Flow rate, Tubing length and diameter – Campbell Scientific TGA100 Trace Gas Analyzer Manual User Manual
Page 76
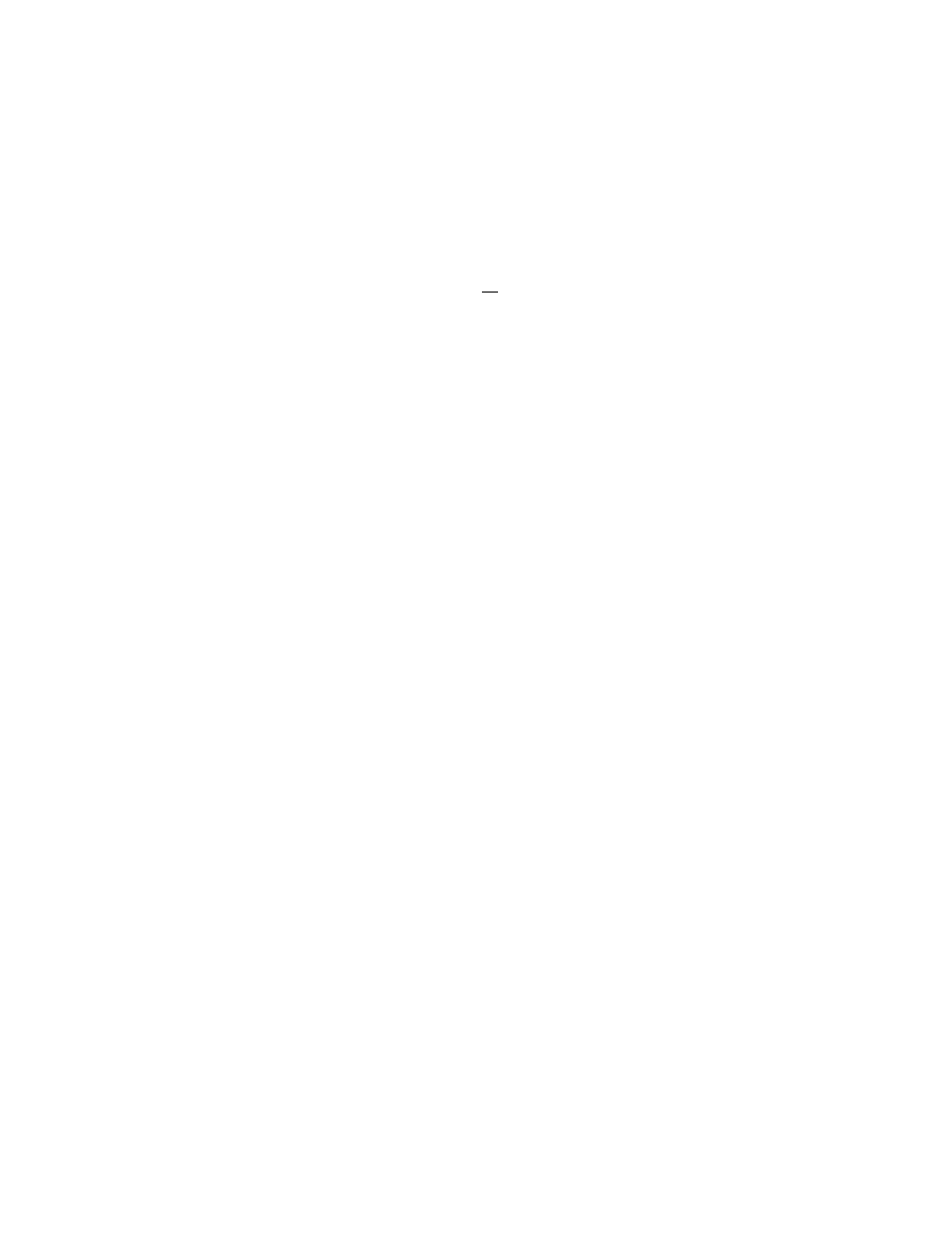
5.1.7.1 Flow Rate
The sample flow rate should be high enough to minimize the equilibration time after valve switching, but low enough
to avoid a possible bias between sample intakes. Two issues that can affect the equilibration time are the time to replace
the sample in the sample cell, and mixing in the tubing. The time to replace the sample in the sample cell depends on
the actual flow rate and the volume of the sample cell:
q
v
t
/
=
where t is time, v is volume, and q is actual flow rate. Substituting the TGA100 sample volume (480 ml), converting
actual flow rate to standard flow rate, and converting some units gives a more useful form of this equation:
Q
P
T
028
.
0
=
where T is time (s) to replace the sample volume, P is the pressure (mbar) in the sample cell, and Q is flow rate
(standard l/min or slpm). With a relatively high pressure (75 mbar) and a relatively low flow rate (2 slpm) the time is
one second, and will be even lower for most cases, where the flow rate is higher and/or the pressure is lower.
Mixing in the sample tubing depends on the tubing length and diameter, and the flow rate. In general it is best to have
short, small-diameter tubing and a high flow rate to minimize mixing. However, mixing is not a problem for most
gradient applications, because the equilibration time is normally only a few seconds, even for tubing lengths of 100 to
200 m.
The maximum flow rate must also be considered. It is extremely important when measuring concentration gradients to
avoid a systematic bias between the two intakes. One possible cause for such a bias is unequal flow rates. There will
always be a pressure drop along the sample cell. Therefore, even though the outlets of the sample and reference cells
are connected inside the analyzer, the pressure drop along the sample cell causes a small pressure difference between
the reference and sample cells, leading to an error in the measured concentration. This TGA100 is designed to minimize
this pressure drop, which normally introduces only a small error in the concentration measurement. However, at high
flow rates, unequal flow rates for the two intakes can give a measurable bias in the concentration difference. To
minimize this problem:
1) The flow rate should generally be no greater than 10 to 15 slpm.
2) For the same standard flow rate, higher pressure in the sample cell reduces the pressure drop (the pressure drop is
related to the actual flow rate, which is inversely related to pressure).
3) The gradient valve assembly and the intake assemblies must be carefully designed to match the flow rate between
the two intakes.
• The filter and the needle valve or orifice should be located downstream of the gradient valve assembly, in
common with both intakes.
• The intake assemblies and tubing upstream of the gradient valve assembly should be well matched, and should
have minimum flow restriction.
• A pair of two-way valves (
) will generally be better matched than the two inlets of a single three-
way valve (
).
A well designed sampling system and flow rates below 15 slpm will give an intake bias well below the detection limit.
5.1.7.2 Tubing Length and Diameter
In some cases it is convenient to locate the analyzer at the base of the instrumentation mast and use a very short tube
from the gradient valve assembly to the analyzer. In other cases it is more convenient to locate the analyzer some
distance away from the intake mast. For example, to measure gradients at multiple sites the analyzer is generally placed
between the sites with relatively long tubes to each of the gradient valve assemblies. The ability to use long sample
tubes is an advantage of the flux gradient method over the eddy covariance method, which requires short sample tubing
to preserve the high frequencies in the data.
To choose tubing diameter and lengths, the two main considerations are the pressure drop in the tubing and the travel
time.
give the predicted pressure drop and travel time for several flow rates and tubing
diameters.
76