Meter maintenance – Liquid Controls MS Meters User Manual
Page 16
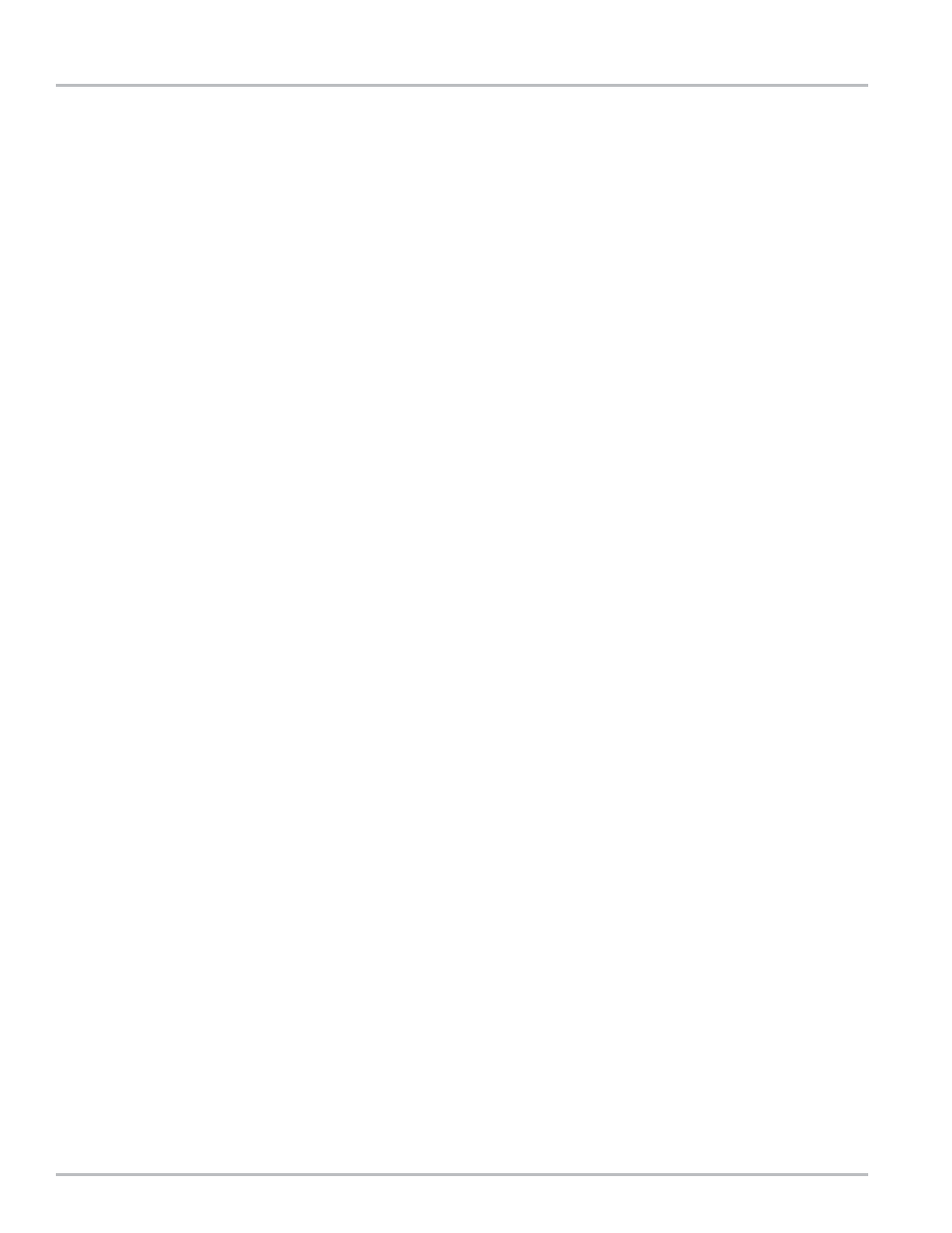
16
Meter Maintenance
Prevent pipe strain or stress from occurring when
making meter or accessory repairs. Pipe strain and stress
occur when the pipes are not supported or are not aligned
correctly to the meter. The weight of the pipes must
always be supported independent of the meter. This
means that the meter and accessories can easily be
removed without affecting the pipes or the pipe alignment.
Never leave any of the pipes hanging.
Seasonal meter storage. If the meter is used for
seasonal work, at the end of each season the meter
should be removed from the system and thoroughly
flushed with a compatible liquid. This includes removing
the drain on the front and rear covers. Then flush the
product from the front and rear covers. If flushing with
water is preferred, extra care should be taken to drain
the meter completely and to dry all internal parts.
Immediate refilling with a compatible liquid (or oil misting)
is essential to prevent corrosion as well as ice damage
to parts from moisture that was overlooked after flushing
and drying.
Do not mar or scratch any of the precision machined
surfaces by prying or sanding parts.
Torque specifications. All fasteners such as screws and
bolts should be torqued to proper specification. See the
“Torque Chart” on Page 31 of this manual.
Stone the machined surfaces when reassembling the
meter to assure that the machined surfaces are free of
burrs and mars.
Repair pulled threads with threaded insert fasteners.
These can be used in many instances. Contact your
full-service distributor for advice if this occurs.
Coating threads. When removing and replacing bolts
and castings in a meter, always coat the threads with
anti-seize.
Removing flange seals. When removing the flange
assembly, always carefully remove the O-ring seal. Make
sure that the flange surface is clean. Discard and replace
the old O-Ring seal if it is nicked or scratched in any
way. If it is undamaged, it can be reused.
Examine all fasteners. Make sure fasteners are not
bent, rusted, or have pulled threads. The threads should
all appear evenly placed. If the bolts are bent, check the
housing and bearing plate for flatness. Use a straight
edge to determine flatness.
Look for gaps. When disassembling a meter, use a feeler
gauge to check for gaps between the bearing plate and
housing. If you do find gaps, check the bearing plates for
flatness with a straight edge. Gaps can be caused by
shock problems that must be resolved. Contact your full-
service distributor or the Service Department at Liquid
Controls for assistance if this occurs.
Check the O-Rings. O-Rings should be smooth. Cracked
or worn O-Rings should be replaced. However, a more
serious problem of shock may have occurred if the O-
Rings look nibbled. Shock problems must be verified and
resolved. Contact your full-service distributor or the
Service Department at Liquid Controls for assistance if
this occurs.
Check the bearing plates. Check the bearing plates for
flatness. Use a straight edge. Warped bearing plates can
be caused by shock problems that must be resolved.
Contact your full-service distributor or the Service
Department at Liquid Controls for assistance if this
occurs.
Weights & Measures. Check with the regulatory agency
that governs Weights & Measures in your area. Removing
a seal wire may require Weights & Measures
recalibration.