3 self-tuning 10, Cancelation 10 - 11, Start 10 – West Control Solutions KS 40-1 Burner User Manual
Page 10: 3 self-tuning
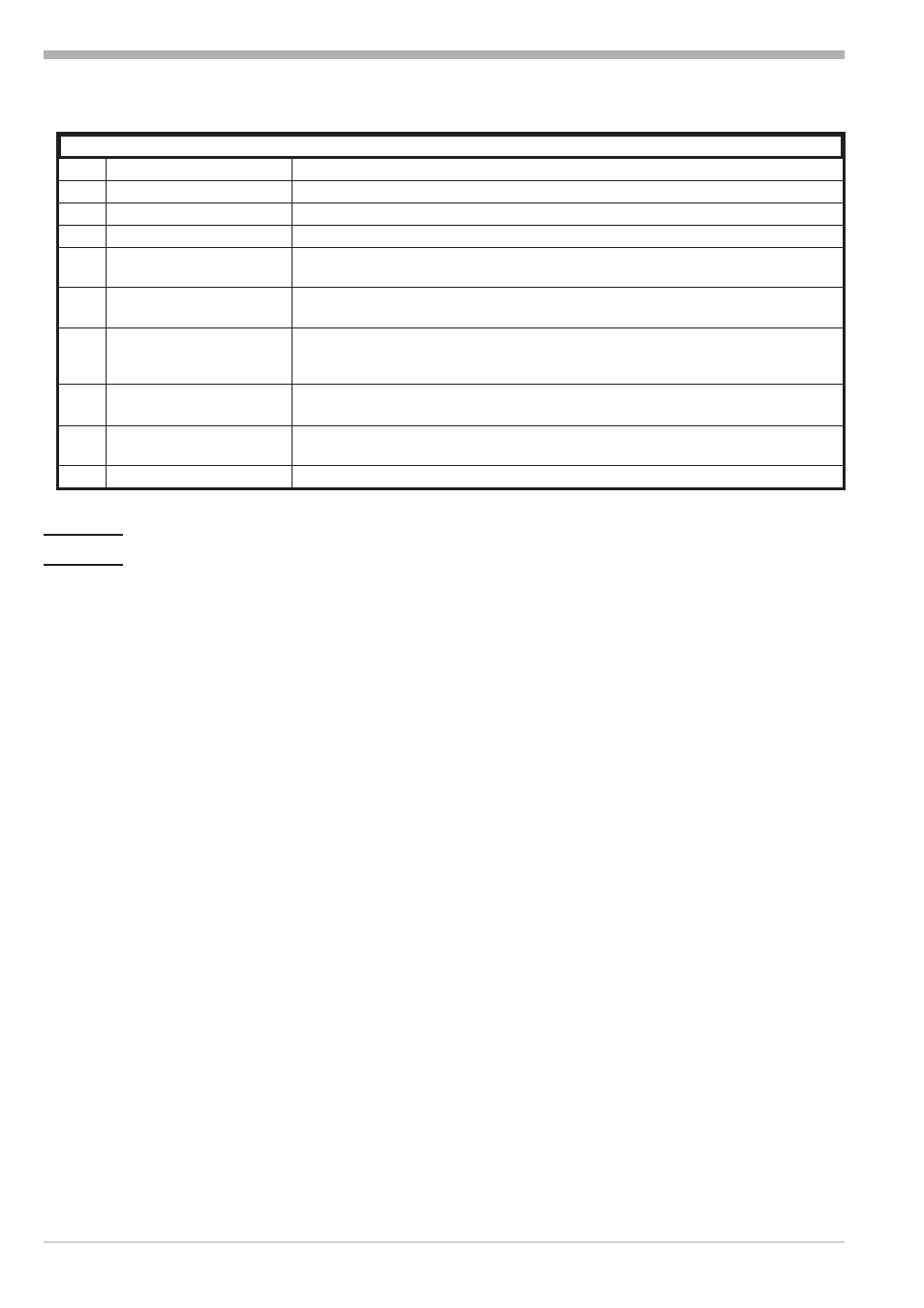
Error status (error status
3 - 9 only with error AdA.H / AdA.C ):
3.3 Self-tuning
After starting by the operator, the controller makes a self-tuning attempt. The
controller uses the process characteristics for quick line-out to the set-point wit-
hout overshoot.
g
ti and td are taken into account only, if they were not set to
OFFpreviously.
Self-tuning start
The operator can start self-tuning at any time. For this, keys Ù and È must be
pressed simultaneously. The AdA LED starts blinking.
The controller outputs 0% or
Y.Lo, waits until the process is at rest and starts
self-tuning (AdA LED lit permanently).
The self-tuning attempt is started when the following prerequisite is met:
w The difference between process value i set-point must be
³ 10% of the
set-point range (
SP.Hi - SP.LO) (with inverse action: process value smaller
than set-point, with direct action: process value higher than set-point).
After successful self-tuning, the AdA-LED is off and the controller continues
operating with the new control parameters.
Self-tuning cancellation by the operator:
Self-tuning can always be cancelled by the operator. For this, press Ù and È
key simultaneously. The controller continues operating with the old parameters in
automatic mode in the first case and in manual mode in the second case.
Operation
KS40-1 burner
10
Self-tuning
Error status
Signification
0 No error/message
not visible, except with acknowledgement
1 Stored error
Change to error status 0 after acknowledgement in error list
2 Existing error
Change to error status 1 after error removal
3
Faulty control action
Re-configure controller (inverse i direct)
4
No response of process
variable
The control loop is perhaps not closed: check sensor, connections and process
5
Low reversal point
Increase (
ADA.H) max. output limiting Y.Hi or decrease
(
ADA.C) min. output limiting Y.Lo
6
Danger of exceeded
set-point (parameter
determined)
If necessary, increase (inverse) or reduce (direct) set-point
7
Output step change too
small (dy > 5%)
Increase (
ADA.H) max. output limiting Y.Hi or reduce
(
ADA.C) min. output limiting Y.Lo
8
Set-point reserve too
small
Increase set-point (invers), reduce set-point (direct) or increase set-point
range (r
PArA / SEtp / SP.LO and SP.Hi )
9
Impulse tuning failed
The control loop is perhaps not closed: check sensor, connections and process