Dwyer GFM4 User Manual
Page 12
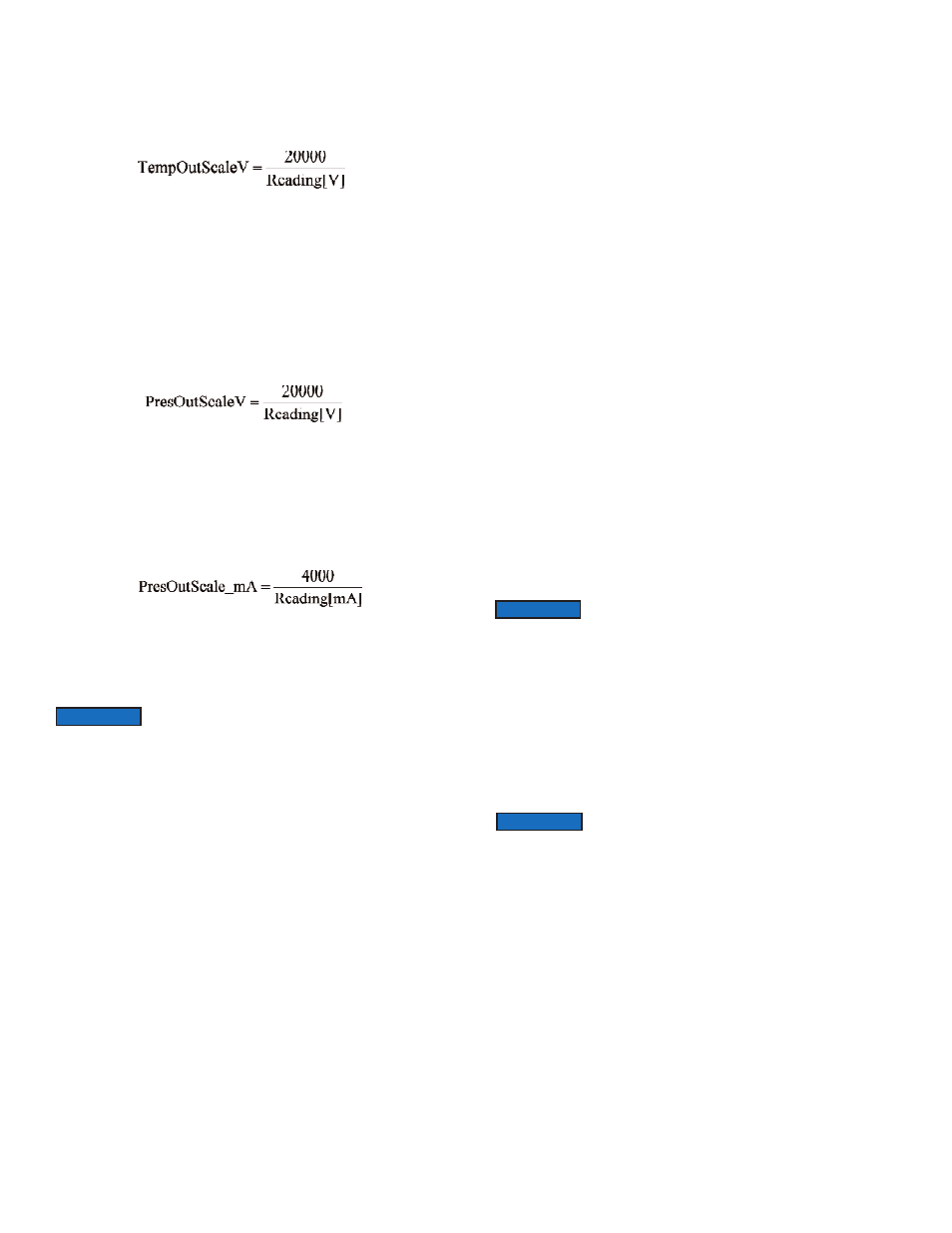
7.3.5 - Gas temperature 4 to 20 mA Analog Output Calibration (GFM4)
1. Install jumpers J3 on the analog PC board for 4 to 20 mA output (see Table VI).
2. Connect a certified high sensitivity multi-meter set for the current measurement
to the pins 3 (+) and 16 (-) of the 25-pin D connector.
3. Write 4000 counts to the DAC channel 2: !11,WRITE,2,4000[CR].
4. Read current with the meter and calculate.
5. Write zero counts to the DAC channel 2: !11,WRITE,2,0CR].
6. Read offset current with the meter and calculate.
7. Save TempOutScale_mA in to the EEPROM: !11,MW,30,Y[CR].
Save TempOutOffset_mA in to the EEPROM: !11,MW,31,Z[CR].
Where: Y - the calculated TempOutScale_mA value.
Z - the calculated TempOutOffset_mA value.
7.3.6 - Gas Pressure 0 to 5 Vdc Analog Output Calibration (GFM3/4)
1. Install jumpers J4 on the analog PC board for 0 to 5 Vdc output (see Table VI).
2. Connect a certified high sensitivity multi-meter set for the voltage measurement
to the pins 4 (+) and 17 (-) of the 25-pin D connector.
3. Write 4000 counts to the DAC channel 3: !11,WRITE,3,4000[CR].
4. Read voltage with the meter and calculate.
5. Save PresOutScaleV in to the EEPROM: !11,MW,32,X[CR].
Where: X - the calculated PresOutScaleV value.
7.3.7 Gas pressure 4 to 20 mA Analog Output Calibration (GFM4)
1. Install jumpers J4 on the analog PC board for 4 to 20 mA output (see Table VI).
2. Connect a certified high sensitivity multi-meter set for the current measurement
to the pins 4 (+) and 17 (-) of the 25-pin D connector.
3. Write 4000 counts to the DAC channel 3: !11,WRITE,3,4000[CR].
4. Read current with the meter and calculate.
5. Write zero counts to the DAC channel 3: !11,WRITE,3,0CR].
6. Read offset current with the meter and calculate.
7. Save PresOutScale_mA in to the EEPROM: !11,MW,33,Y[CR].
Save PresOutOffset_mA in to the EEPROM: !11,MW,34,Z[CR].
Where: Y - the calculated PresOutScale_mA value.
Z - the calculated PresOutOffset_mA value.
Enable DAC update by typing: !11,WRITE,4,N[CR].
Unit will respond with: !11,DisableUpdate: N.
Close Backdoor mode by typing: !11,MW,1000,0[CR].
Unit will respond with: !11,BackDoorEnabled: N.
7.4 - Temperature and/or Pressure Sensor Calibration
Calibration of the temperature and pressure sensors for GFM3/4 devices is not
described in this manual. Temperature or/and pressure sensors re-calibration
requires factory assistance.
8. RS-485/RS-232 SOFTWARE INTERFACE COMMANDS
8.1 - General
The standard GFM3/4 comes with an RS-485 interface. For the optional RS-232
interface, the start character (!) and two hexadecimal characters for the address
have to be omitted. The protocol described below allows for communications with
the unit using either a custom software program or a "dumb terminal." All values
are sent as printable ASCII characters. For RS-485 interface, the start character is
always (!), and the command string is terminated with a carriage return (line feeds
are automatically stripped out by the GFM3/4). See section 2.2.3 for information
regarding communication parameters and cable connections.
8.2 - Commands Structure
The structure of the command string:
!
Where:
!
Start character **
Addr
RS485 device address in the ASCII representation of
hexadecimal (00 through FF are valid).**
Cmd
The one or two character command from the table
below.
Arg1 to Arg4
The command arguments from the table below.
Multiple arguments are comma delimited.
CR
Carriage Return character.
** Default address for all units is 11. Do not submit start character and two
character hexadecimal device address for RS-232 option.
Several examples of commands follow. All assume that the GFM3/4 has been
configured for address 15 (0F hex) on the RS485 bus:
1. To get the temperature reading:
!0F,TR
The GFM4 will reply:
!0F72.5 F
(Assuming temperature is 72.5F)
2. To get the pressure reading:
!0F,PR
The GFM4 will reply:
!0F14.5 PSI
(Assuming pressure is 14.5 PSI)
3. To get a flow reading:
!0F,F
The GFM3/4 will reply:
!0F50.0
(Assuming the flow is at 50%F.S.)
4. Set the high alarm limit to 85% FS:
!0F,A,H,85.0
The GFM3/4 will reply:
!0FAH85.0
The global address can be used to change RS-485 address for a particular device
with unknown address:
1. Make sure only one device (which address has to be changed) is connected to
the RS-485 network.
2.Type the memory write command with global address: !00,MW,7,XX[CR].
Where XX, the new hexadecimal address can be [01 - FF]. After assigning the
new address, a device will accept commands with the new address.
When done with the analog output calibration, make sure the
DAC update is enabled and the BackDoor is closed (see
command below).
NOTICE
Address 00 is reserved for global addressing. Do not assign
global address for any device. When command with global
address is sent, all devices on the RS-485 bus execute the command, but do not
reply with acknowledge message.
NOTICE
Do not assign the same RS-485 address for two or more
devices on the same RS-485 bus. If two or more devices with
the same address are connected to the one RS-485 network, the bus will be
corrupted and communication errors will occur.
NOTICE
Page 12