5 microprocessor reset facility, 6 diagnostics display, Troubleshooting – Dwyer Series PUB User Manual
Page 39
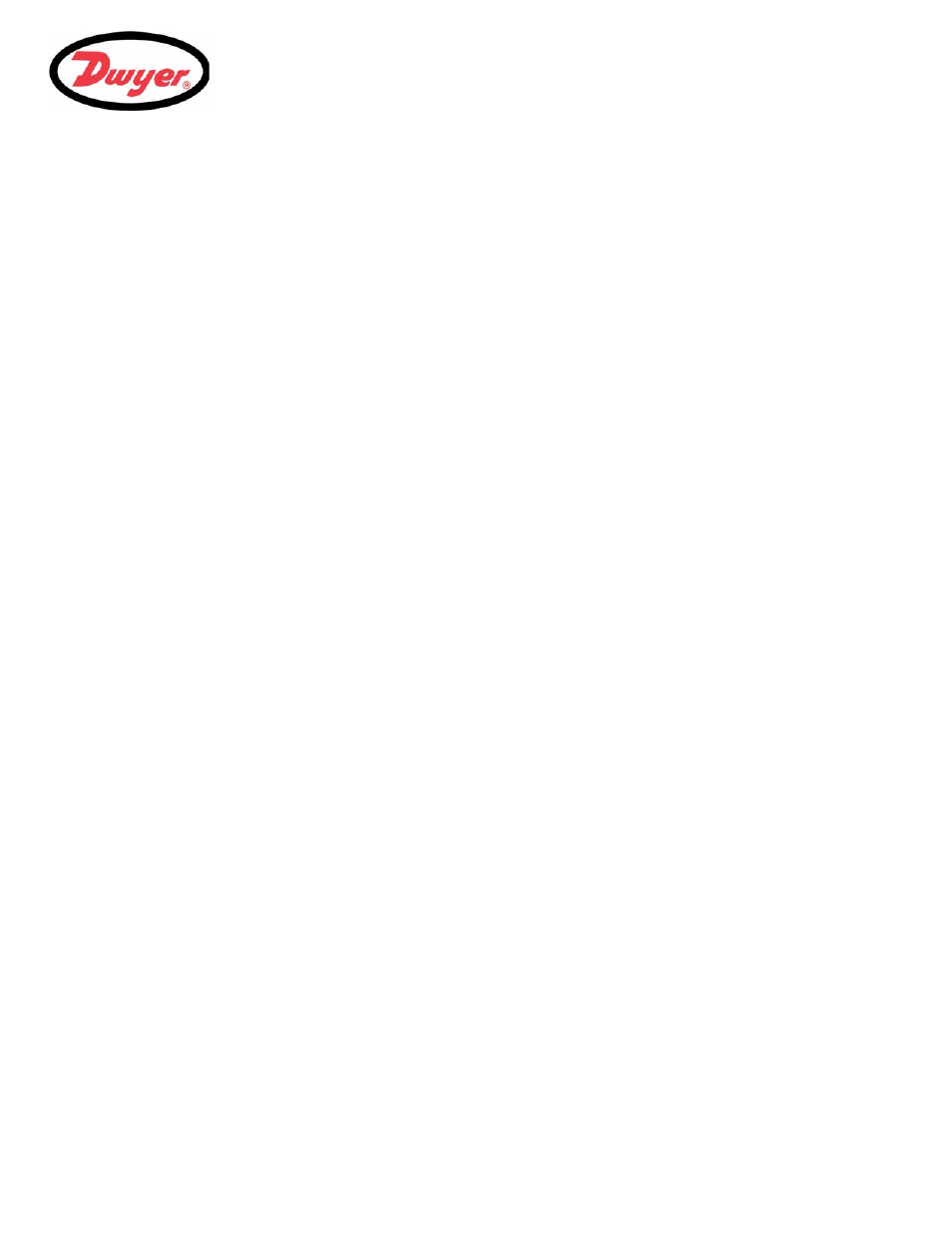
5: Troubleshooting
35
5.
Select
Sensor mode and position the cursor at Diagonal and press ENTER to return to the SENSOR
SELECTION menu.
6.
Select
Exit and press ENTER to return to the SENSOR SEPARATION screen.
7.
Check that the parameters displayed are correct.
8.
Apply acoustic couplant to the sensors and attach them to the test block with the connectors positioned
towards the center of the test block as shown, and temporarily secure them in place using elastic bands or
tape.
9.
Connect the sensors to the PUB instrument using the cables provided.
10. Press
ENTER to go to the FLOW READING screen.
11. Select the
Options key to go to the FLOW READING OPTION menu and set the Damping to at least 10
seconds.
12. Select
Exit and press ENTER to return to the FLOW READING menu.
13. The flow reading value displayed is not important. The fact that a reading is obtained indicates that the
instrument is functioning. This value may fluctuate but this is normal.
14. The signal strength indicator at the left of the display should show 3–4 bars.
5.5
Microprocessor Reset Facility
In the rare event that the PUB instrument appears to totally hang-up, or the display is indistinguishable, you can
reset its microprocessor by carefully inserting a straightened paperclip into the pinhole located in the right-hand
side of the instrument to operate the internal reset switch. Hold the paperclip perpendicular to the instrument
while doing this.
5.6
Diagnostics Display
This feature is designed for advanced users and is intended to provide information that will aid the user to
diagnose problems – e.g. no signal strength.
When operating in the
FLOW READING mode you can access a diagnostics screen by pressing the Options
function key and then selecting
Diagnostics from the FLOW READING OPTIONS screen. This will display the
operating values for the following parameters.
Calculated time (µs)
This is a value the instrument predicts will be the time in µsecs that it should take for the acoustic wave to
propagate across a particular pipe size. This value is ascertained from the data entered by the user. i.e. Pipe size,
material, sensor set etc.
Actual time (µs)
This is the value the instrument measures as the time taken for the acoustic wave to propagate across the pipe. It
is used to see if the signal is being taken from the burst, at the correct time to get the strongest signal. This value
is normally a few µs below the calculated µs value. If, however, this value is much greater than the calculated
time, there is a problem with the set-up.
Flow (m/s)
This displays flow velocity in m/s to 3 decimal places.
Signal strength
This is the averaged value of Signal and should be a value between 800 and 1600 – where 800 is approximately
50%, and 1600 is approximately 100%.