10 cylinder removal and installation, Lift cylinder removal, Lift cylinder installation – JLG M4069 ANSI Service Manual User Manual
Page 77: Cylinder removal and installation -5
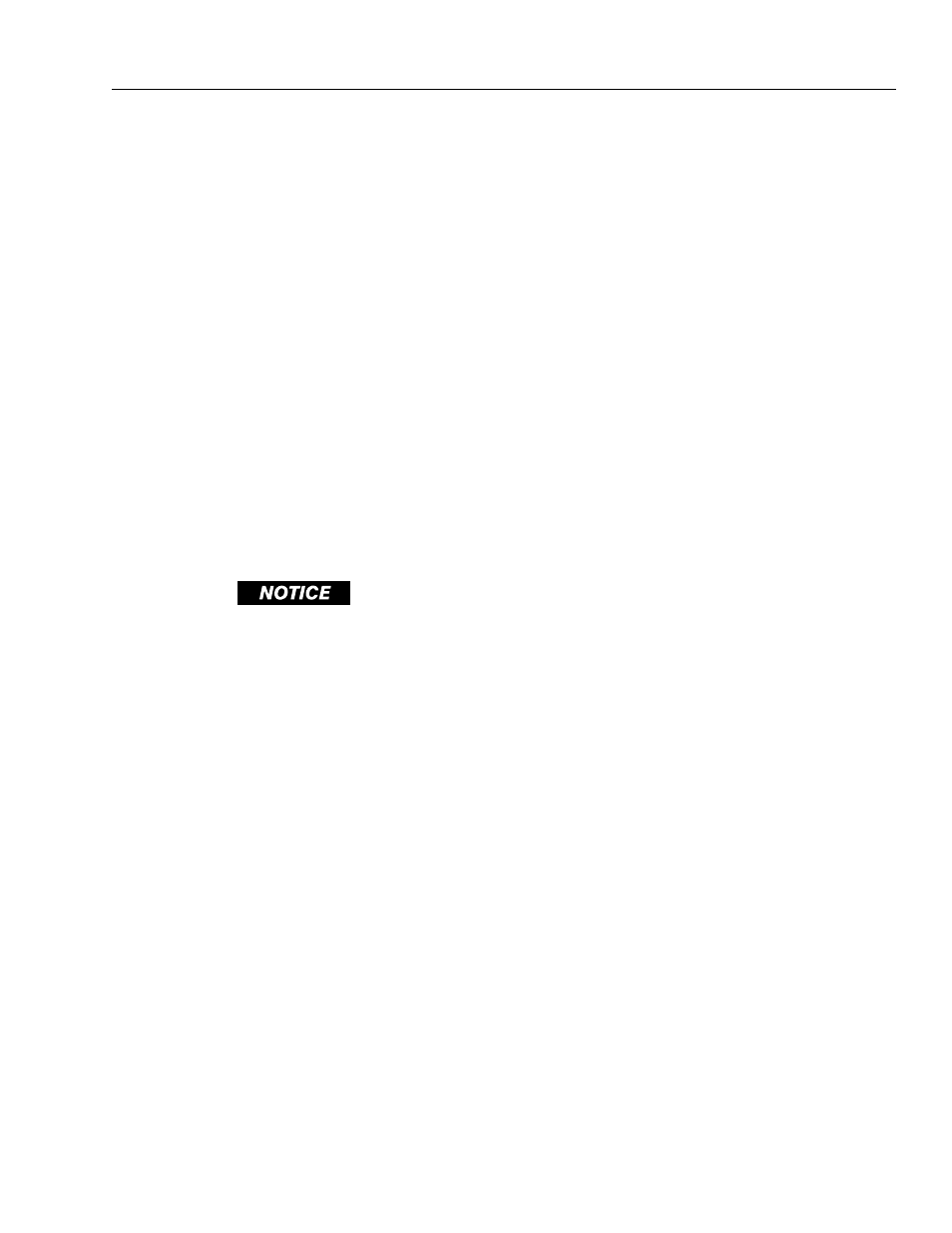
SECTION 4 - HYDRAULICS
3121122
– JLG Lift –
4-5
lines. Carefully remove hydraulic hoses from appro-
priate cylinder port block.
4. There will be initial weeping of hydraulic fluid, which
can be caught in a suitable container. After the initial
discharge, there should not be any further leakage
from the ports. If leakage continues at a rate of 6-8
drops per minute or more, the following cylinder
repairs must be made. If the retract port is leaking,
the piston is leaking, the piston seals are defective
and must be replaced. If the extend port is leaking,
the counterbalance is defective and must be
replaced.
5. If no repairs are necessary or when repairs have
been made, carefully reconnect hydraulic hoses to
the appropriate ports.
6. Remove lifting device from platform, activate hydrau-
lic system and run cylinder through complete cycle
to check for leaks and operation.
Cylinders with Duel Counterbalance Valves
(Oscillating Cylinders)
OPERATE ALL FUNCTIONS FROM GROUND CONTROL STATION
ONLY.
1. When working on oscillating axle cylinder, place
machine on firm level surface.
2. Using all applicable safety precautions, activate
hydraulic system.
3. Shut down hydraulic system and allow machine to
sit for 10-15 minutes. This is done to relieve pressure
in the hydraulic lines. Carefully remove hydraulic
hoses from appropriate cylinder port block.
4. There will be initial weeping of hydraulic fluid, which
can be caught in a suitable container. After the initial
discharge, there should not be any further leakage
from the ports. If leakage continues at a rate of 6-8
drops per minute or more, the following cylinder
repairs must be made. If the retract port is leaking,
the piston is leaking, the piston seals are defective
and must be replaced. If the extend port is leaking,
the counterbalance is defective and must be
replaced.
5. To check piston seals, carefully remove the counter-
balance valve from the retract port. After initial dis-
charge there should not be any further leakage from
the ports. If leakage occurs at a rate of 6-8 drops per
minute or more, the piston seals are defective and
must be replaced.
6. If no repairs are necessary or when repairs have
been made, carefully reconnect hydraulic hoses to
the appropriate ports.
7. Activate hydraulic system and run cylinder through
complete cycle to check for leaks and operation.
4.10 CYLINDER REMOVAL AND
INSTALLATION
Lift Cylinder Removal
1. Place the machine on a flat and level surface. Turn
power on and raise the platform. Turn power off and
attach a suitable lifting device to the platform.
2. Remove the bolt, locknut and keeper shaft securing
the cylinder rod attach pin to the upper inner arm
assembly. Using a suitable brass drift, drive out the
rod end attach pin from the arm assembly.
3. Retract the cylinder rod completely.
4. Tag and disconnect, then cap the lift cylinder
hydraulic lines and ports.
5. Remove the bolt, locknut and keeper shaft securing
the cylinder barrel attach pin to the upper inner arm
assembly. Using a suitable brass drift, drive out the
rod end attach pin from the arm assembly.
6. Carefully remove the cylinder from the scissor lift
and place in a suitable work area.
Lift Cylinder Installation
1. Install lift cylinder in place using a suitable slings,
aligning barrel end attaching pin mounting holes on
lower arm assembly.
2. Using a suitable drift, drive the barrel end attach pin
through the mounting holes in the lift cylinder and
the lower arm assembly. Secure in place with bolt,
locknut and keeper shaft.
3. Remove cylinder port plugs and hydraulic line caps
and correctly attach lines to cylinder ports.
4. Extend the cylinder rod until the attach pin hole
aligns with those in the upper arm assembly. Using a
suitable drift, drive the cylinder rod attach pin
through the aligned holes, taking care to align the
pin retaining holes with the hole on the arm assem-
bly. Secure the pin in place with bolt, locknut and
keeper shaft.
5. Lower platform to stowed position and shut down
motor. Check hydraulic fluid level and adjust accord-
ingly.
NOTE: Always check hydraulic fluid level after completely
elevating and lowering machine.