Power supply connections, Input connections, Remote setpoint – NOVUS Controller N1200 User Manual
Page 5: Digital input connections, Connection of alarms and outputs, Operation
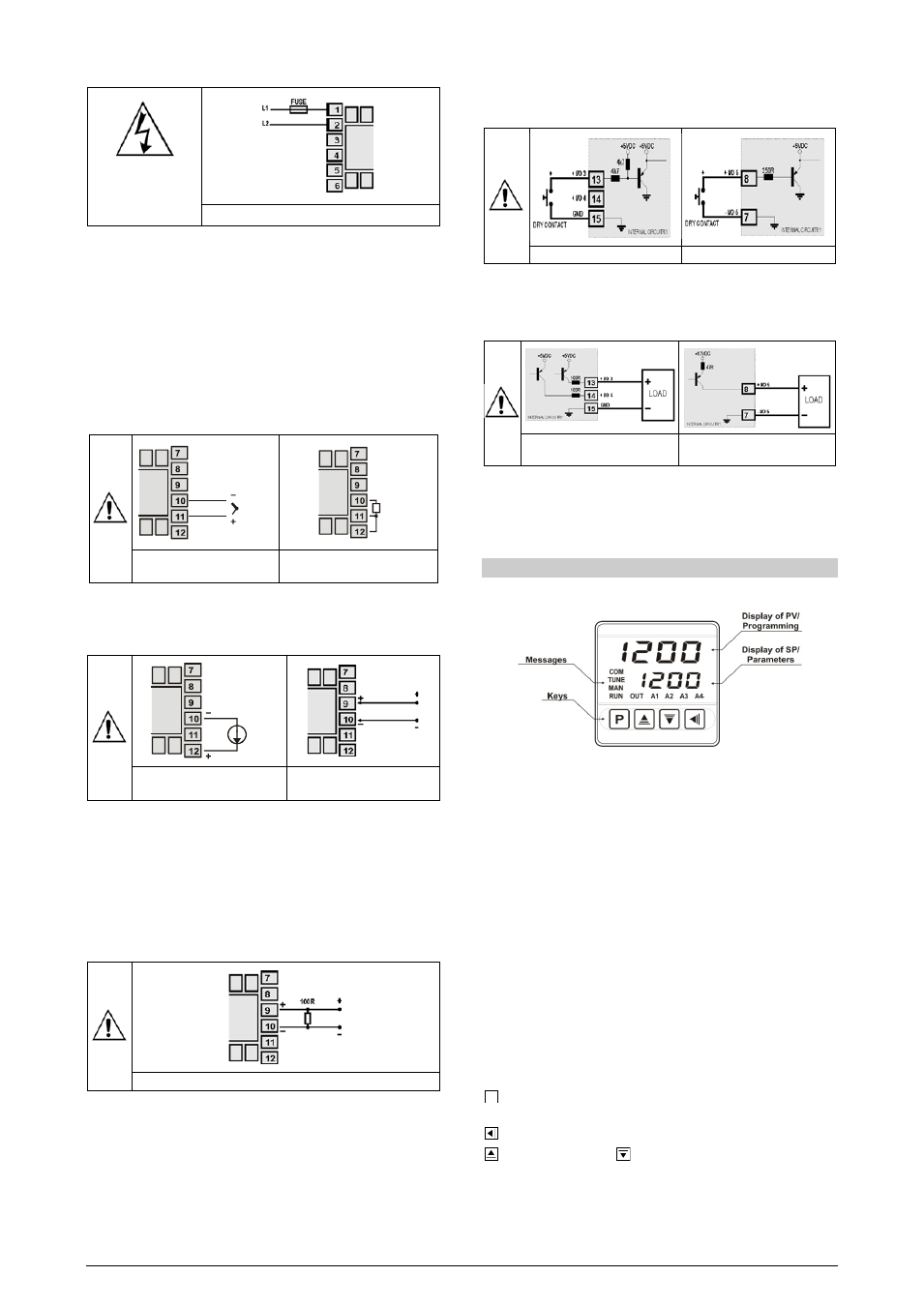
Controller N1200
NOVUS AUTOMATION
5 / 13
Power Supply Connections
Observe the power
requirement for the
unit. of required power
supply
Figure 2 – Power supply connections
Input Connections
• Thermocouple (T/C) and 0-50 mV
The Figure 3a indicates the wiring for the thermocouple and 0-50mV
signals. If the thermocouple wires needs to be extended, use
appropriate compensation cables.
• RTD (Pt100):
Figure 3b shows the Pt100 wiring, for 3 conductors. For proper cable
length compensation, use conductors of same gauge and length).
For 4-wires Pt100, leave one conductor disconnected at the
controller. For 2-wire Pt100, short-circuit terminals 11 and 12.
T/C, 0-50mV
Figure 3a - Connection of T/C,
0-50mV
Figure 3b - Connection of three
wire Pt100-3
• 4-20 mA:
The connections for current signals 4-20 mA must be carried-out
according to Figure 4a.
Figure 4a - Current connection
4-20 mA
Figure 4b - Connection for 5V
and 10V
• 5 V and 10 V
Refer to Figure 4b for connecting voltage signals.
Remote Setpoint
Feature available in the controller's terminals 9 and 10. When the
Remote SP input signal is 0-20 mA or 4-20 mA, an external
100Ω shunt resistor of must be connected to terminals 9 and 10 as
indicated in Figure 4c.
Figure 4c - Connection for remote SP
Digital Input Connections
Figures 5a and 5b show switches driving I/O 3 and I/O 5. The same
scheme applies to I/O 4
Figure 5a – I/ O3 a Digital Input Figure 5b – I/O5 a Digital Input
Connection of Alarms and Outputs
The I/O channels, when configured as outputs, must have their load
limit capacities observed, according to the product specifications.
Figure 6a – I/ O3 or I/O4 with
output pulse for SSR.
Figure 6b – I/O5 with output
pulse for SSR.
I/O3, I/O4 and I/O5 can also be configured as digital outputs (I/O3 and
I/O4 provide a 5 Vdc output signal whereas I/O5 a 12 Vdc signal). An
example of usage is shown in Figure 6a for the I/O3 and in Figure 6b
for the I/O5. I/O5 is electrically isolated from the sensor input
OPERATION
The controller's front panel, with its parts, can be seen in the Figure 7:
Figure 7 - Identification of the parts referring to the front panel
Display of PV/Programming: Displays the current value of PV
(Process Variable). When in configuration mode, it shows the
parameters names.
Display of SP/Parameters: Displays the value of SP (Setpoint).
When in configuration mode, it shows the parameters values.
COM indicator: Flashes to indicate communication activity in the
RS485 interface.
TUNE indicator: Stays ON while the controller is in tuning process.
MAN indicator: Signals that the controller is in the manual control
mode.
RUN indicator: Indicates that the controller is active, with the control
output and alarms enabled.
OUT indicator: For relay or pulse control output; it reflects the actual
state of the output. If an analog output is assigned for control, the
OUT indicator lights continuously.
A1, A2, A3 and A4 indicators: signalize the occurrence of alarm
situation.
P
P Key (Program key): used to walk through the menu
parameters.
Back Key: used to retrocede parameters.
Increment key and
- Decrement key: allow altering the
values of the parameters.
When the controller is powered on, its firmware version is presented
for 3 seconds, after which the controller starts normal operation. The
values of PV and SP are displayed and the outputs are enabled.
Pt100
4-20mA