System design considerations, Design for proper flow control, Design for thermal shock or expansion – Liquid Controls MS Meters User Manual
Page 10: Commissioning
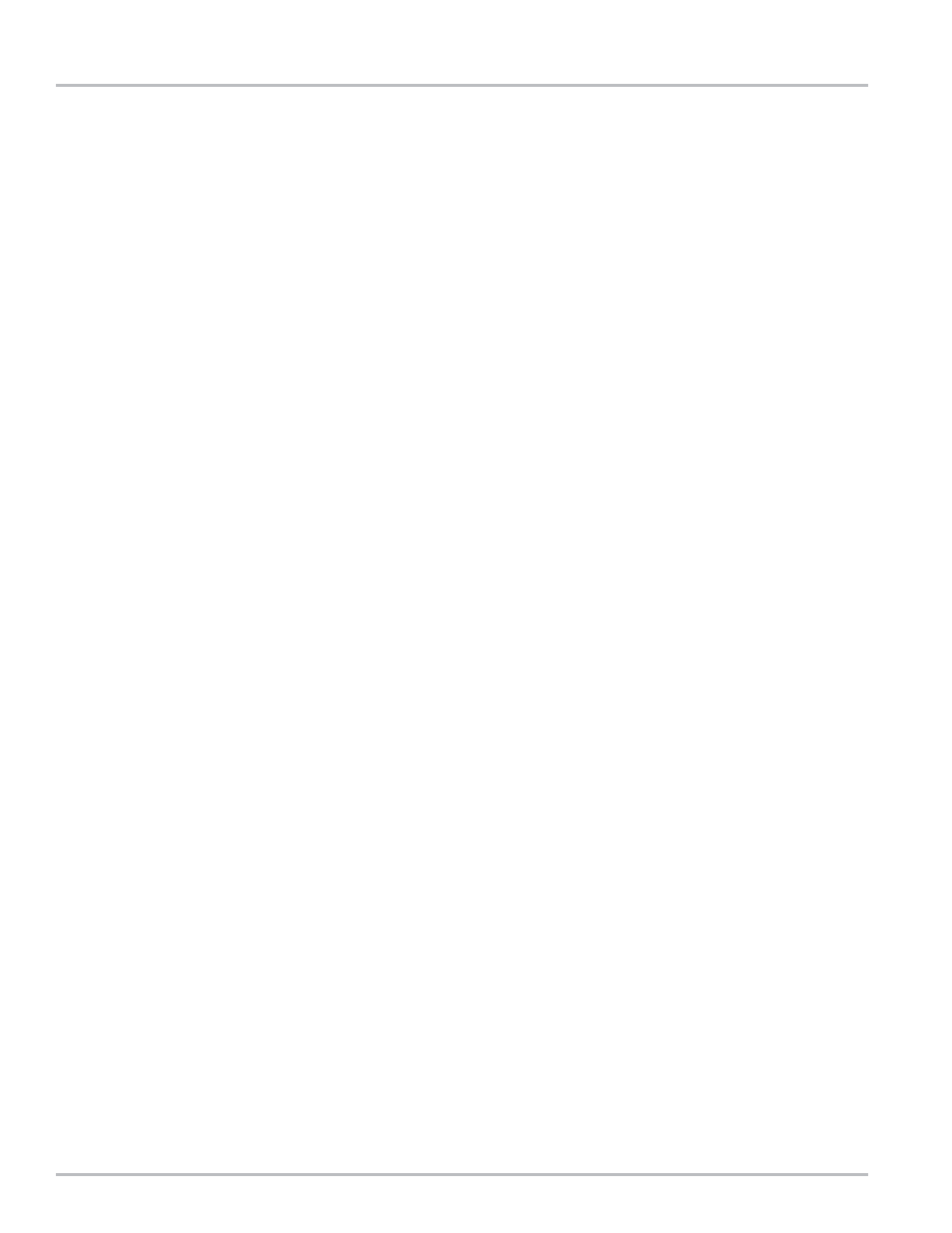
10
System Design Considerations
Design for Proper Flow Control
The example on Page 7 shows 152 meters monitoring
the delivery of 4 different products. Thirty eight meters
are used for delivery of HSD. Assume that one (1) pump
is selected to supply product to the meters. Each meter
measures 375 gallons per minute (GPM). The total flow
capacity of the pump must be:
38 X 375 GPM or 14,250 GPM.
Once the system is in operation, product flows through
the first meter when the control valve is opened. If the
flow rate is not regulated, 14,250 GPM attempts to flow
through the meter. The resulting overspeed will
immediately damage the meter. It is critically important
that a each meter location be equipped with a digital or
hydraulic flow rate controller. These valves must be
downstream of the meter to ensure that the meter remains
full of product at all times.
Control must also be used when beginning or stopping
flow. Proper control will minimize or eliminate transient
pressure conditions brought on by rapid velocity changes
in the system.
Design for Thermal Shock or
Expansion
Temperature considerations in system design should not
be ignored. Care must be taken in the design so that
zones are not created where fluid can be trapped or
locked between two closed valves. For every 1°F
increase in temperature, pressure in the trapped zone
will increase by an amount depending on the product in
the system (70 psi for LPG). A few degrees increase in
ambient temperature may create a serious problem if
thermal expansion pressure relief is not included in
regions where the product may be trapped. Typically,
the pressure setting in a thermal relief valve is set
approximately 10% higher than the nominal operating
pressure.
Commissioning
Once the metering system is installed, it is ready for
commissioning. Filling the system the first time requires
care and time. Ensure that the isolation valve on the
inlet side of the meter is closed. Pressure the header by
starting the pump. At the meter position to be
commissioned, “crack” or slightly open the inlet isolation
valve until flow into the meter can be heard. Allow the
inlet side to remain in this slightly opened position until
flow stops.
At this time, “crack” or loosen the pipe plug on top of the
meter case to allow air to bleed out. Once the air is
eliminated and product is present, fully tighten the plug.
Open the inlet side isolation valve completely. The
system must be kept full of fluid to avoid damage to the
meter. If air is allowed inside the metering element,
significant damage can occur as this air expands or
compresses due to system flow and pressure conditions.
In extreme cases, the presence of air can cause
catastrophic failure of the measuring element as a result
of liquid velocities and transient pressure spikes that can
bend or break critical measuring elements. The rate at
which the system is filled and pressurized must be
controlled to eliminate the possibility of creating any
pressure transients from excessive liquid velocity. Once
the meter and system are filled, pressurized, and free of
air, flow may begin.
Care must be taken during the initial flow condition to
prevent damage to the meter or strainer due to foreign
debris in the piping system. Foreign particles not removed
during flushing and hydrotesting will collect in the strainer
basket. Monitor the strainer differential pressure for the
first month of operation. Clean the strainer basket if
needed. Examine the strainer basket carefully and
replace if damaged.
Assure that the thermal relief valves are installed and
functioning properly.