not be guaranteed.
Specifications
Contact Rating
10A @ 24V ac, 10A @ 110V ac, 6A @ 230V ac; 6A @
24V dc
2.5 kV max. transient tolerance
NEMA A300 P300
Contact Material
Silver-nickel alloy
Maximum Switching Speed
30 operations per minute
European Rating
Utilization categories: AC15 and DC13 (IEC 60947-5-1)
Switches with 1 and 2 contact pairs: Ui = 500V ac; Ith =
10 A
Switches with 3 contact pairs: Ui = 400V ac; Ith = 5A
40-60 Hz
Ue
Ie/AC-15
Ie/DC-13
Limit-Switch Style Machine Safety Switches
P/N 059622 Rev. G
www.bannerengineering.com - tel: 763-544-3164
5