Additional universal command specifications – KROHNE IFC 010 Converter HART User Manual
Page 8
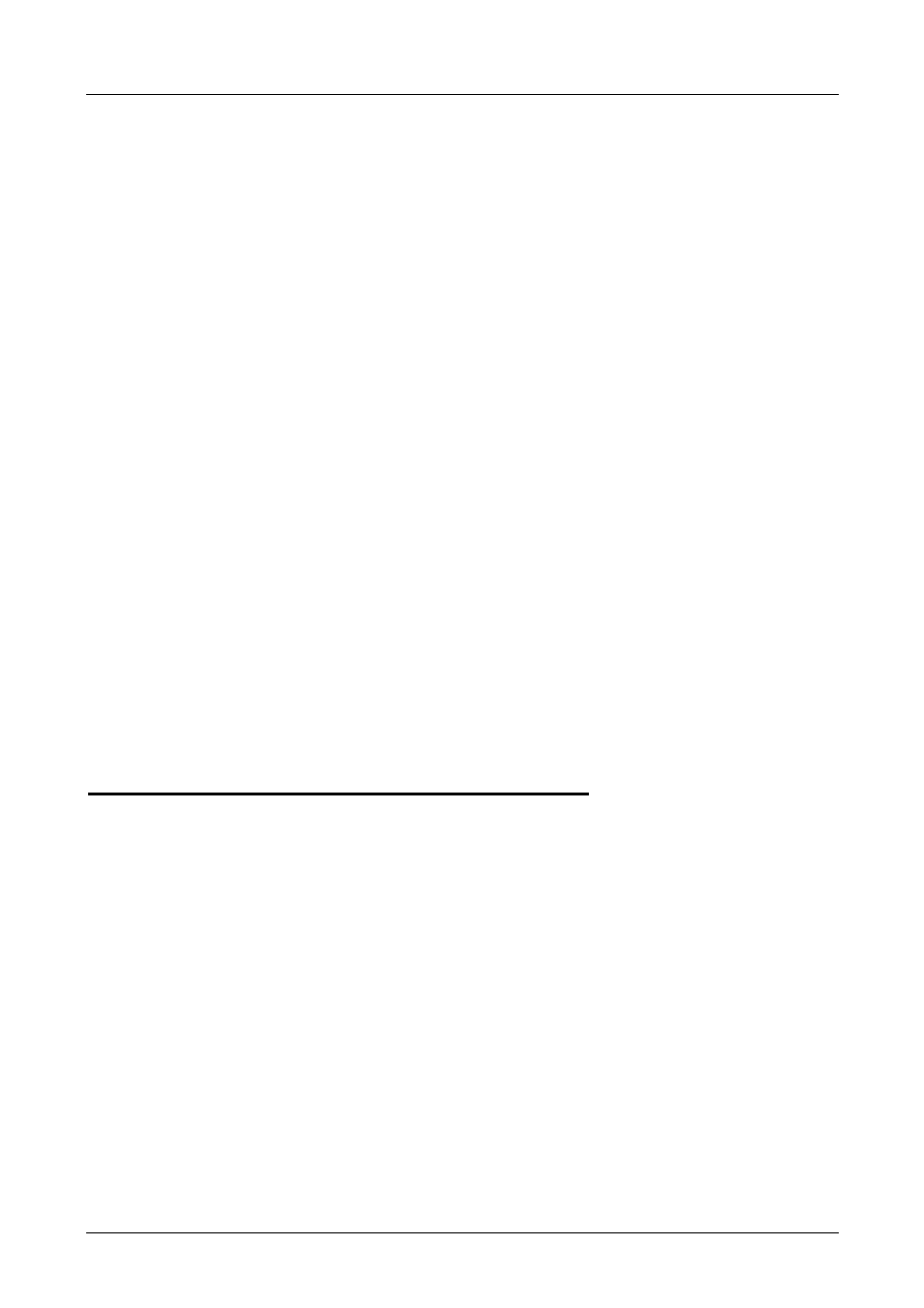
HARTÆ Communications Protocol
IFC010 Command Specification Rev: 1.0
Release Date: 29 May 1997
© 1997 KROHNE Mefltechnik D-47058 Duisburg
Page
8
SmoothedFlow is always mapped onto the current output, thus providing a fixed setting for Primary Variable. The
frequency/pulse output can deal with two possible assignments: RawFlow or SmoothedFlow. Therefore only values 0
and 1 are allowed as Secondary Variable code. Tertiary and Fourth Variables are mapped onto logical slots (no more
outputs) and can therefore accept any allowed value (0..3).
5.2 Damping
Implementation
The IFC010 transmitter implements damping on both the digital Primary Variable and its Analog Output. The Analog
Output is calculated from the digital Primary Variable.
The rest Dynamic Variables have either the same Damping Value as Primary Variable, or no damping. It depends on the
Secondary Variable Code (refer to Command #51, Write Dynamic Variable Assignments).
5.3
Nonvolatile Memory Data Storage
The Flags Byte of Command #0 will have Bit #1 (Command #39, EEPROM Control) set to 0, indicating that all data
sent to the transmitter will be saved automatically in the device EEPROM upon receipt of the Write- or Command-type
command, that require data storage. Command #39, EEPROM Control, is not implemented.
5.4
Multidrop Mode
This revision of the IFC010 supports Multidrop Mode.
5.5
Burst Mode
This revision of the IFC010 does not support Burst Mode.
6. Additional Universal Command Specifications
This section contains information pertaining to those commands that require clarification.
6.1
Command #0
Read Unique Identifier
Device Identification Number (Data bytes #9..#11 of response packet) is preserved in the instrument as a 4-bytes
number. Hence only three (low significant) bytes of this number are ìvisibleî to HART-requester.
6.2
Command #14
Read Primary Variable Sensor Information
Sensor serial number is not stored within device and therefore is responded as Ñnot applicable to deviceì (zero value).
Sensor parameters depend on the meter diameter and should be reread if the latter is changed.
6.3
Command #15
Read Primary Variable Output Information
Upper Range Value depends on the meter diameter. When the latter is changed, Upper Range Value will be
automatically corrected if needed. In the last case bus master will be prompted about compulsory changes in correlated
parameters via Warning-type Response Codes (refer to Command #131, Write Meter Diameter).