Warner Electric TCS-200-1H User Manual
Page 14
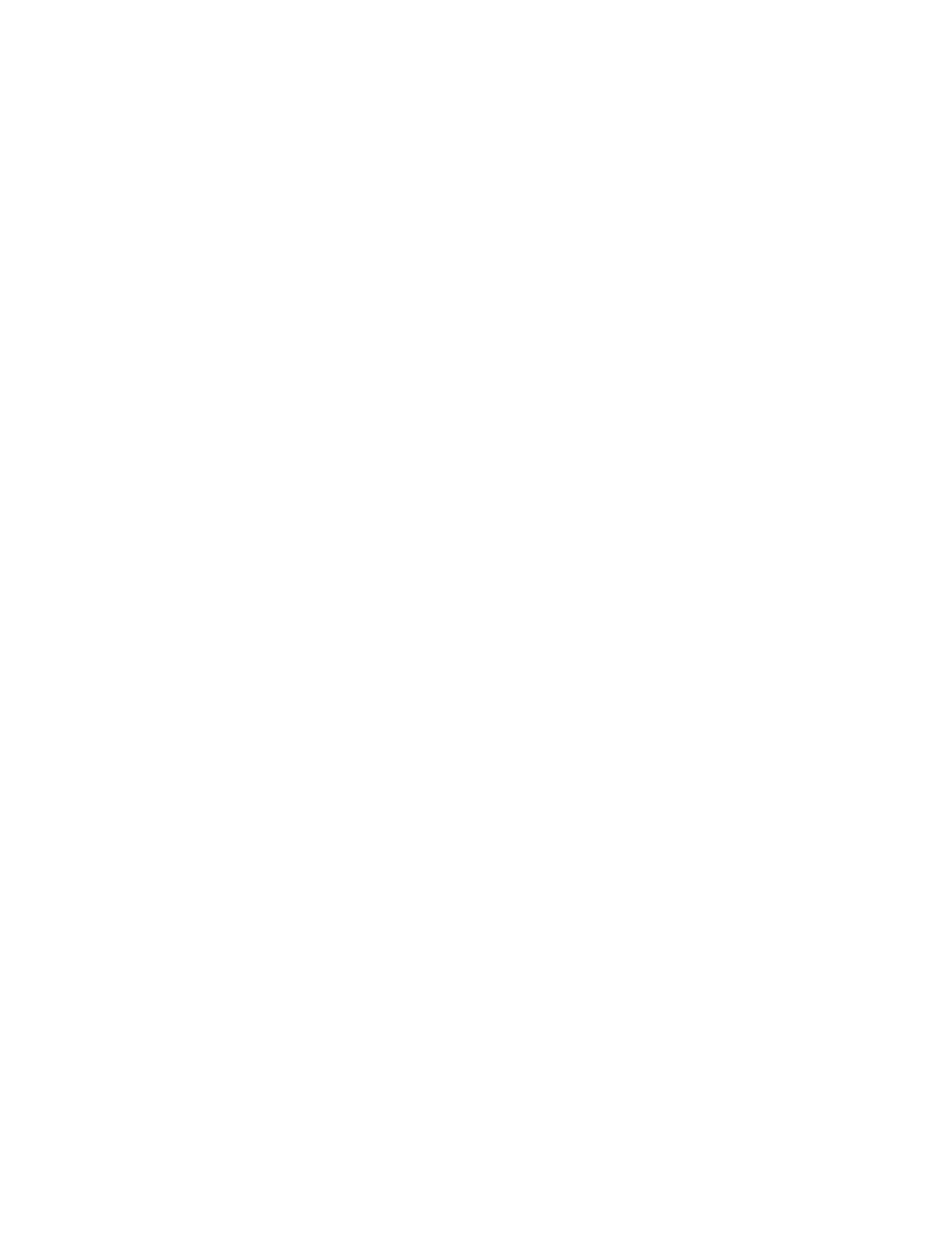
14
Warner Electric • 800-825-9050
P-2003-2 • 819-0420
o 15. Adjust the front panel tension adjust
potentiometer to the maximum output level
required for the application. Now set the remote
tension adjust potentiometer between maximum
and zero.
Note: If start-up and adjustment procedures do not
produce the desired results, consult the
troubleshooting section of this manual.
o 16. If a remote mode selector switch is used,
repeat steps 5 through 13 using the remote
mode selector switch.
o 17. Close the control front cover and latch it by
tightening the screw that is provided.
Roll Follower Tension Adjust
o 1. Apply power to the control system.
o 2. Check that the green LED marked "power" is
illuminated.
o 3. Using an AC voltmeter, measure the AC input
voltage at terminals 4 and 8 of terminal block
TB2. This voltage should be approximately 115
or 230 VAC, depending on the voltage chosen.
o 4. Remove power from the control system and
wait approximately 30 seconds before
proceeding to the next step.
Electro Disc Tension Brake
Note: If you are not using electro disc tension
brakes, proceed to step 5 under all other 2 wire
tension brake section.
o 5. Remove the sense magnet lead from terminal
1 of terminal block TB2 and insert a DC current
meter in series with the lead of the sense magnet
and terminal 1 of terminal block TB2.
Note: Use a DC current meter that reads 0 to 500
mA with the positive (+) lead connected to terminal 1
and the negative (-) lead connected to the wire.
o 6. Reapply power to the control system.
o 7. Set the mode selector switch to the brake
“off” position. The meter should read zero current
and the brake should free wheel.
o 8. Place the mode selector switch in the brake
“stop" position. The meter should read 345 to
375 mA and the brake should be locked.
o 9. Place the mode selector switch in the brake
"run" position and set the tension adjust
potentiometer to its maximum (fully clockwise)
setting.
Note: Refer to Table 1 for various inputs and outputs
when using the roll follower system
o 10. Connect a second DC voltmeter between
terminals 9 and 11 of terminal block TB1.
Note: Use a DC voltmeter capable of measuring zero
to 10 volts DC.
o 11. With the roll follower potentiometer
disconnected from the roll follower arm, position
the follower arm to its true zero position, which
should be the centerline of the unwind spindle.
o 12. Adjust the roll follower potentiometer to a
zero voltage reading on the voltmeter which is
connected per step 10, page 14.
o 13. Connect the roll follower potentiometer to the
roll follower arm. After coupling the follower arm
to the potentiometer, recheck the voltage
between terminals 9 and 11 of terminal block
TB1 to insure the voltage is still zero VDC.
o 14. Place a full roll of material on the unwind
stand.
o 15. Set the roll follower arm on the unwind roll.
o 16. Check the voltage between terminals 9 and
11 of terminal block TB1 and refer to Table 1. If
the voltage reading is less than 0.8 VDC, refer to
Table 1 for the nominal output current available.