Chapter 2 operation, 5 sensor setup – INFICON SQC-222 Thin Film Deposition Controller User Manual
Page 27
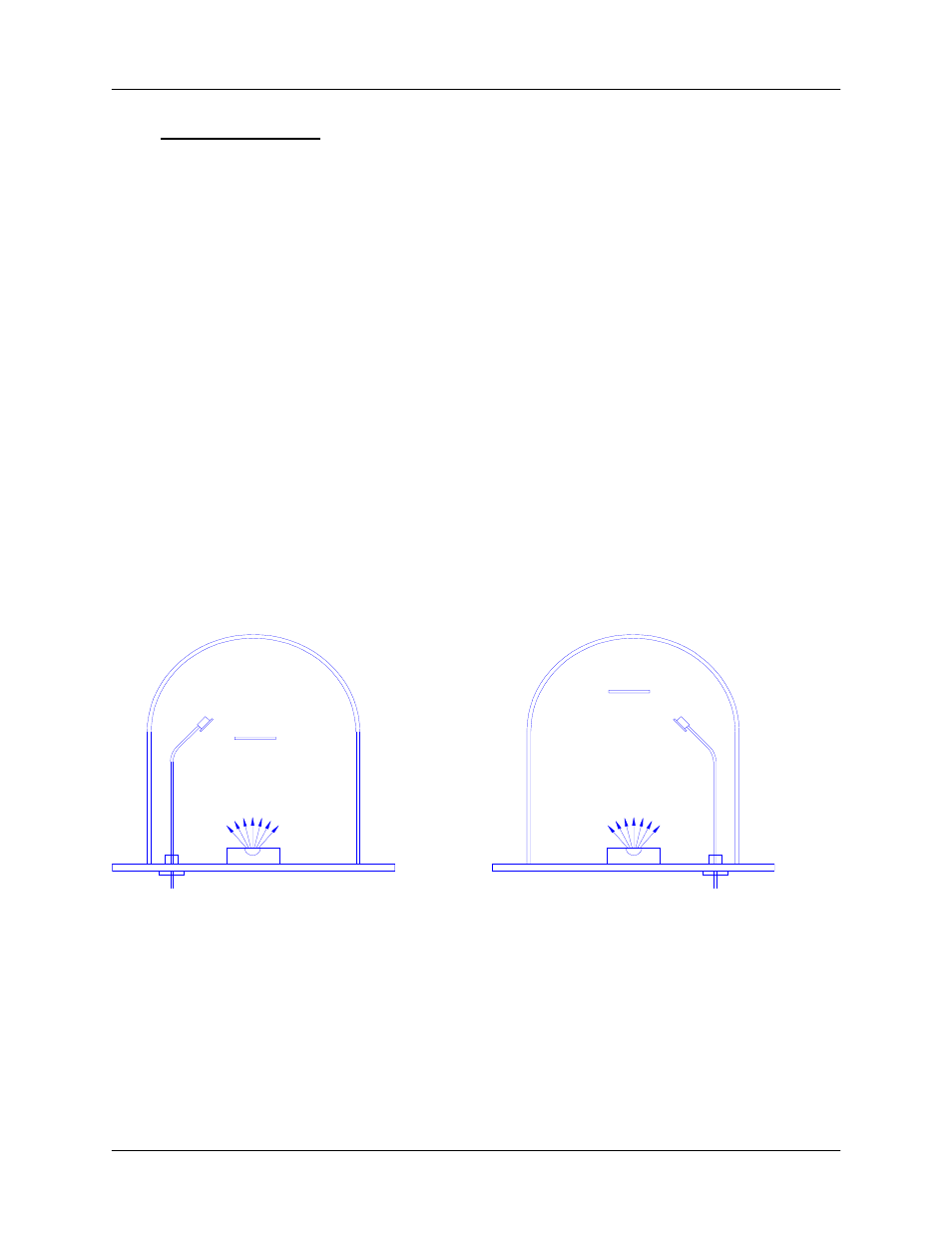
Chapter 2
Operation
2-8
2.5 Sensor Setup
Sensor setup involves selecting the sensor(s) to be used, setting the Min/Max crystal
frequencies, and adjusting the Tooling Factor.
In the System Params menu, Max Frequency is the initial frequency of a new crystal,
typically 6.0e+06 Hz (6 MHz). Due to manufacturing tolerances, some crystals may
oscillate above 6MHz initially, which would be detected as a sensor error. Setting the
Max Frequency slightly above the nominal value, to say 6.1 MHz will avoid this problem.
Min Frequency is the frequency where the SQC-222 will flag a sensor as bad. For a
6 MHz crystal, the Min Frequency is typically 5 MHz. Crystal failure is often predicted
by periods of “mode hopping,” where the crystal briefly makes an abrupt change in
frequency, or stops oscillating altogether. Some materials will cause crystals to fail or
mode hop well before 5 MHz. It is good practice to set the Min Frequency to a value
that indicates crystal failure in you process well before crystals actually fail.
To better determine impending crystal failure, Crystal Quality and Stability parameters
are also available for each Film. See Chapter 3, Film Menus, for more information on
setting Crystal Quality and Stability.
Sensor Tooling and System Tooling (System Params menu) adjusts for the difference
in measured deposition rate between the sensor and the substrate being coated.
Substrate
Substrate
Tooling
Over 100%
Tooling
Under 100%
In the left illustration above, the sensor will measure less rate or thickness than is
actually deposited on the substrate because of its positioning. In the right illustration,
the sensor will measure high. Tooling is the ratio of the actual substrate deposition rate
or thickness, to that measured by the sensor.
Let’s assume that at the end of deposition the sensor measures a thickness of 1.000
kA. But, suppose the actual substrate is deposited to 1.100 kA thickness (as