2 polynomial rtd – Pyromation Series 642 User Manual
Page 41
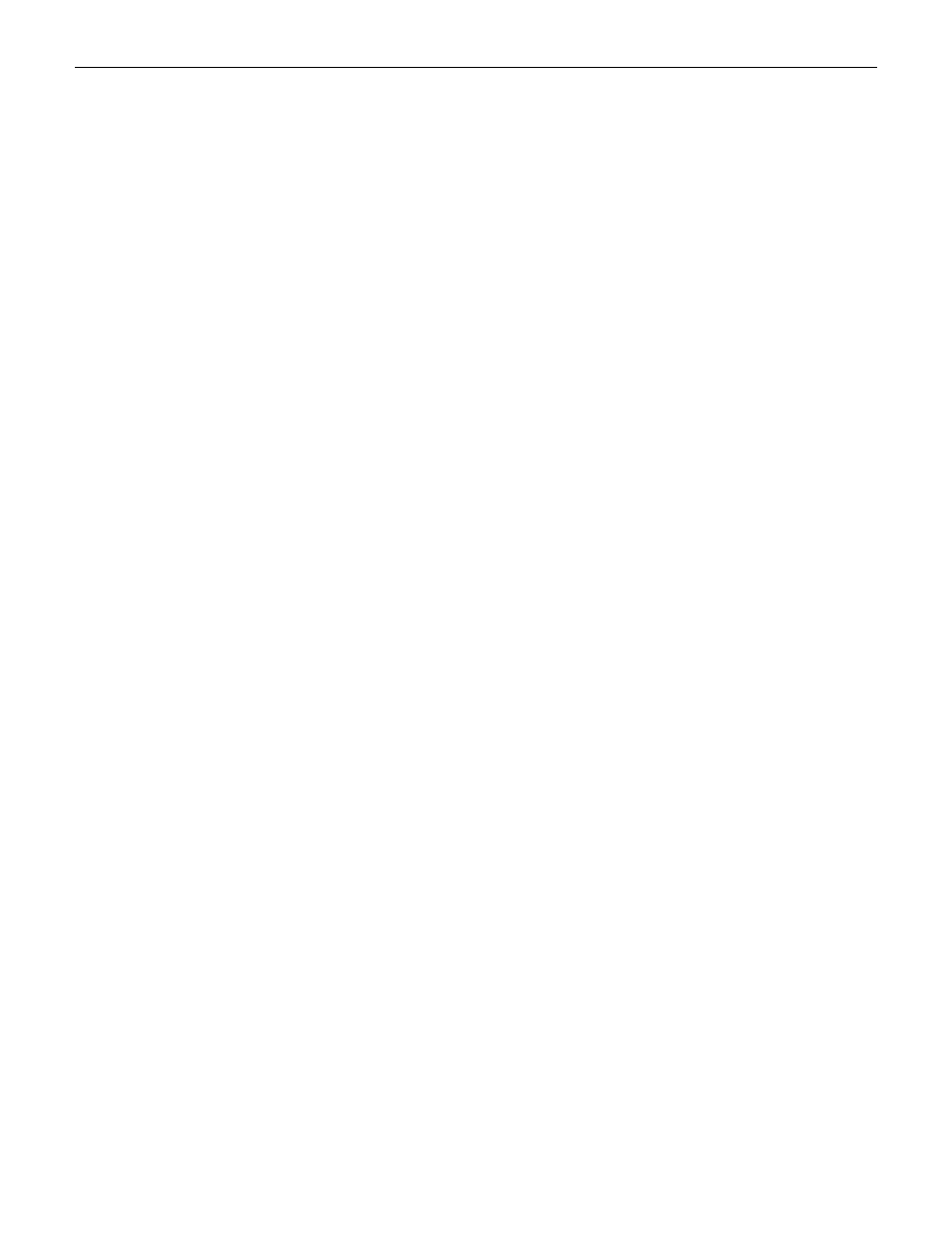
Series 642
Appendix
Pyromation, Inc.
41
10.2
Polynomial RTD
With "Polynomial RTD", the sensor is defined by a polynomial (X4*x
4
+X3*x
3
+X2*x
2
+X1*x
1
+X0)
with 5 coefficients. The physical measuring range is 10 to 400
Ω.
The 5 coefficients of the polynomial are calculated using the PC configuration software TransComm
Light. There are two different ways of determining the polynomial:
• The sensor-matching-calibration
The deviation (compared to standard RTD) of the sensor or at the complete measuring point
(transmitter with connected sensor, Measured =
ΔT /°C or mA) is measured at different
temperatures (sampling points). By using a "weight factor" it is possible to set special focus either
on the given points (the deviation on the rest of the curve can be quite high) or on the trend
compared to the reference linearization (The sampling points are only reference points of an e.g.
aged sensor). These sampling points lead to a new revised linearization, which is transferred to
the temperature transmitters.
• The customer specific linearization
The linearization is made by measured resistance or current values over the target temperature
range. These sampling points lead also to a new revised linearization, which is transferred to the
temperature transmitters.
10.2.1
How to use with the PC configuration software TransComm
Light:
1.
Select POLYNOM RTD in Choice-field "Sensor type".
2.
Press button LINEARIZATION to open module SMC32.
3.
Default setting is Sensor-matching-calibration which can be recognized by "
ΔT/°C" in the
groupbox "Measured". Alternative choice is "Ohm" or "mA" for customer specific linearization.
4.
Default reference RTD linearization is Pt100. Check "Type of Sensor" if another RTD is
required. With customer specific linearization it is not possible to select "Type of Sensor".
5.
"Weighting" default is 50%. As described above 100% means full focus on the accuracy at the
sampling points, 0% uses the sampling points as trend information for the complete curve.
6.
The "sampling points" can be edited in the shown table, default points are the min and max
temperature of the reference element. These values can be modified to a reduced range.
7.
To see the results of the new linearization use menu Calculate … Calculate Curve and/or
Calculate … Show Coefficients (Coefficients are shown in an extra form).
8.
The red curve in the graph (scale on right) shows the deviation between calculated and
reference curve. This graph easily shows the effect of changing the "weighting".
9.
When files exist, data can also be loaded (Data … Load). Files made with older versions (SW
< 2.0) do only supply sampling points, the extra information ("Measured", "Type of Sensor")
has to be edited after loading data.
10. Storing all data in files use Data … Save or Data … Save as....
11. For using this functionality in the transmitter please press OK (data will be taken over in the
PC configuration software TransComm Light) and start to transmit to the device.