Integrating the gold bell on a pcb, Traces, Grounds and returns – ElmoMC Gold Line Digital Servo Drives-Gold Bell User Manual
Page 34: Traces 4.5.2. grounds and returns
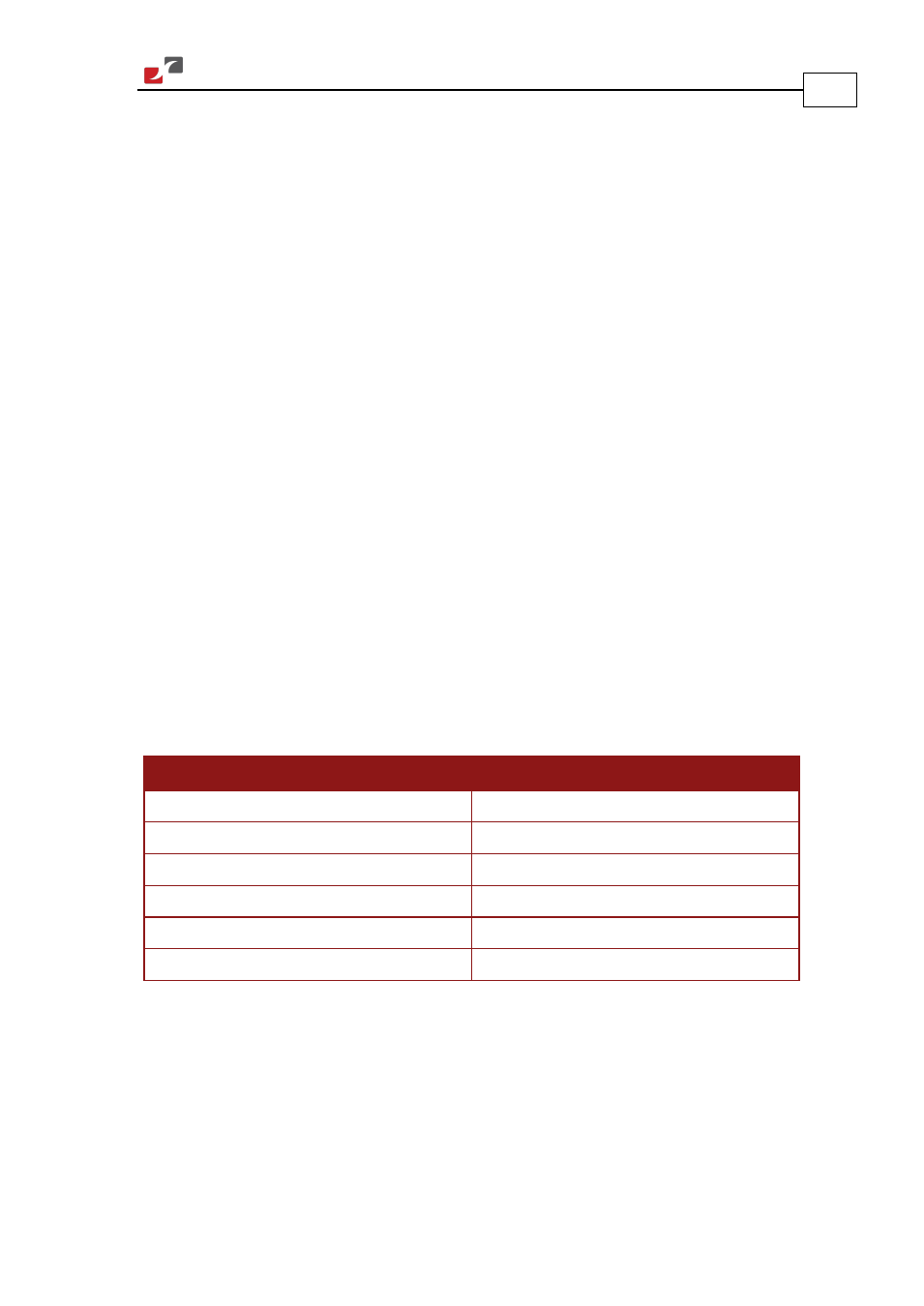
Gold Bell Installation Guide
Installation
MAN-G-BELIG (Ver. 1.004)
34
4.5. Integrating the Gold Bell on a PCB
The Gold Bell is designed to be mounted on a PCB, either by soldering its pins directly to the
PCB or by using suitable socket connectors. In both cases the following rules apply:
4.5.1.
Traces
1.
The size of the traces on the PCB (thickness and width) is determined by the current
carrying capacity required by the application.
•
The rated continuous current limit (Ic) of the Gold Bell is the current used for sizing
the motor traces (M1, M2, M3, M4 and PE) and power traces (VP+, PR and PE).
•
For control, feedbacks and Input/Output conductors, the actual current is very small
but a greater thickness and width of the conductors will contribute to better
performance and less interference.
2.
The traces should be as short as possible to minimize EMI and also to minimize the heat
generated by the conductors.
3.
The spacing between the high voltage conductors (VP+, PR, M1, M2, M3, M4, VL) must be
at least:
•
Surface layer: 1.5 mm
•
Internal layer: 0.10 mm
Complying with the rules above will help satisfy UL safety standards, MIL-STD-275 and the IPC-
D-275 standard for non-coated conductors, operating at voltages lower than 200 VDC.
4.5.2.
Grounds and Returns
The returns in each functional block are listed below:
Functional Block
Return Pin
Power
PR (Power Return)
Internal Switch Mode P. S.
PR (Power Return)
Analog input return
ANLRET (J2/20)
Common return
COMRET (J2/25,31,32,43,46; J1/23)
STO safety signal return
STO_RET (J1/10)
Input Return
IN_RET (J1/3)
Table 8: Grounds and Returns