Dwyer GFM4 User Manual
Page 10
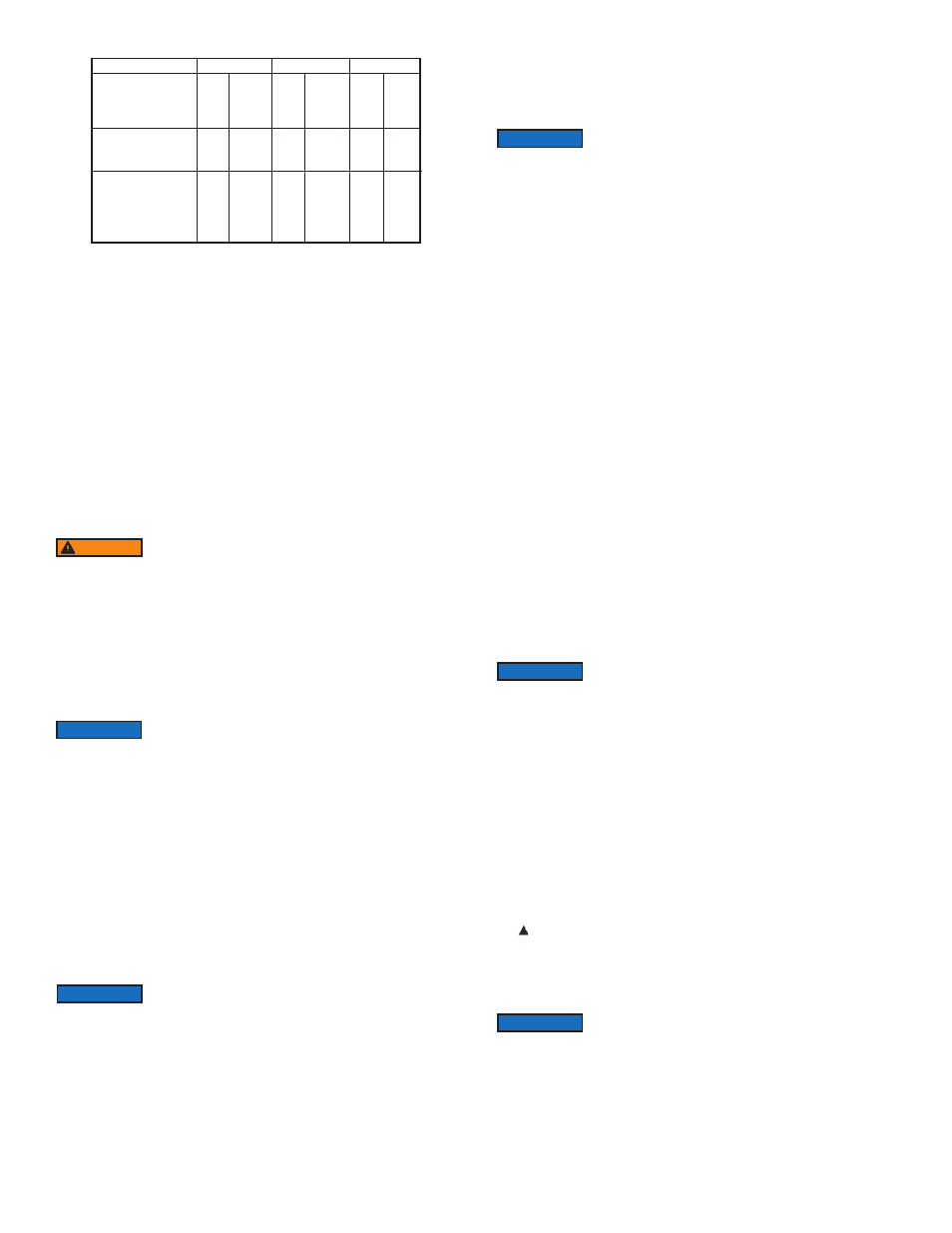
Table VI Analog Output Jumper Configuration
See APPENDIX IV for actual jumpers layout on the analog PCB.
6. MAINTENANCE
6.1 - Introduction
It is important that the Mass Flow Meter is used with clean, filtered gases only.
Liquids may not be metered. Since the RTD sensor consists, in part, of a small
capillary stainless steel tube, it is prone to occlusion due to impediments or gas
crystallization. Other flow passages are also easily obstructed. Therefore, great
care must be exercised to avoid the introduction of any potential flow impediment.
To protect the instrument, a 50 micron (10 L/min) or 60 micron (50 to 100 L/min)
filter is built into the inlet of the flow transducer. The filter screen and the flow paths
may require occasional cleaning as described below. There is no other
recommended maintenance required. It is good practice however, to keep the
meter away from vibration, hot or corrosive environments, and excessive RF or
magnetic interference. If periodic calibrations are required, they should be
performed by qualified personnel and calibrating instruments, as described in
section 7. It is recommended that units are returned to Dwyer
®
Instruments, Inc. for
repair service and calibration.
6.2 - Flow Path Cleaning
Before attempting any disassembly of the unit for cleaning, try inspecting the flow
paths by looking into the inlet and outlet ends of the meter for any debris that may
be clogging the flow through the meter. Remove debris as necessary. If the flow
path is clogged, proceed with steps below.
Do not attempt to disassemble the sensor. If blockage of the sensor tube is not
alleviated by flushing through with cleaning fluids, please return meter for servicing.
6.2.1 - Restrictor Flow Element (RFE)
The Restrictor Flow Element (RFE) is a precision flow divider inside the transducer
that splits the inlet gas flow by a preset amount to the sensor and main flow paths.
The particular RFE used in a given Mass Flow Meter depends on the gas and flow
range of the instrument.
6.2.2 - 10 L/min Models
Unscrew the inlet compression fitting of meter. Note that the Restrictor Flow
Element (RFE) is connected to the inlet fitting. Carefully disassemble the RFE from
the inlet connection. The 50 micron filter screen will now become visible. Push the
screen out through the inlet fitting. Clean or replace each of the removed parts as
necessary. If alcohol is used for cleaning, allow time for drying. Inspect the flow
path inside the transducer for any visible signs of contaminant. If necessary, flush
the flow path through with alcohol. Thoroughly dry the flow paths by flowing clean
dry gas through. Carefully re-install the RFE and inlet fitting, avoiding any twisting
and deforming the RFE. Be sure that no dust has collected on the O-ring seal.
6.2.3 - 50 to 100 L/min Models
Unscrew the four socket head cap screws (two 10-24 and two 6-32) at the inlet side
of the meter. This will release the short square block containing the inlet
compression fitting. The 60 micron filter screen will now become visible. Remove
the screen. DO NOT remove the RFE inside the flow transducer! Clean or replace
each of the removed parts as necessary. If alcohol is used for cleaning, allow time
for drying. Inspect the flow path inside the transducer for any visible signs of
contaminants. If necessary, flush the flow path through with alcohol. Thoroughly dry
the flow paths by flowing clean dry gas through. Re-install the inlet parts and filter
screen. Be sure that no dust has collected on the O-ring seal. It is advisable that at
least one calibration point be checked after re-installing the inlet fitting - see section
7.
7. CALIBRATION PROCEDURES
7.1 - Flow Calibration
Dwyer
®
Instruments, Inc. Flow Calibration Laboratory offers professional calibration
support for Mass Flow Meters, using precision calibrators under strictly controlled
conditions. NIST traceable calibrations are available. Calibrations can also be
performed at customers' sites using available standards. Factory calibrations are
performed using NIST traceable precision volumetric calibrators incorporating liquid
sealed frictionless actuators. Generally, calibrations are performed using dry
nitrogen gas. The calibration can then be corrected to the appropriate gas desired
based on relative correction [K] factors shown in the gas factor table (see
APPENDIX III). A reference gas, other than nitrogen, may be used to better
approximate the flow characteristics of certain gases. This practice is recommended
when a reference gas is found with thermodynamic properties similar to the actual
gas under consideration. The appropriate relative correction factor should be
recalculated (see section 9). It is standard practice to calibrate Mass Flow Meters
with dry nitrogen gas at 70.0°F (21.1°C), 20 psia (137.9 kPa absolute) inlet pressure
and 0 psig outlet pressure. It is best to calibrate GFM3/4 transducers to actual
operating conditions. Specific gas calibrations of non-toxic and non-corrosive gases
are available at specific conditions. Please contact your distributor or Dwyer
®
Instruments, Inc. for a price quotation.
It is recommended that a flow calibrator of at least four times better collective
accuracy than that of the Mass Flow Meter to be calibrated be used. Equipment
required for calibration includes: a flow calibration standard, PC with available RS-
485/RS-232 communication interface, a certified high sensitivity multi meter (for
analog output calibration only), an insulated (plastic) screwdriver, a flow regulator
(for example - metering needle valve) installed upstream from the Mass Flow
Meter, and a pressure regulated source of dry filtered nitrogen gas (or other
suitable reference gas). It is recommended to use Dwyer
®
Instruments, Inc.
supplied calibration and maintenance software to simplify the calibration process.
Gas and ambient temperature, as well as inlet and outlet pressure conditions
should be set up in accordance with actual operating conditions.
7.2 - Gas Flow Calibration of GFM3/4 Mass Flow Meters
GFM3/4 Mass Flow Meters may be field recalibrated/checked for the same range
they were originally factory calibrated for. When linearity adjustment is needed, or
flow range changes are being made, proceed to step 7.2.3. Flow range changes
may require a different Restrictor Flow Element (RFE). Consult your distributor or
Dwyer
®
Instruments, Inc. for more information.
7.2.1 - Connections and Initial Warm Up
Power up the Mass Flow Meter for at least 30 minutes prior to commencing the
calibration procedure. Establish digital RS-485/RS-232 communication between
PC (communication terminal) and the GFM3/4. Start Dwyer
®
Instruments, Inc.
supplied calibration and maintenance software on the PC.
7.2.2 - ZERO Check/Adjustment
Check SENSOR AVERAGE counts on the GFM3/4 LCD status line. Keep pressing
the ( ) [Up] button from the main screen until status line will display Device Sensor
Average ADC counts. With no flow conditions, the sensor Average reading must be
in the range 120 10 counts. If it is not, perform Auto Zero procedure (see section
5.3.10 "Zero Calibration").
7.2.3 - Gas Linearization Table Adjustment
Gas flow calibration parameters are stored in the Gas Dependent portion of the
EEPROM memory separately for each of 10 calibration tables. See APPENDIX I for
complete list of gas dependent variables.
Analog Signal
Flow Rate Output
Jumper Header J2
Temperature Output
Jumper Header J3
Pressure Output
Jumper Header J4
J2.A
J2.B
J2.C
J2.D
J3.A
J3.B
J3.C
J3.D
J4.A
J4.B
J4.C
J4.D
5 to 9
2 to 6
7 to 11
8 to 12
5 to 9
2 to 6
7 to 11
8 to 12
5 to 9
2 to 6
7 to 11
8 to 12
5 to 9
2 to 6
7 to 11
8 to 12
5 to 9
2 to 6
7 to 11
8 to 12
5 to 9
2 to 6
7 to 11
8 to 12
J2.A
J2.B
J2.C
J2.D
J3.A
J3.B
J3.C
J3.D
J4.A
J4.B
J4.C
J4.D
1 to 5
2 to 6
3 to 7
4 to 8
1 to 5
2 to 6
3 to 7
4 to 8
1 to 5
2 to 6
3 to 7
4 to 8
J2.A
J2.B
J2.C
J2.D
J3.A
J3.B
J3.C
J3.D
J4.A
J4.B
J4.C
J4.D
0 to 5 VDC
0 to 10 VDC
4 to 20 mA
DISASSEMBLY
MAY
COMPROMISE
CURRENT
CALIBRATION.
NOTICE
OVER TIGHTENING WILL DEFORM AND RENDER THE RFE
DEFECTIVE. IT IS ADVISABLE THAT AT LEAST ONE
CALIBRATION POINT BE CHECKED AFTER RE-INSTALLING THE INLET
FITTING.
NOTICE
REMOVAL OF THE FACTORY INSTALLED CALIBRATION
SEALS AND/OR ANY ADJUSTMENTS MADE TO THE
METER, AS DESCRIBED IN THIS SECTION, WILL VOID ANY CALIBRATION
WARRANTY APPLICABLE.
NOTICE
All adjustments in this section are made from the outside of the
meter via digital communication interface between a PC
(terminal) and GFM3/4. There is no need to disassemble any part of the instrument
or perform internal PCB component (potentiometers) adjustment.
NOTICE
Your GFM3/4 Digital Mass Flow Meter was calibrated at the
factory for the specified gas and full-scale flow range (see
device front label). There is no need to adjust the gas linearization table unless
linearity adjustment is needed, flow range has to be changed, or new additional
calibration is required. Any alteration of the gas linearization table will void
calibration warranty supplied with instrument!
NOTICE
Page 10
TO PROTECT SERVICING PERSONNEL IT IS MANDATORY
THAT ANY
INSTRUMENT
BEING
SERVICED
IS
COMPLETELY PURGED AND NEUTRALIZED OF TOXIC, BACTERIOLOGICALLY
INFECTED, CORROSIVE OR RADIOACTIVE CONTENTS.
WARNING