MTS WIFT Mini Transducer Interface User Manual
Page 76
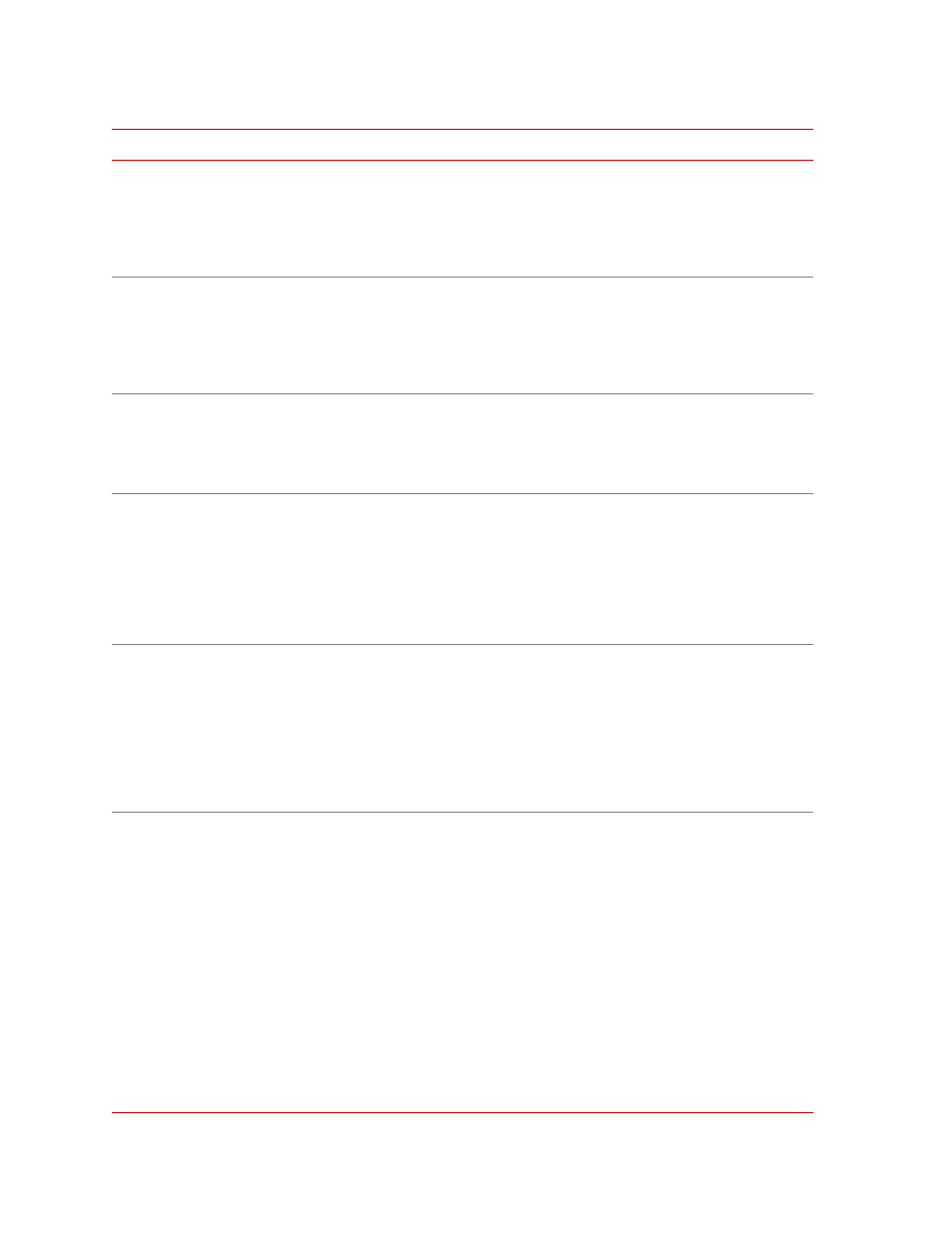
SWIFT
®
Mini TI
76
Troubleshooting
Zero Offset: One or more
Signal Outputs appear to
have an offset after the TI
electronics have been
zeroed.
The transducer was zeroed
with load applied (or a
different load than the
intended tare weight for
non-spinning applications
only).
Rezero the TI, being careful not to touch or load
the transducer during the zero procedure.
Considerable temperature
changes have occurred.
The transducer is temperature-compensated to
reduce temperature-induced errors, but any
significant changes in temperature will induce
zero shifts. For best results, zeroing should
occur at the conditions closest to those of the
test conditions.
Noise in the system.
Noise in the power supply or high magnetic
fields can cause errors in the zeroes. For more
information, see grounding suggestions in
“Transducer Interface Electronics Installation”
Zero button was pressed
with cables not connected,
or during a loaded test
If the Zero button is pressed with the cables not
connected, the TI Electronics will set the new
zero values according to this zero voltage
signal. If the Zero button is accidentally pressed
during a test, the TI electronics will zero the
bridges at whatever load they are reading at the
time the Zero button was pressed, resulting in
an erroneous bridge zero value.
The data acquisition
configuration or input ports
show a zero offset.
After zeroing, while the TI is turned on and all
cables from the SWIFT transducer to TI are
connected, use a handheld DVM to verify the
output of individual channels while they are
being loaded. With no load applied, the outputs
should be 0 V. If the data acquisition is showing
an offset while the TI reads 0 V (as measured by
the handheld DVM), the data acquisition is set
up incorrectly, or is inducing the offset.
The reference angle of the
transducer is set incorrectly
in non-spinning (fixed)
mode.
The AngleFixed value in the TI calibration file
is initially set to zero, indicating that the
coordinate outputs shown on the transducer
label are correct when the label is upright. If the
label is not upright, or if the AngleFixed value
in the calibration file is not set correctly, the
angular transformation may be causing the
error.
For example, if the transducer should be sensing
only a vertical load with the vehicle at rest, but
the angle is set incorrectly, it may give an output
of longitudinal load and vertical load based on
this erroneous axis orientation set by the
AngleFixed value. To correct, verify that the
AngleFixed value matches the actual
orientation of the transducer.
Troubleshooting Guide (part 3 of 11)
Symptom
Possible Causes
Solution